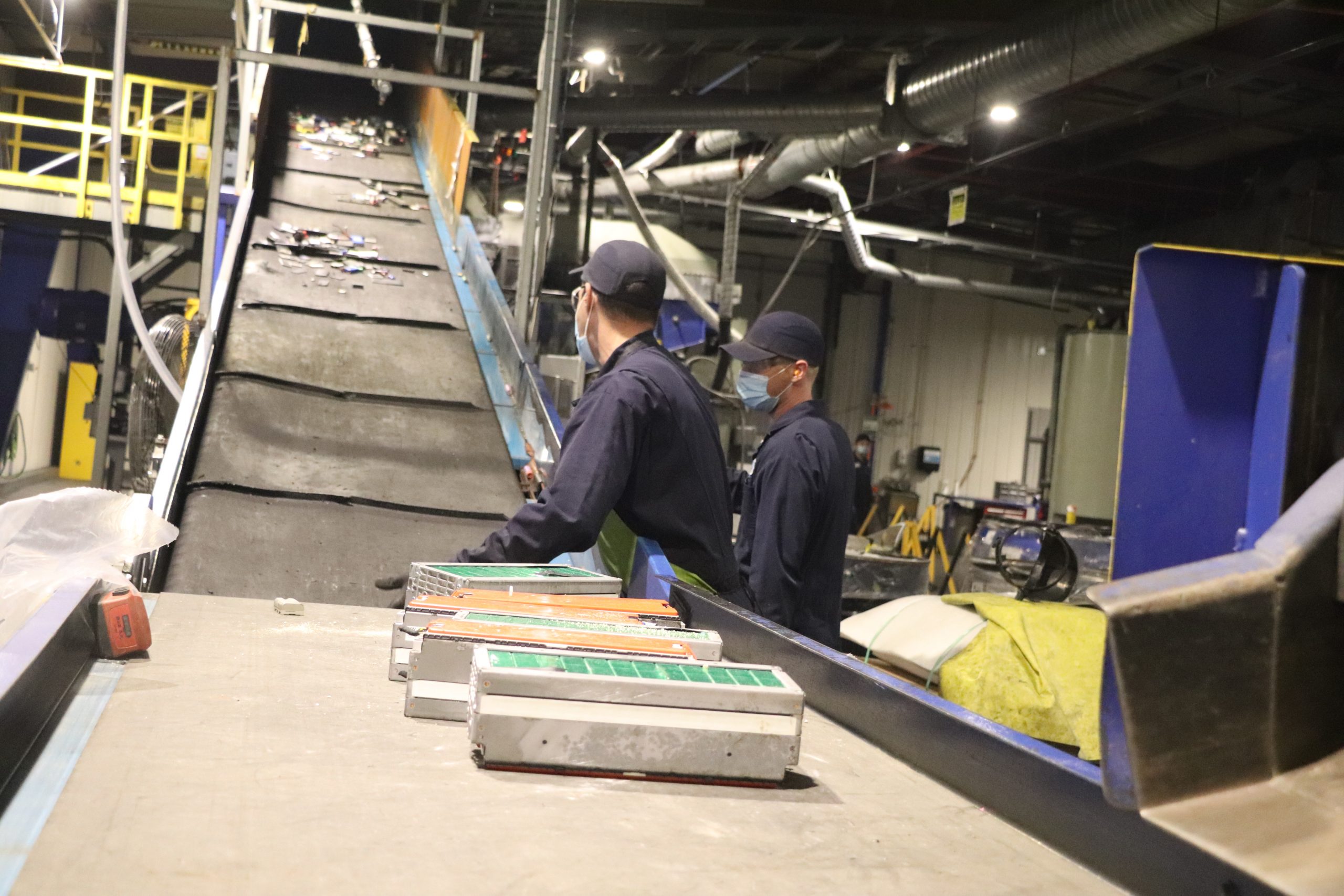
April 11, 2022
Lithium-ion battery recycler Li-Cycle expands operations
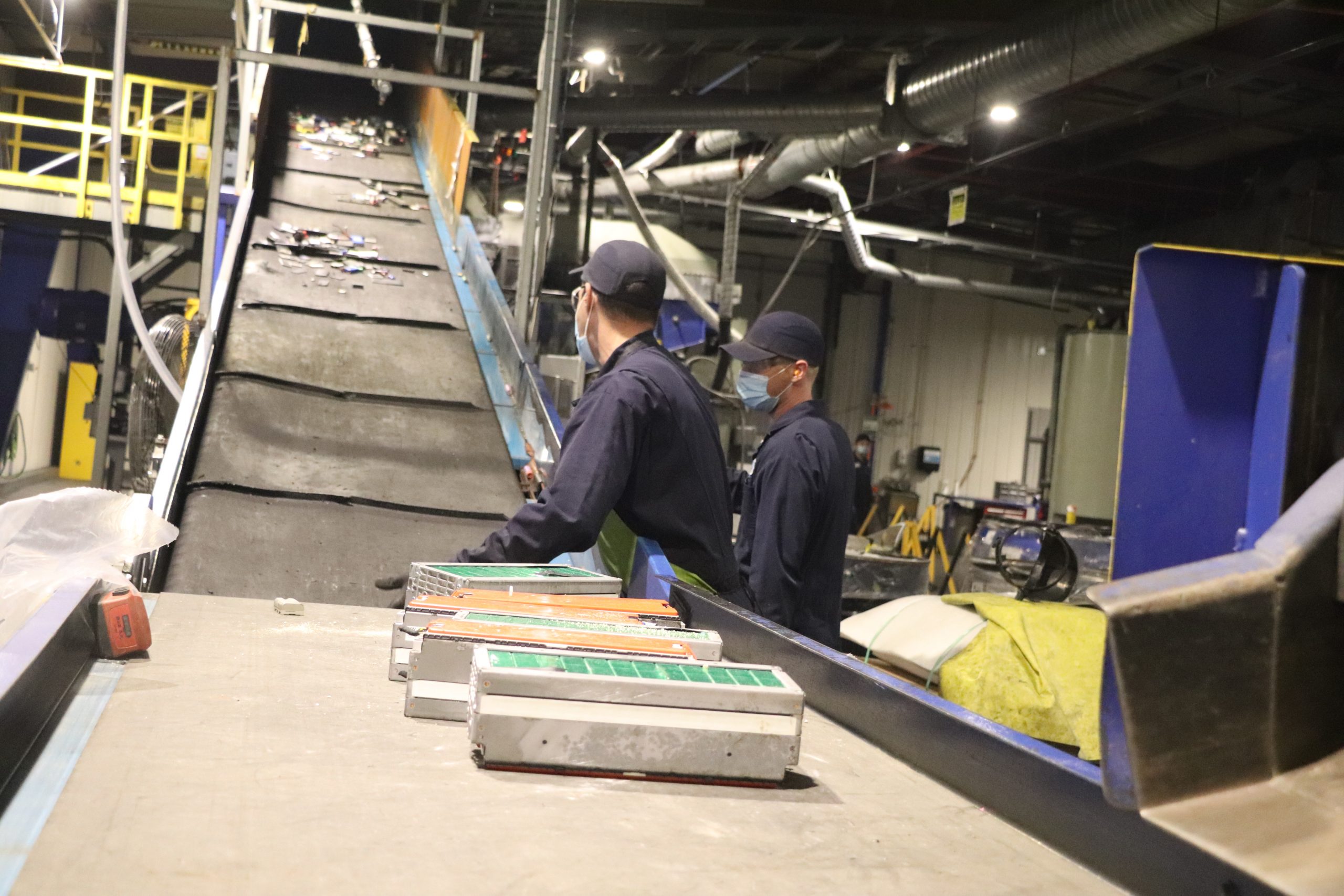
Li-Cycle Holdings Corp. considers its recycling technology the “missing link in the battery supply chain” as countries around the world increase reliance on electricity to reduce greenhouse gas emissions.
April 8, 2022
Original article published in Sustainable Biz
Mississauga-based Li-Cycle (LICY-N) plans on filling that void by aggressively scaling up its operations to recycle 65,000 tonnes of lithium-ion batteries by the end of 2023.
Founded in 2016, the company’s patented Spoke and Hub facilities can recycle all types of lithium batteries. They can also utilize the scrap discarded during battery production.
“Spoke” facilities collect and break down the waste batteries into recyclable elements. The “Hub” then takes the byproduct and turns it into reusable materials.
“As the world continues to electrify, the need for environmentally and economically sustainable recycling solutions will only continue to accelerate,” said Tim Johnston, Li-Cycle’s co-founder and executive chairman, in an email interview with Sustainable Biz. “In line with the rapidly growing demand for lithium-ion battery recycling, our goal is to continue to grow in lockstep with our customers.”
Li-Cycle wants ‘truly circular’ battery supply chain
Li-Cycle boasts of being able to recover up to 95 per cent of all that material, thanks to a low-temperature recycling process.
Its internal data also estimates the recycling process produces 70 per cent less carbon emissions compared to traditional battery recycling. The goal is to become a key player in a “truly circular” lithium-ion battery supply chain.
Li-Cycle currently operates two facilities – in Kingston, Ont., and New York State – which are each processing 5,000 tonnes annually of waste batteries. From now through 2023, it plans to add several more facilities to bring it to the 65,000 tonnes of capacity.
Facilities in Arizona and Alabama are scheduled to come online in Q2 and Q3 of this year, bringing the company’s capacity to 30,000 tonnes by the end of 2022.
In 2023 it plans to complete facilities in Ohio, Norway and Germany. The Ohio location will process 15,000 tonnes of waste, while the operations in Norway and Germany will handle 10,000 tonnes apiece.
Li-Cycle’s expansion also includes a recently announced larger facility in Kingston as well asplans to bring its first commercial Hub in Rochester, N.Y. fully online in 2023. The Rochester facility is expected to be the first commercial hydrometallurgical battery resource recovery facility in North America.
The recycling process
At Li-Cycle’s Spoke facilities, the lithium-ion battery material is put through a proprietary submerged shredding process.
This converts the material into three main product streams: plastics, copper/aluminum, and a substance called “black mass” which contains metals essential to battery production including lithium carbonate, nickel sulfate and cobalt sulfate. Other marketable metals in black mass include graphite, copper and aluminum.
The same process can be used to break down the five to 10 per cent of waste from the original battery manufacturing process.
When the Arizona and Alabama facilities are completed, Li-Cycle’s four locations are expected to produce 10,500 to 19,500 tonnes of black mass annually.
A company presentation says the process is “recycling agnostic,” meaning it is able to recycle all battery chemistries. Further, the batteries can come from anywhere, from earbuds to electric vehicles.
Johnston calls the company’s low-temperature approach “. . . very advantageous compared to traditional recycling processes that utilize extreme heat and typically burn off half of the materials.”
The black mass taken to the company’s Hub facility in Rochester will be broken down to produce new materials, which will be sold for use in fresh batteries. The same company presentation estimates the Rochester Hub will process 35,000 tonnes of black mass annually once it is fully operating.
The Rochester Hub is being constructed by MasTec Industrial, an infrastructure construction company headquartered in Coral Gables, Fla.
Li-Cycle predicts the global lithium-ion battery recycling industry could have more than three million tonnes annually available for recycling by 2030. Li-Cycle’s website predicts a cumulative 15 million tonnes of lithium-ion batteries will have reached end of life globally by the same year.
The Kingston expansion
The company’s first Kingston Spoke facility was constructed in 2019. Initially, it was producing 2,500 tonnes annually before a 2020 upgrade to 5,000 tonnes.
The new facility, announced in March, will be the first occupant of Kingston’s Clogg’s Road business park. Li-Cycle paid $5 million for the site, and will occupy about 12 of its 47 hectares. It’s expected to be operational in early 2023.
“Our new Centre of Excellence at Clogg’s Road business park will enable us to bring both our warehouse as well as our Spoke facility under the same roof, which will further optimize recycling logistics,” Johnston said.
“Kingston is also conveniently located between the Ontario and Quebec markets, which have experienced significant electric vehicle penetration and are expected to produce large quantities of lithium-ion battery material that will require recycling.”
When asked about the potential for further Canadian expansions, Johnston replied the company “is constantly exploring the best options to help us to further fuel our growth.”