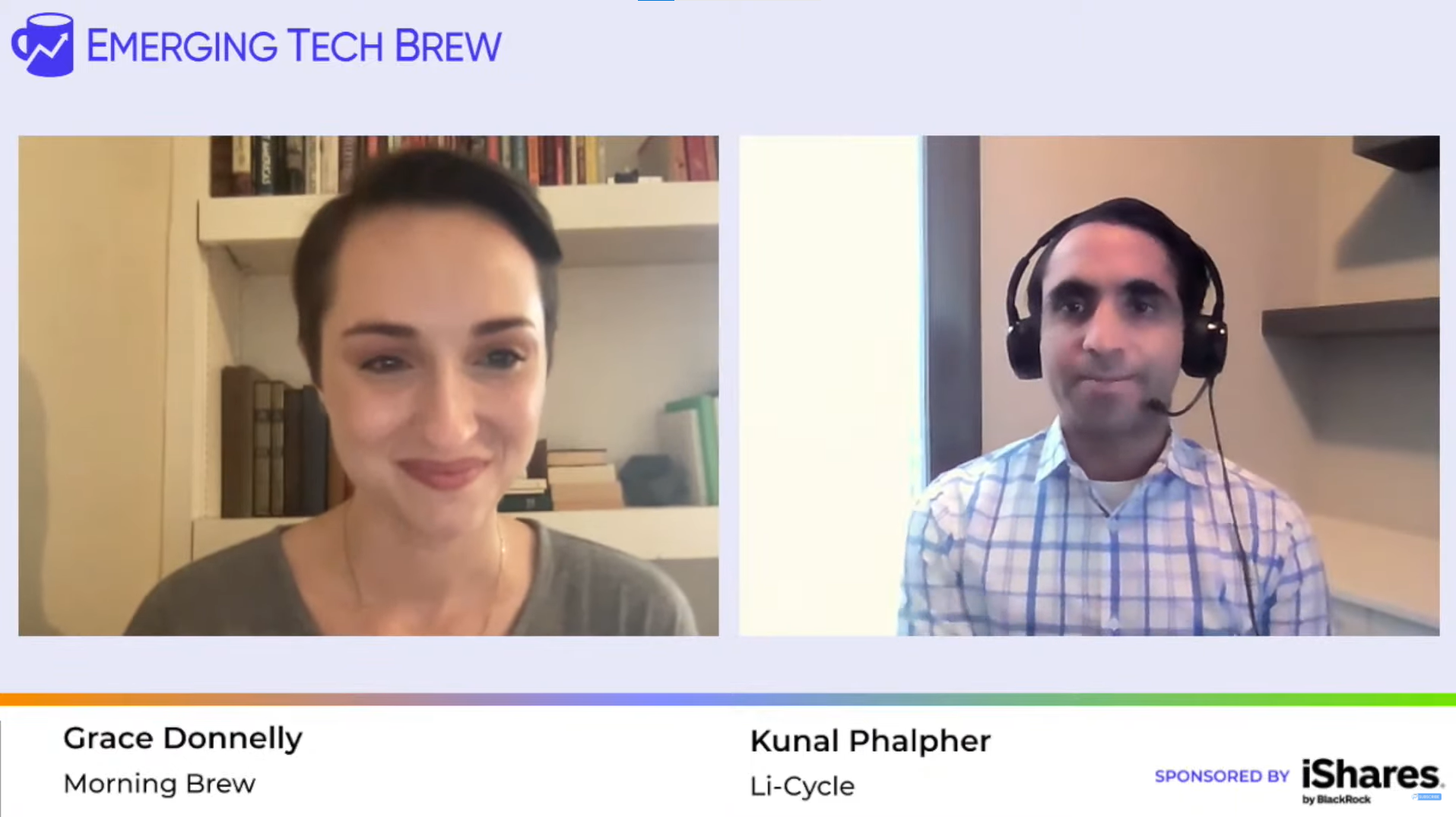
February 28, 2022
Event recap: What does EV battery recycling look like today?
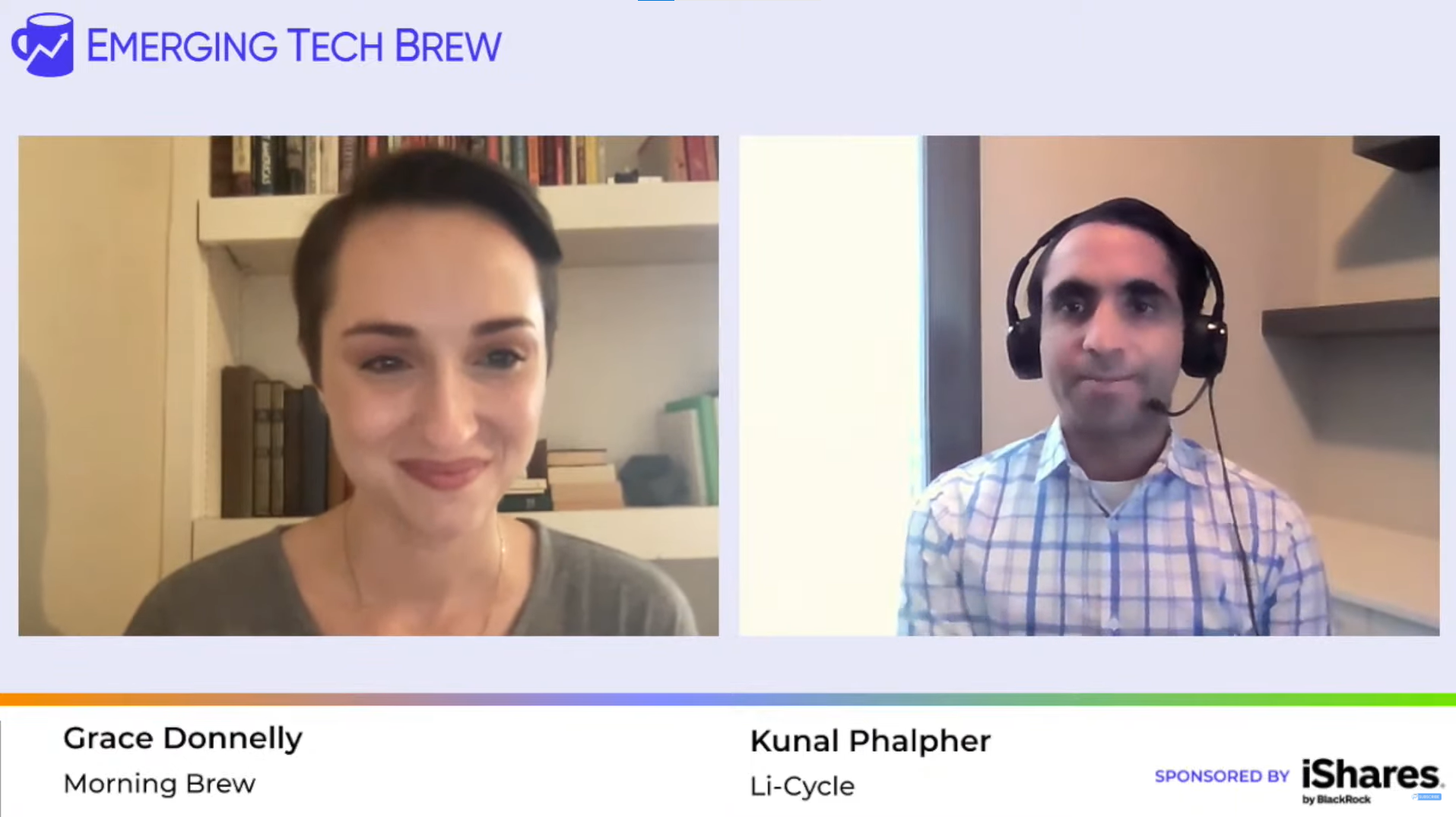
We talked to Kunal Phalpher, Chief Strategy Officer of battery recycler Li-Cycle.
February 25, 2022
Original article published in Emerging Tech Brew
There are few technologies more important to our collective future than batteries, and no, we don’t mean the Energizer Bunny-endorsed kind. Without scaled-up battery manufacturing, a transition to an electrified, renewable-based economy will be next to impossible.
As battery production goes into overdrive and more electric vehicles hit the road, a big question will become more and more pressing: How do we reuse and recycle EV batteries?
Yesterday, Emerging Tech Brew’s Grace Donnelly hosted a virtual event with Kunal Phalpher, chief strategy officer of Li-Cycle, a publicly traded battery-recycling company, to answer that question.
- Li-Cycle was founded in Canada in 2016. It SPAC’d in August, is currently valued at ~$1.1 billion, and has commercial partnerships with LG Chem and LG Energy, as well as with Ultium, a joint-venture between General Motors and LG Energy.
You can watch the full replay below, or read on for a written recap.
Getting the goods
For newer, still-under-warranty EVs, Phalpher said the recycling process can be pretty straightforward: If your EV’s battery is on the fritz, and your car is under warranty, automakers will replace your battery with a new one and recover the defunct battery. Once they do this, they typically hand the battery off to a recycling partner—e.g. Li-Cycle, or Redwood Materials, which has a partnership with Ford—for processing, or re-use the batteries when possible.
But, but, but…Things will become much more complicated in the future, once more EV warranties expire.
- “The big question that remains is what happens after warranty, when cars are eight or 10 years old?” Phalpher said. “Are they going to go through that traditional scrapping route, or are automotive companies going to continue to take an active role in reclaiming the batteries—since there’s so many valuable, critical materials in the battery—and keep it in their supply chains?”
Phalpher said that recycling waste from battery-production centers is a key market for Li-Cycle over the next three to five years, as they wait for EV adoption to scale up.
“As you produce battery cells, you definitely have material that comes out of the process that can’t be put into a battery—there’s just scrap material, out-of-specification material, lower-quality material, but it still contains a lot of valuable nickel, cobalt, and lithium,” he said. “And so, the best use case for that material, which can be thousands of tons from one of these sites, is how do you bring those materials and metals back into the supply chain—and that’s where the recycling piece comes in.”
Trash → treasure
To process batteries, Li-Cycle uses what it calls a “spoke and hub” process. A spoke is where used batteries are broken down and separated into different “material streams,” Phalpher said, and a hub is where some of that material—called “black mass”—is refined into battery-grade lithium, cobalt, and nickel.
- Phalpher said spokes are “decentralized,” and placed close to where used batteries could come from (e.g., areas with high EV penetration or close to battery manufacturers), while hubs will be in more centralized locations.
The thinking behind the model: Localized spokes can minimize the time (and cost) spent transporting heavy, potentially volatile old batteries, Phalpher said, while refinement is a process that benefits from economies of scale.
- Li-Cycle currently has spoke facilities in Kingston, Ontario and Rochester, NY and is building out facilities in Phoenix, AZ, Tuscaloosa, Alabama, and Warren, Ohio. It’s also developing sites in Norway and Germany.
- It’s building out its first hub facility in Rochester, and the company expects to begin delivering materials from it in 2023.
Through this process, Li-Cycle claims it’s able to recover ~95% of the lithium, nickel, and cobalt from the used battery. It also creates other, tertiary products, like plastic, copper, aluminum, graphite, and manganese. A recent peer-reviewed study found that lithium-ion batteries made with recycled materials are comparable to those created with newly-mined material.
Looking ahead…
Ultimately, Phalpher said the goal is to help automakers establish a more localized battery supply chain. The current battery-manufacturing process can be hyper-complex and can easily span four or five continents—from sourcing and refining materials to actually assembling the batteries.
Li-Cycle is aiming to build 100,000 tons of annual shredding capacity across its spoke sites by 2025, Phalpher said, enough to build batteries for ~200,000 EVs. Right now, its capacity is approaching 55,000 tons. He said building capacity by the end of the decade is crucial because that’s when a lot more EVs will reach the end of their lives in Europe and in North America—and demand for recycling should boom.