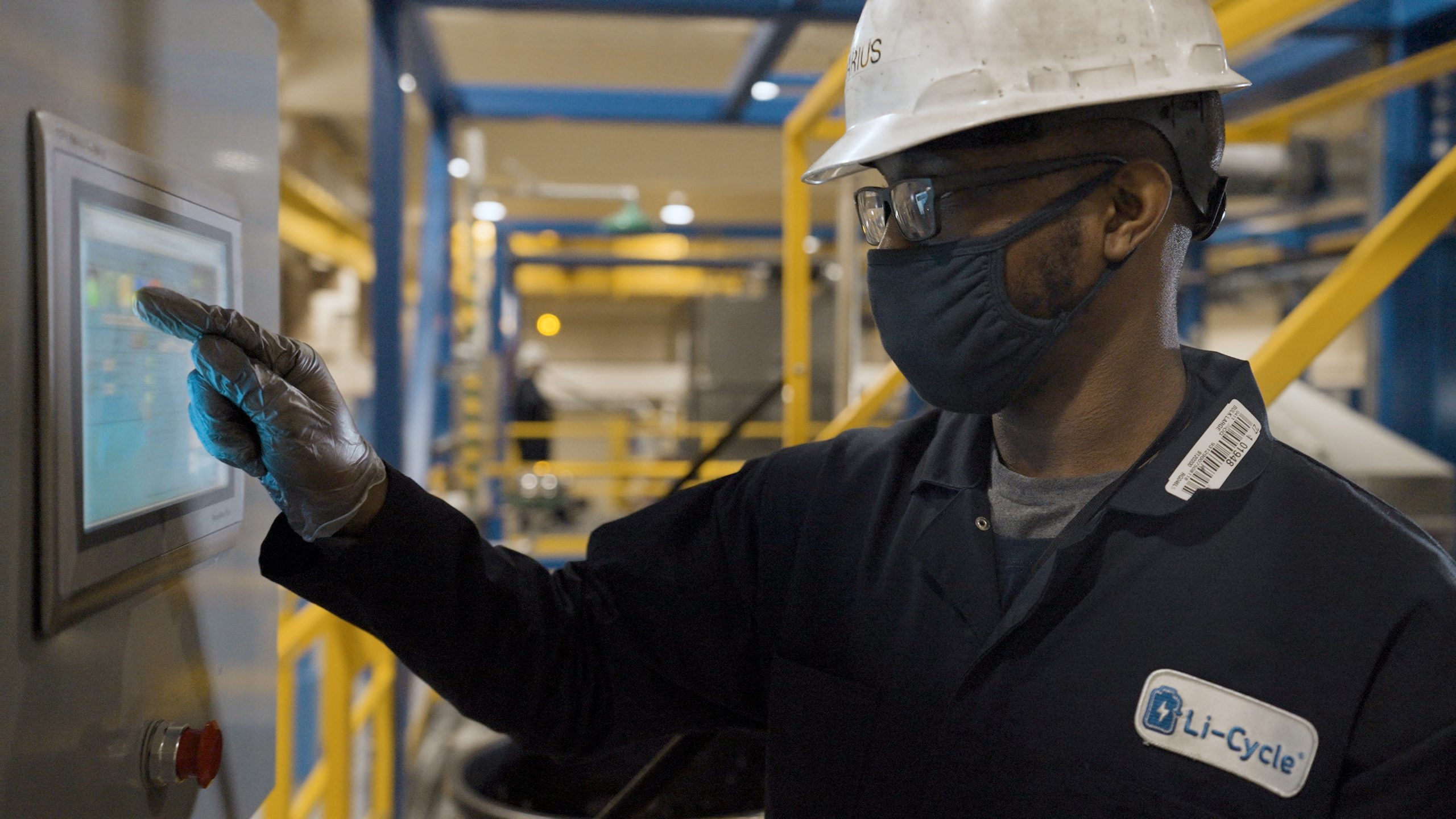
June 13, 2022
EV battery recycling is costly. These five startups could change that
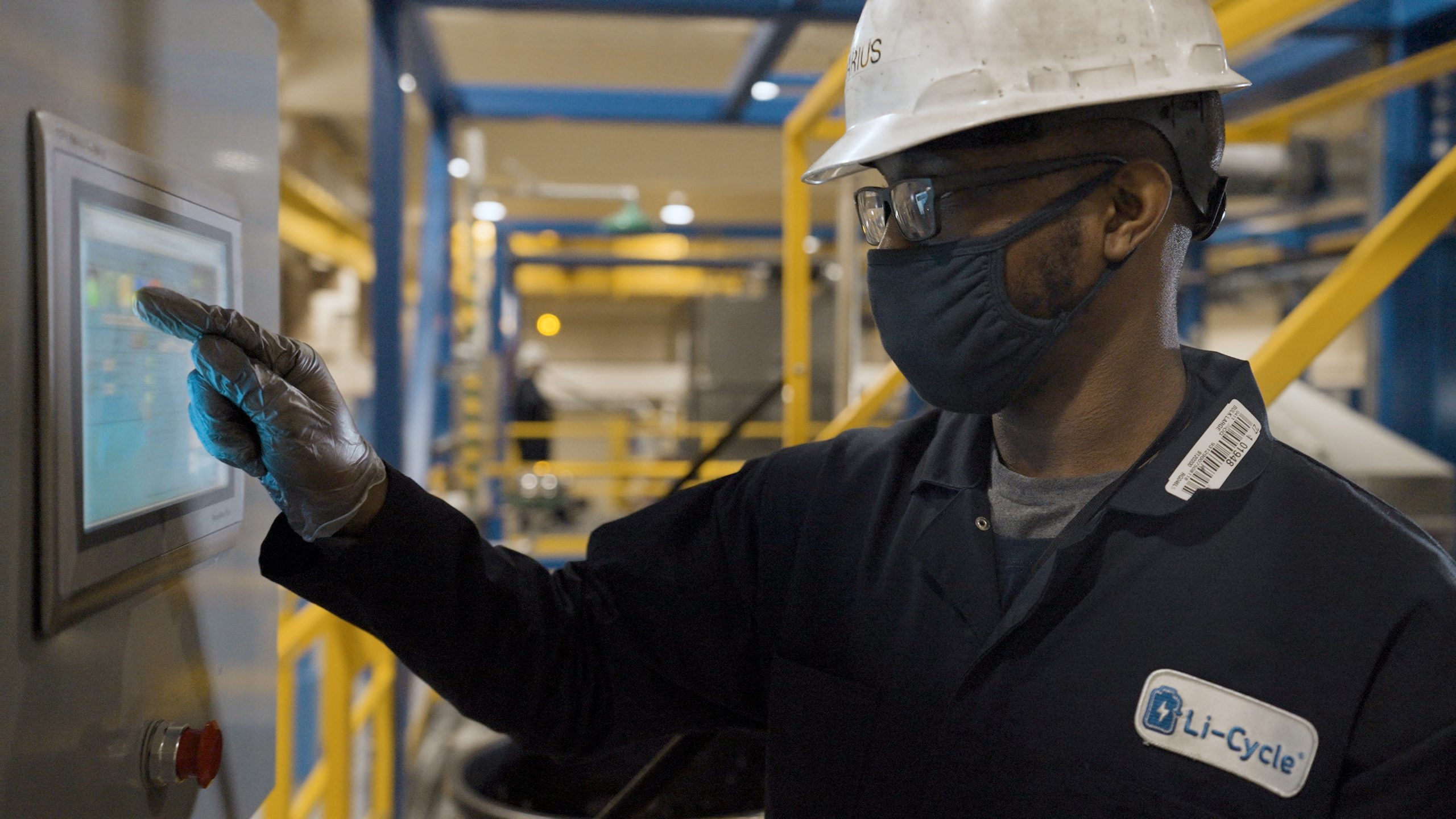
Meet the American companies making lithium-ion battery recycling more profitable and sustainable than it’s ever been.
June 13, 2022
Original article published in Canary Media
The public is finally buying electric vehicles in substantial numbers, a pivotal step toward decarbonizing transportation. But without changes to how the industry does business, the surge in EVs could eventually leave the planet awash in the batteries that make them run.
Lithium-ion batteries already power phones, laptops, scooters, e-bikes and toothbrushes. But global battery manufacturing is growing rapidly to serve the newly voracious demand for electric cars, which hit a record 8.6 percent of global new car sales in 2021.
Now that the growth trajectory is clear for battery-powered cars, the clean energy industry needs to figure out how to deal with the ensuing waste. Lithium-ion batteries contain materials that shouldn’t be dumped in a landfill, and old batteries can catch fire if they aren’t cared for properly. But so far battery recycling technology and processing capacity has lagged far behind manufacturing.
It’s possible to pay someone to cart off old batteries and dispose of them as a hazardous waste stream. But this adds cost to the battery life cycle. That’s because traditional methods for breaking down batteries, including pyrometallurgy and hydrometallurgy, are expensive and time-consuming and don’t recapture all of the valuable material inside.
Pyrometallurgy involves chucking batteries into a furnace to burn off much of their content; the smoldering remains get sold to smelters who use the trace nickel and cobalt.
Hydrometallurgy uses chemistry to reclaim metals after mechanically shredding batteries into little bits (see video below). This sometimes requires painstaking manual labor to break down large packs beforehand.
These methods don’t recover anything close to the amount of material needed to make a new battery, even though all the fixings for a new battery exist in an old battery. Old-school recycling facilities often don’t even reclaim the lithium — they just weren’t set up to do that.
Now, though, a number of startups are commercializing cleaner and more efficient recycling techniques, and building dedicated lithium-ion battery recycling factories at an unprecedented scale. Many of the founders come armed with experience they gained from prior stints in battery manufacturing. And in just the last year or two, they’ve raised a boatload of cash from investors who sense an opportunity to make battery recycling profitable.
“I’ve worked in this space for 22 years, and last year looked significantly different than the previous 21,” said Shane Thompson, president of long-running recycling company Retriev Technologies. As for the next decade? “Buckle up,” he said.
Recycling capacity has lagged battery production in part because it takes years of operating an EV before its battery pack needs disposal, and electric vehicles are still a pretty new mass-market trend. But this new cohort of recyclers doesn’t have to wait for electric vehicles to hit critical mass. They’ve got plenty to hone their techniques on with existing consumer electronics waste, plus the scrap from new battery manufacturing.
“It is absolutely a solvable problem,” Li-Cycle CEO and co-founder Ajay Kochhar said of the recycling challenge. “Companies like us exist, and our whole premise is to make this economically and environmentally beneficial.”
Here’s a sampling of five up-and-coming startups making battery recycling more efficient, clean and profitable. If they succeed, they’ll help prepare the world for the EV revolution.
ABTC: Take batteries apart the way they are put together
Instead of shredding or burning batteries, why not run the manufacturing process in reverse?
That’s the elegant insight that informs how the American Battery Technology Company approaches battery recycling. The team there knows how to put batteries together because they helped Tesla set up its Nevada Gigafactory. One of Ryan Melsert’s jobs was to vet prospective recyclers to responsibly dispose of waste from the battery manufacturing process.
“After seeing the state of the industry in North America and how there was such a void of competitive and responsible operations, that’s what led my team and [me] to leave Tesla” and fill that void, said Melsert, now CEO and CTO of ABTC.
Melsert and company decided to enhance battery recycling by programming off-the-shelf manufacturing machines to disassemble instead of assemble. The machines take battery packs and break them back down to cells, and then pick apart the anodes, cathodes and separators.
At that point, the company applies its chemical know-how to extract the materials needed to make new batteries. (The team also uses these techniques to harvest new minerals from the company’s mining operations.) The mechanized process increases the amount of recovered materials, while reducing the costs of processing.
“By doing it strategically, we’ve been able to dramatically lower the amount of chemical agents we needed in the separation process,” Melsert said. That reduces a dominant cost of mineral recovery: buying the acids, caustics, solvents and oxidizers that extract useful materials.
ABTC then refines the materials for use in new batteries and sells them as a domestic source of critical minerals.
The company has tested its techniques in lab settings and in high throughput trials at equipment manufacturer sites and currently is building its first pre-commercial-scale plant in Reno, Nevada. That one will take in 20,000 tonnes of batteries per year — if it works, the next plant will use the same extraction technologies and processes at 10 times the scale.
Battery recycling “is solvable, but it still requires putting effort in and building commercial scale facilities,” he said.
Li-Cycle: Break down whole packs, recycle all the metals
Traditional battery recycling does not revolve around recovering the ingredients to make new batteries. In many cases, the goal is to pull out just the nickel and cobalt and forget the rest. When it comes to EV batteries, though, this approach means wasting the lithium, so a number of startups are experimenting with more thorough processes that allow them to extract this valuable mineral.
“Sometimes these things are obvious, but they just take time to develop and scale up,” Li-Cycle’s Kochhar said.
His company, which has more than 300 employees, opened a factory in Arizona in May that breaks down battery packs in a newly efficient way.
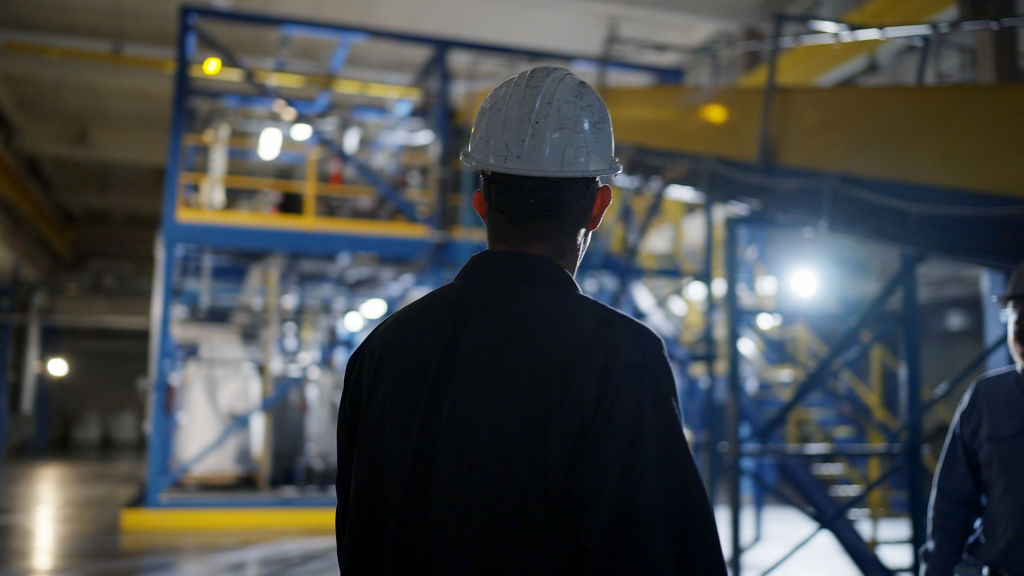
“We don’t dismantle, we don’t discharge — our Arizona plant takes a full pack into the shredder,” Kochhar said. That shredding happens with batteries submerged in a solution to tamp down fire risk. The facility sifts out aluminum, copper and plastics, which get recycled. That leaves a mishmash of battery materials known in the industry as “black mass.”
Li-Cycle will send black mass from Arizona and other “spoke” sites to a “hub” facility under construction in Rochester, New York. There the company will use hydrometallurgy to isolate the metals that can go into new batteries. Instead of trashing much of the recovered battery material and then wondering why recycling isn’t profitable, Li-Cycle tries to get everything out.
In the long term, Li-Cycle aspires to make recycled battery materials cheaper than the mined alternative.
“That’s totally possible, and that absolutely will help in terms of all of these pains that have been incurred in the scale-up of batteries,” Kochhar said.
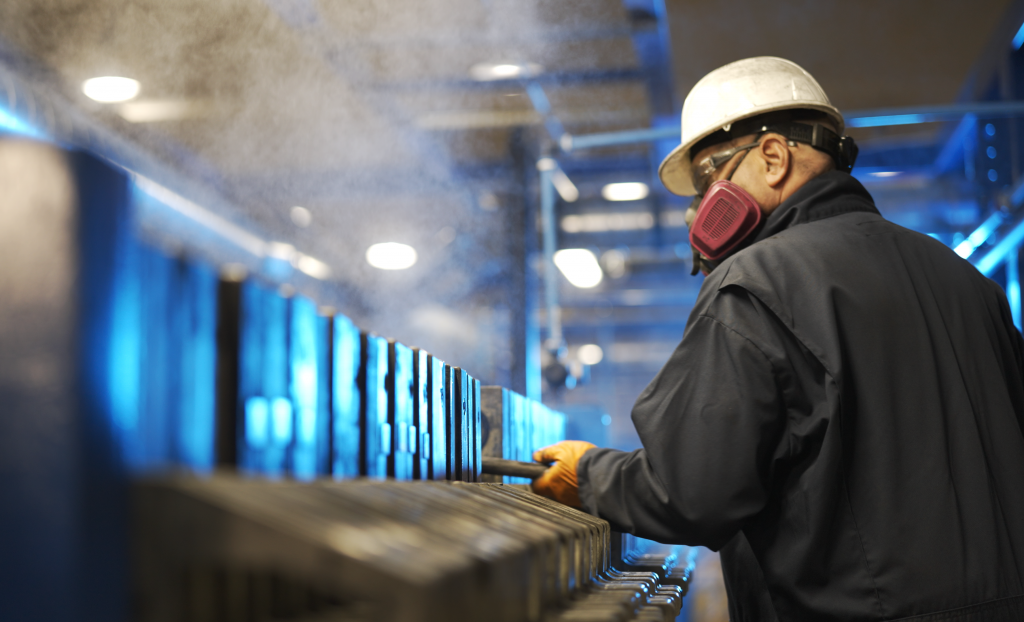
It remains to be seen if and when that vision comes true. But in the meantime, Li-Cycle enjoys ample funding to carry it forward. Mining conglomerate Glencore invested $200 million in May, and Koch Strategic Platforms invested $100 million last September, both in the form of convertible notes.
Ascend Elements: Turn old cathodes into new cathodes
Michael O’Kronley knew he could get more out of old batteries than the mixed metal slag that emerges from pyrometallurgy. And he wanted to get more than the commodity metals that conventional hydrometallurgy recovers from shredded battery parts.
“We want to make the highest-value material possible from spent lithium-ion batteries,” said O’Kronley, who runs Ascend Elements, a closed-loop recycling firm founded in 2015.
The most expensive part of a new battery is the cathode. Today cathodes are made by mining and processing lithium and metals such as nickel, manganese and cobalt. But an old battery contains all the necessary ingredients. It’s just a question of getting them out and back into a fresh, usable form.
Ascend scientists riffed on traditional hydrometallurgy and created a process they call “hydro to cathode.” They shred batteries and put them in solution. Instead of pulling out individual metals, they extract impurities from the liquid and leave behind only cathode ingredients in their pure atomic state. Then the scientists can adjust the ratio of metals in the cathode material based on what the customer is looking for. They precipitate out nickel manganese cobalt hydroxide, a cathode precursor. Adding lithium to that yields new cathode active material.
This process yields cheaper battery materials than mining and refining virgin ores from the ground, O’Kronley said. But Ascend still has to build up its factory capacity and prove to customers its materials are just as good as conventional batteries.
It got a boost in that effort from a study published last year in the journal Joule. Researchers, including scientists at Argonne National Lab, tested Ascend’s materials and found “the recycled material outperforms commercially available equivalent.”
Low cost is a valuable competitive edge in the battery market. But recycled cathodes have even greater benefits in terms of environmental impact. They help avoid carbon-intensive mining and shipping, and the recycling process itself can run on clean electricity.
“Our carbon footprint is…90 percent lower than [manufacturing] cathode material from virgin sources,” O’Kronley said. “It’s going to dramatically change the equation of the CO2 footprint of a new EV, and that’s incredibly important for the industry going forward.”
Ascend has been doing this at pilot plants in Massachusetts and Michigan over the last few years. Now it’s building a commercial recycling plant in Covington, Georgia that will open later this year. That facility will shred spent batteries and pull lithium, cobalt and nickel salts from the mass. A second factory, coming online in early 2024, will take the metals and turn them into complete cathode active materials. The company raised $20 million in a Series B funding round in 2021 and another $70 million later that year to fund these efforts.
There are plenty of vetted technological improvements in battery recycling, O’Kronley said. The problem is that very little recycling capacity has been built.
“As we’re building these gigafactories, we need to be building giga recycling factories alongside that,” he said.
Redwood Materials: Use stored energy to power the recycling
Old batteries typically arrive at recycling facilities with some residual energy stored in them. Many recyclers then spend time and money emptying them of charge so their materials can be extracted safely.
Redwood Materials, the extremely well-funded startup led by Tesla co-founder and CTO JB Straubel, thinks that’s a waste. The Reno, Nevada company figured out a way to convert the stored electricity into heat for a low-temperature calcination process that extracts electrolyte from old battery cells.
This and a slew of other proprietary techniques pull out upward of 95 percent of the battery materials, said spokesperson Alexis Georgeson. Today, the company turns those materials into “battery intermediates,” the metals that go into new battery production. But the plan is to manufacture new copper foil, and eventually anode and cathode materials, in-house.
“We’re a battery materials company that’s using recycled content to help make battery materials as sustainable as possible,” Georgeson said.
Energy is one of the major inputs for a recycling operation. Harnessing the energy in the batteries themselves reduces the energy bill. Redwood powers the rest of its operation with renewable electricity, spokesperson Georgeson noted.
KULR: Make it safe and cheap to transport old batteries
The costs of recycling start to accrue before old EV batteries even arrive at a facility.
Used lithium-ion batteries are considered hazardous material by the U.S. Department of Transportation because especially worn-down batteries could catch fire. That designation imposes special protocols: Trains and planes can’t haul them, and truck drivers have to go through special training to handle them. That makes it more expensive to move old EV batteries from the field to a central recycling location.
KULR Technology Group helps shipping companies get around these limitations while remaining in compliance with the law. The startup earned a special permit last year from the Department of Transportation for its lightweight, fireproof carrying case. KULR designed the liquid-cooled carbon-fiber packaging for NASA, so astronauts could store their lithium-ion laptop batteries without worry of a fire in outer space.
Now it’s available for use with terrestrial batteries of up to 2.1 kilowatt-hours. That’s a minuscule fraction of an electric vehicle battery, but useful for batteries used in consumer electronics and micromobility devices like scooters and e-bikes.
“It’s kind of like a Domino’s Pizza case, but instead of keeping [the batteries] warm, it’s keeping them cold,” CEO Michael Mo said.
The company already helps battery manufacturers and recyclers like Retriev safeguard shipping for end-of-life units. The fireproof casing lowers the cost of transportation, both because it avoids the need for specialized training and because it’s more effective than status-quo shipping methods. Currently, spent batteries are shipped in a UL-certified cardboard box with fire retardant and thermal insulation, a legacy product designed for earlier generations of battery tech, Mo explained.
“It doesn’t matter how fire-retardant the cardboard is — it’s not going to cut it” in a lithium-ion fire, he said.
KULR is working to increase the capacity its envelopes can handle. If it can get certified for 10 kilowatt-hours, then it’s feasible to break down whole EV packs into modules that each fit in a fireproof case. For now, the company is chasing the massive volume of smaller battery packs that’s already circulating.