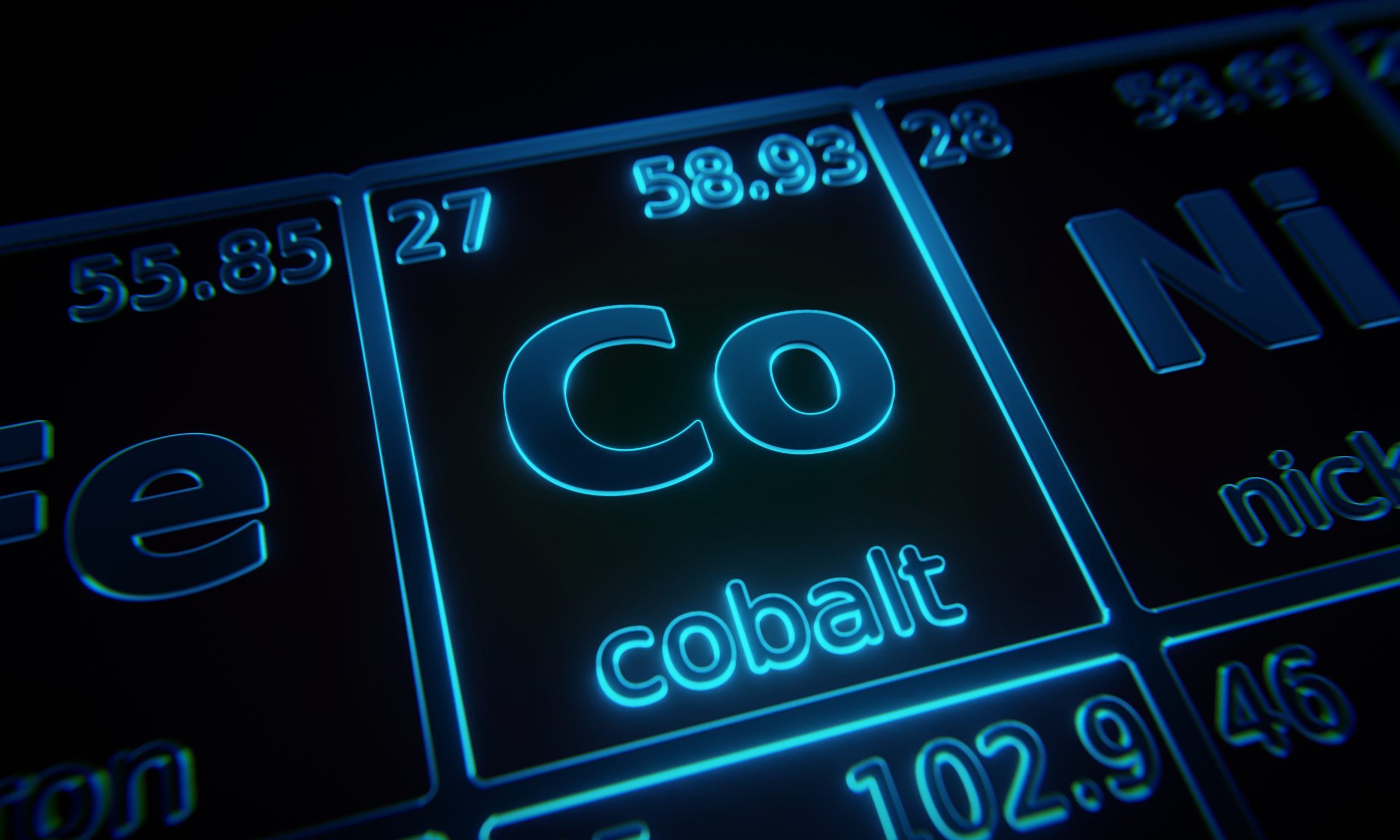
April 3, 2018
Cobalt: the DRC and the Role of Lithium-ion Battery Recycling
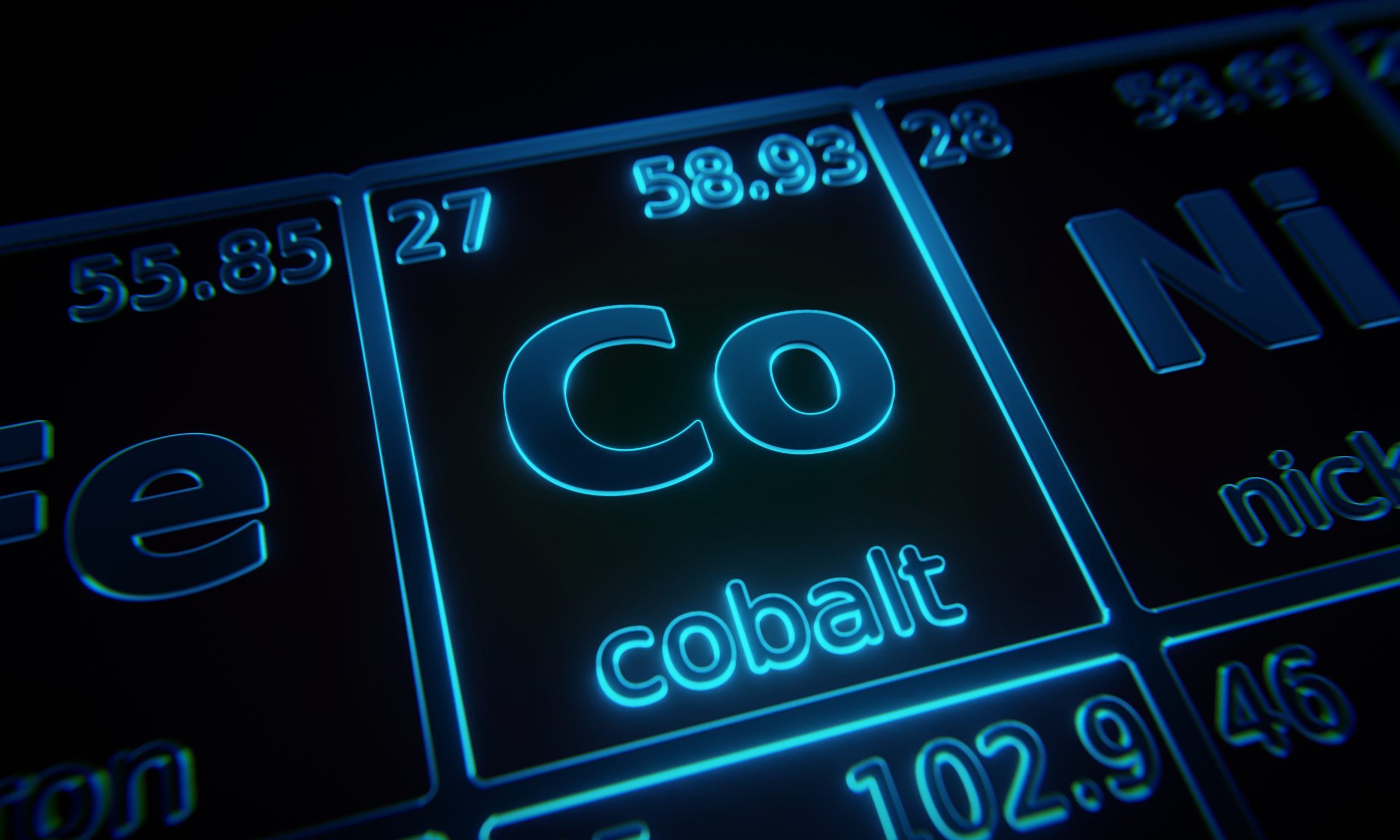
A labourer climbs through a cobalt and copper mine in Kawama, Congo (Source: Washington Post)
As lithium-ion batteries electrify our world through the proliferation of electric vehicles, grid-scale energy storage, and consumer electronics, the demand for critical materials continues to burgeon. Critical materials include cobalt, lithium, graphite, and more, each having their own unique supply chain dynamics.
Cobalt is a critical component in lithium-ion battery cathodes for high energy and power applications. The Democratic Republic of the Congo (DRC) accounts for almost two-thirds of global cobalt supply. However, some of the artisanal stream of cobalt production in the DRC has unfortunately been documented to involve child labour. Additionally, 98% of cobalt is mined as a by-product of copper and nickel, and hence cobalt supply has historically been relatively inelastic.
In order to mitigate risks and ensure high standards of social responsibility, manufacturers are actively looking to ensure providence associated with DRC-sourced cobalt supply, while some are looking to diversify away from the region. Alongside, the recycling of cobalt and other critical materials from lithium-ion batteries could play an integral role in minimizing bottlenecks and price swings into the future.
Mining: the starting point of the cobalt supply chain
In 2016, an Amnesty International investigation exposed how lithium-ion batteries could be linked to child labour in the DRC. The country has had a long history of foreign exploitation of its natural resources and is now a hot spot for foreign companies to extract high-value and abundant minerals. The Congo is responsible for more than 60% of global cobalt supplies. Approximately 20% of their cobalt exports reportedly originate from artisanal mines, the majority of which are unregulated and sometimes illegally operated.
Artisanal miners are typically impoverished workers working in harsh conditions without the help of mechanized equipment. With no idea of their enormous role in the global cobalt supply chain, these workers spend day and night mining by hand, with the constant risk of possible cave-ins, with little oversight and few safety measures. In order to secure only $2-3 a day, it is common to see artisanal miners digging along roads, railroad tracks, through the dirt floors of their own homes, and even by dangerously trespassing into privately owned land of mining companies.
Child labour and its unfortunate role in the cobalt supply chain has been an acute concern across industry. In 2012, UNICEF estimated that 40,000 children were taking part in the DRC’s mining industry. However, this devastating problem has only been aggravated by another socio-economic issue in the DRC: the lack of schools and government resources to establish them. “We have a big challenge with these children, because it is difficult to take them out of the mines where there are no school for these children to go to,” said Richard Muyej Mangez, a high-ranking government official in Kolwezi, as part of an interview with the Washington Post in 2016. Due to minimal resources and without a proper system to take these children out of dangerous working conditions, the local government has been hard pressed to find a solution.
From the DRC’s mines to the latest products
So how exactly does cobalt from the DRC’s mines and other sources move into the rest of the world’s consumer electronics? Companies such as Zhejiang Huayou Cobalt are responsible for a significant level of cobalt processing and production. Huayou Cobalt produces cathodic precursors (e.g. high purity cobalt sulphate heptahydrate) to supply to cathode manufacturers, who in turn sell the cathodes to battery cell and pack manufacturers. Ultimately, electric vehicle and consumer electronic companies utilize these lithium-ion battery cells and packs in their end products.
Manufacturers have recently increased their efforts in supply chain due diligence and tracking. A recent report from Amnesty International, Time to Recharge, has ranked industry leaders such as Apple, Samsung, Microsoft, BMW and Tesla on how these companies have worked to improve unethical cobalt sourcing in the last several years. Nonetheless, there is still a significant amount of work to be done to protect human rights abuse and prevent child labour in areas like Kolwezi in the DRC.
Supply chain dynamics and the recycling of lithium-ion batteries
With the recent boom of cobalt demand due to its extensive use in smartphones, laptops and in the rapidly growing applications of electro-mobility, cobalt prices have recently risen to over $42.50 per lb. (over $93,700 per metric tonne) as of March 2018. Alongside, the DRC plans to double tax rates on cobalt as well, which could inhibit mining investment in the country.
By 2020, lithium-ion batteries are forecasted to account for 60% of annual global production of cobalt. As battery and vehicle manufacturers ramp up their operations globally, cobalt supply has had trouble rapidly responding to demand. Although there are a variety of companies exploring new primary mining sources of cobalt, it will likely take years to bring any new discovery into production. Manufacturers have sought long-term supplies of cobalt; however, the inelastic supply dynamics of cobalt have proven difficult to overcome.
Could the recycling of lithium-ion batteries mitigate the current and near-term cobalt supply challenges? In short, yes – by 2025, lithium-ion battery recycling could meet 20% of the forecasted global demand for cobalt. In turn, lithium-ion battery recycling will reduce the social and environmental impacts of artisanal mining in the DRC. Moreover, recycling can mitigate drastic price swings in cobalt and other critical materials, as well as the reliance on mining and refining into the future.
Li-Cycle Technology™ is uniquely positioned to enable the maximized recovery of cobalt and other critical materials through recycling lithium-ion batteries, due to its closed loop nature. Subsequently, recovered materials are re-integrated into the lithium-ion battery supply chain and the broader economy. In turn, Li-Cycle is enabling a completely transparent and ethical supply chain for 100% recycled cobalt and other critical materials.
The recycling of cobalt from lithium-ion batteries is playing an important role in supply chain diversification and will increasingly do so into the future.