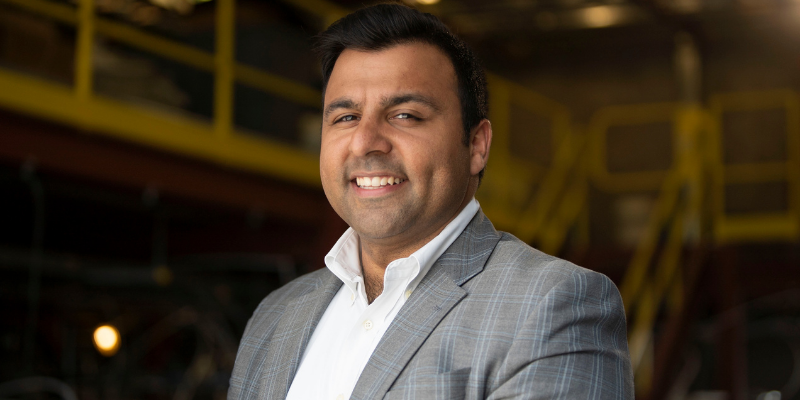
July 29, 2021
‘You cannot change the geology in a given country , but every country can have access to the above ground resource – the urban mine’
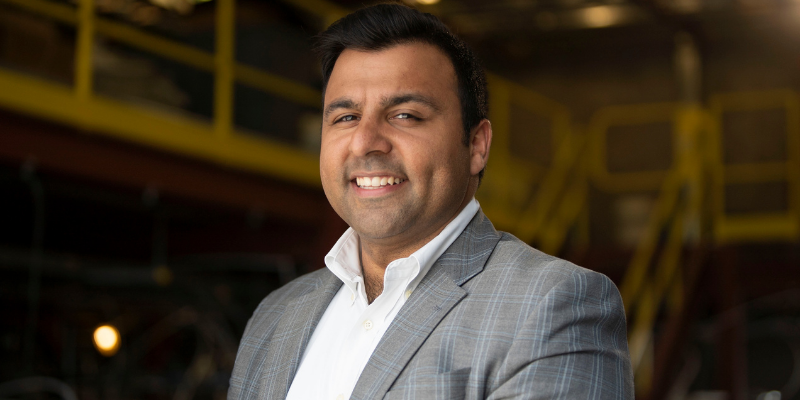
Benchmark spoke with Li-Cycle’s Ajay Kochhar, President, CEO, and Co-Founder, about the lithium ion recycling market, Li-Cycle’s plans for bringing recycling capacity to North America, the future of battery raw material supply
July 29, 2021
Original article published in Benchmark Minerals
Benchmark: To start with, can you give us an overview of Li-Cycle and your background in the industry and what led you to founding the company?
Ajay Kochhar: By way of background, Tim Johnston and I founded Li-Cycle over five years ago before lithium ion battery recycling was really the prevalent topic that it is today. We both come from the lithium industry and met while working at a firm called Hatch. For reference, Hatch is a global engineering, procurement and construction management company. While we were there, we worked extensively on projects to make lithium chemicals for cathode materials. Tim and I had the perfect blend of skillsets and expertise to start Li-Cycle – I brought the chemical engineering experience and he brought the mechanical engineering prowess.
We saw how the world is rapidly changing as it is swept by the electrification of the global economies. And we both found ourselves wondering, “What is going to happen to all these batteries?” Not only when they come to the end of their lives, but also the substantial amount of waste that is generated in battery manufacturing. That led us down a path of saying, “Okay, well what’s happening today? Where are those batteries going and how is the manufacturing waste being handled?”
Batteries had been being treated like waste, predominantly they entered legacy supply chain processes, which traditionally utilise extreme heat processes – burning off many of the critical components – and only some of the materials end up being recovered. This set-up simply did not make sense to us, and fixing it was really the impetus for us to start Li-Cycle in 2016.
We realised that there was a glaring hole in the future of this increasingly electrified global economy, which was the lack of an environmentally and economically sustainable lithium ion battery recycling solution. Both Tim and I knew the industry, we knew the challenges, but most importantly we knew we could develop a solution that would solve for the missing piece in a truly circular battery supply chain.
Benchmark: Looking at the industry more broadly, what’s the state of the lithium ion battery recycling industry today and how does it compare regionally?
AK: There are groups, which you could classify as pre-processors, that are handling batteries regionally. This happens in Europe, North America to some degree, Japan, Korea, and China. These pre-processor groups take in mixed battery streams which go into an intermediate product. They are essentially trying to isolate the cathode and anode material in the batteries. The cathode contains the critical, valuable components, which is why cathode recycling has been going on for a while.
During the second step, which we call post-processing, there have been some parties taking an intermediate product which has then entered the legacy nickel smelting infrastructure. The intermediate product then makes its way to companies that take all sorts of materials, including mined material, and go through a smelting and ultimately a refinery process.
There are many parties involved, and the state of play, globally, is really organised around these two routes. This may be the traditional “normal” for the lithium ion battery recycling industry, however, there is a desire for other solutions that are both more environmentally and economically sustainable, while rooted in the circular economy.
There are two main issues affecting legacy supply chains recycling lithium ion batteries. One issue is that batteries are not just scrap metal – they have risk. The other issue is we need burgeoning quantities of lithium, nickel, and cobalt to go into new batteries.
Benchmark: Could you talk us through Li-Cycle’s recycling process and technology? Which materials are you producing?
AK: When we set out, we understood the broad development of the industry and the variability in chemistries. Lithium ion is of course a universe with a number of different products. Historically in the lithium ion recycling space it was very clear that existing companies were mainly looking to recycle cobalt – with cobalt in small format devices tending to have higher content.
However, we at Li-Cycle take a different approach. Our focus and foundation as it pertains to recycling has always been to take any chemistry and any form factor as long as it is lithium ion. From the smallest constituent material all the way up to a large pack level and at any state of charge. Another issue is that with large packs there is a lot of residual energy, which can be both laborious and risky, from a safety perspective, to discharge and deal with.
Being able to process any form of lithium ion battery was in the fundamentals for how we wanted to root our process – and we are currently executing on that at our Spoke facilities. There is no sorting into specific lithium ion chemistries, and we do not dismantle heavily. If we recycle a large pack, we’re typically getting down to the module level at most. We are also now moving towards full pack processing – no dismantling. From a chemistry perspective, we are totally agnostic and we only operate a single line – we do not operate different lines for different chemistries – making it easily scalable.
We have innovated a new process and technology to deal with lithium ion batteries, without using extreme heat. Our operations are split into a two-stage process which we call our Spoke & Hub model, utilising our patented technology, which is efficient, profitable, and scalable. We follow a non-thermal process resulting in low-polluting air emissions, no wastewater, minimal solid waste, and everything goes back to the economy.
A network of facilities, called Spokes, take in end-of-life lithium batteries and battery scrap generated in battery manufacturing, transforming them into intermediate products. The Spokes are located close to a significant supply of batteries enabling us to get to scale very quickly. Ultimately the Spokes feed the intermediate materials to our Hubs, centralised facilities, where we convert them into battery grade materials.
To contextualise our process, I can describe it using an example. Li-Cycle will take end-of-life batteries from electric vehicles no longer active at a big name car dealership. The batteries are shipped to our nearest Spoke, which shreds the batteries, producing an intermediate product called “black mass”, a powder like substance that includes valuable metals such as lithium, nickel and cobalt. We then take the black mass to one of our Hubs, where we separate the metals contained within, in a submerged solution and extract them. Then, we sell the extracted battery grade materials to Traxys, the largest independent nickel and cobalt offtake and trading firm. From there the battery grade materials will find their way to a battery manufacturing facility who uses them to build new electric vehicle batteries.
We have two Spokes today, one in Kingston, Ontario and a second in Rochester, New York. We are planning to establish 20 Spokes around the world over the next five years. Each Hub serves a network of Spokes and has the capacity to process output products from 12 Spokes.
At the Hub, which is in development in Rochester, NY, we’ll use a hydrometallurgical process, taking the black mass, and recovering graphite in a concentrate form, battery lithium carbonate, battery grade cobalt sulphate, battery grade nickel sulphate, manganese, and other valuable products.
Processing at our Hubs will allow us to achieve economies of scale, while simultaneously condensing the recycling supply chain into one. This removes the need for many different parties and brokers – some pre-processing and some post-processing – and a very elongated process, which is not fit for purpose.
Benchmark: How energy intensive are your operations? How do you factor in ESG and safety factors?
AK: For every tonne of batteries we recycle, we offset or reduce approximately five tonnes of carbon dioxide or greenhouse equivalents from the atmosphere. So how does that work? Well, in the mining refining chain we make eight different products from the Hub. Usually that would represent many separate supply chains, each of them with their own emissions profile. However, through our recycling process we consolidate all of those supply chains, reducing the overall footprint of each of those primary sources.
And as an offset figure, for example, for every tonne of batteries we recycle, we save 96 tonnes of water from being used in primary mining and refining applications. More broadly, approximately 50% of the overall carbon footprint of an electric vehicle is usually in the battery pack. There is a big push to cut that figure down. We can reduce the batteries footprint by 74%.
Another ESG factor to consider is the safety aspect of battery recycling, which is not discussed as much as it should be – but is an important aspect of battery recycling we have effectively tackled. We are ISO certified. That may sound mundane, but this is the first area of focus to figure out when you start scaling – particularly the management of safety around storage and transport of lithium ion batteries. It starts with the customer, making sure batteries are transported to us in the correct way, with the right packaging, and right methodology – all the way through to storage. We follow our own storage practices. In a lot of these areas the regulatory landscape is not clear, so we have had to figure out what the best practices are and lead. With the recycling process, safety is managed through the way we mechanically process at the Spoke. Our process deprives the system of oxygen, through submerged shredding, which prevents the risk of fire.
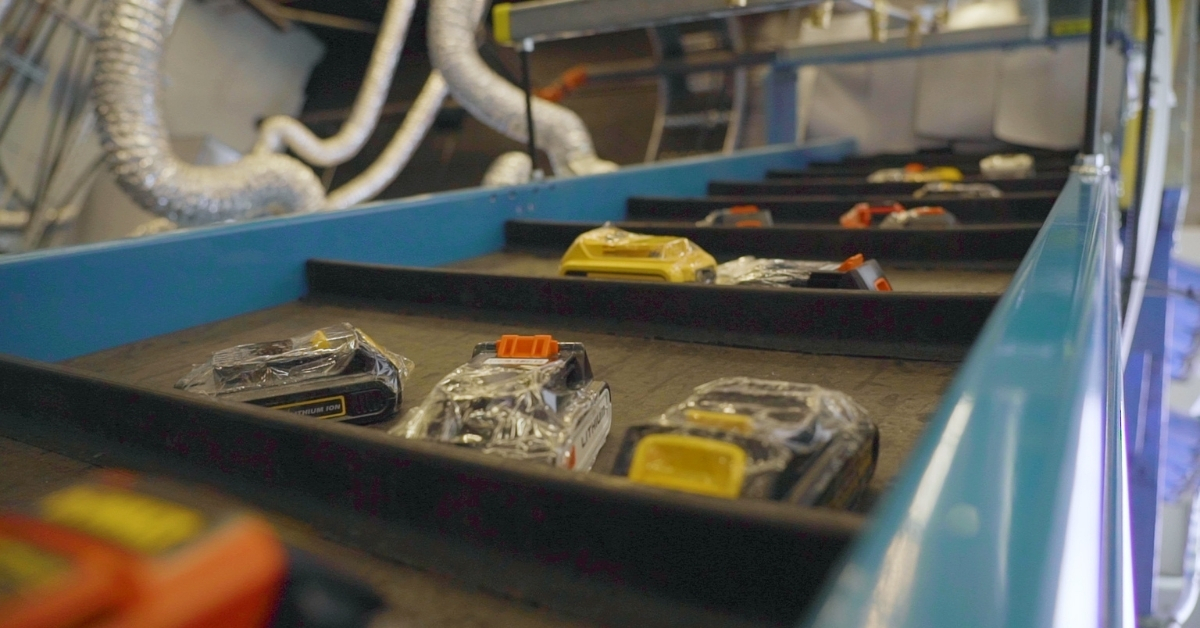
Benchmark: Please talk us through where you are with offtake agreements and partnerships today and what you plan for the future?
AK: There are two parts to this, there’s the way in and the way out. On the way in, we have batteries and essentially battery materials. On the way out, we have nickel, cobalt, lithium chemicals, and other materials going back into the supply chain.
It may have taken us five years in order to prove we are able to qualify for the highest of standards when it comes to battery recycling, however, we now work with the largest automotive companies and battery manufacturers in the world.
Today we have 40 plus battery supply customers. If I were to describe the mix today, approximately 20% comes from battery aggregators and consolidators – smart phone batteries, laptop batteries, scooter batteries, you can name it.
Around 50 to 60% of our supply today comes from manufacturing scrap. A big misnomer when we started the business was that battery recycling was 10 years away and that it was not a problem for today. But we knew that was not the case and the underlying reason for that – or at least a major part of that – is because of manufacturing scrap.
Benchmark’s megafactory tracker now has over 200 megafactories in the pipeline. I think we all remember that not long ago that figure was only just over 10 in the pipeline. The pipeline has grown exponentially and will continue to do so to meet demand. Every one of these megafactories – and those in the pipeline – generates a level of production waste of typically 5%-10% on a conservative basis, in reality it’s probably much higher. When you begin to add that up across 200 plus facilities over time, that’s a huge driver for the recycling market, before you even have end-of-life material. That is how our supply chain is changing.
In the future, the second phase of battery recycling, is the conceptualised end-of-life tsunami of batteries. We already have an offtake agreement with Traxys, which is the largest independent nickel and cobalt trader in the world.
They have been a key partner for us. We have eight products out of our Hub and from a de-risking standpoint we know the lithium, nickel, and cobalt markets, however, we are lithium ion battery recyclers not traders. So, we wanted to partner with a group that could bring both the acumen and be the offtake partner, all while allowing us to retain our flexibility through a collaborative partnership. It has taken us time to qualify the way in, go through our development, bring the customers along, make the product and battery grade materials, and qualify the product. And now we are on track to ramping up commercialisation.
Benchmark: Looking at your North American footprint, you recently announced you will be building a new facility in Arizona. Can you talk us through North America, in particular, and your plans to expand into other regions?
AK: Our high-level global plan for the next five years is to establish 20 Spokes and four Hubs.
Today, we have two existing commercial operating Spokes and a larger Hub in Rochester, NY in development.
Our Rochester Hub is being built at the Eastman Business Park – which is the former Kodak Business Park – so it’s a great place for us in terms of chemical infrastructure, labour, and support from the state. We undertook a rigorous site selection some years ago and are now fully in execution mode. There are over 45 people on the team working on the Rochester Hub. The overall plan is to break ground by the end of 2021 and, by early 2023, have the plant fully operational.
In North America we announced our third Spoke, which will be in Arizona. We chose Arizona because it is close to our existing customer network but also at the nexus of where a significant supply of batteries is available for recycling. The intent is for that to be up and running by early 2022.
From a global perspective, we are expanding in three ways. For the incremental 17 Spokes and three Hubs, excluding North America, we have a three-pronged strategy. The first prong is regional partnerships. The market differs greatly region by region, as there are a variety of different aspects of regulatory drivers in the supply chain. Our first approach is to partner with groups that have batteries available for recycling and add value in terms of speed. If they have existing facilities and we bring the technology, the know-how, and the ability to combine these together we will deliver great value.
The second prong is that the customers we serve in North America, or even globally, are consistently asking us to set up in other regions. Finally, the overall market is highly regional. Within Europe and other regions there are some parties that have been operating for a while, that have permits, people, and potentially supply, but they do not have the technology that is required for this new wave and the shift in our space. Therefore, there are some judicious cases of buy-side M&A that we will look at on an opportunistic basis.
Benchmark: How can battery recycling support President Biden’s plans to “win the electric vehicle market”? What would you suggest to politicians to support the build out of those supply chains?
AK: There used to be a time when there wasn’t any sense of urgency as it pertains to the adoption of battery recycling. Now it’s clear that is no longer the case, and the supply chain needs to be set up not just in the USA but in every jurisdiction, globally.
The first point is that supply chain investment needs to be increased end-to-end. It cannot simply be that you invest in battery cell making – that isn’t going to cut it. If you are going to invest in cell production, you also need to invest in the cathode production and even in other upstream segments of the supply chain to support battery capacity. We see the need for this reflected in much of the dialogue on the battery supply chain, and it’s an important point to remember.
Secondly, as we look forward, a major bottleneck in the battery supply chain will be for critical materials such as lithium, nickel, and cobalt. You cannot change the geology in a given country, but every country can have access to the above ground resource – the urban mine. I think we’re now at an inflection point. A couple of years ago there wasn’t necessarily the desire to use above-ground reserves. But as we reach this inflection point in electrification we will need as much of these battery materials as we can get, sourced in a clean, transparent, low-carbon footprint way. This is a key opportunity for any country.
For the U.S. specifically, our Hub in Rochester will be the largest domestic source of cobalt in the USA and one of the top two for both lithium and nickel. My point is, we will need both primary and secondary material sources, and as the USA’s plan unfolds and investment is targeted, it needs a focus across the supply chain.
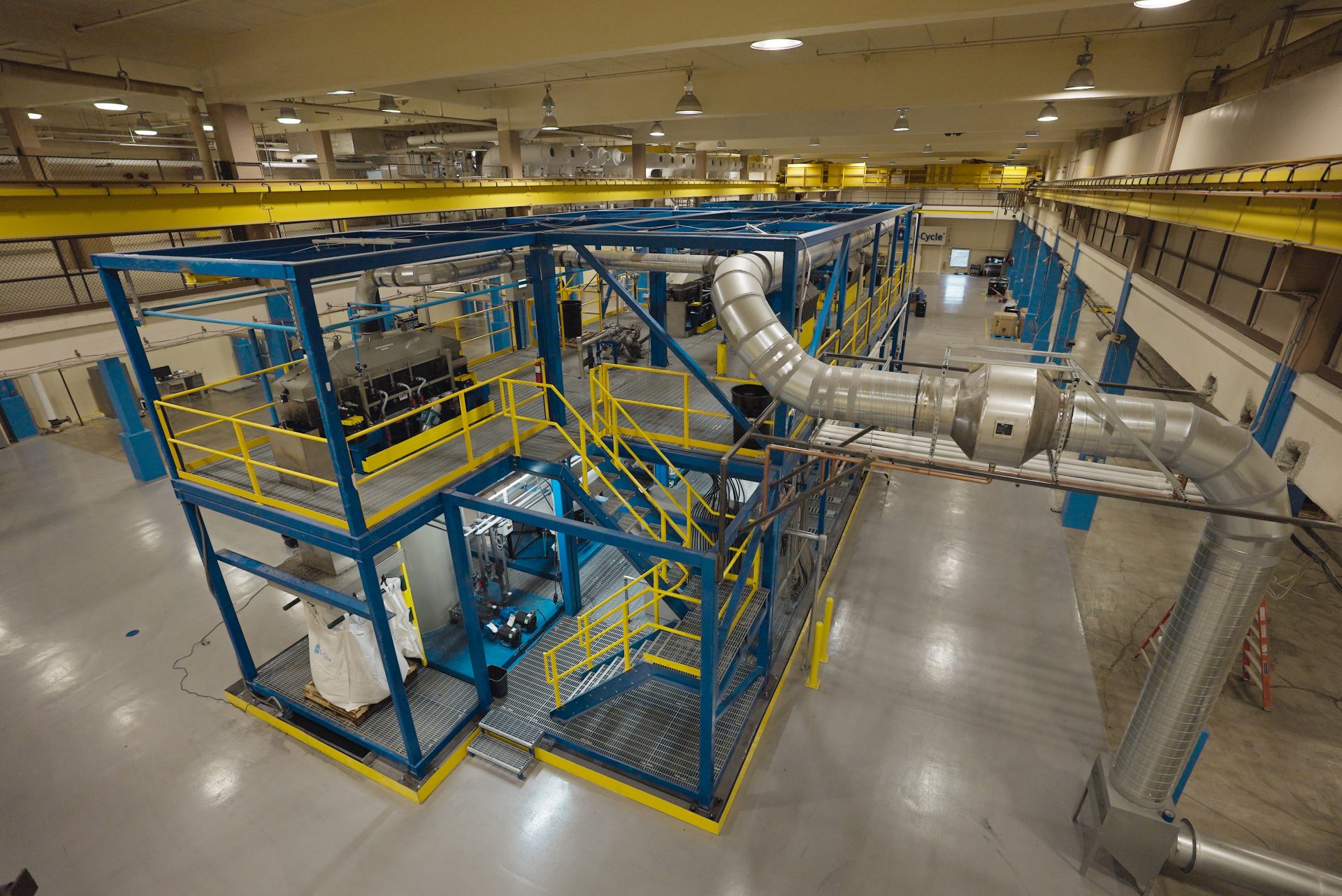
Benchmark: How large a role can recycling play in supplying raw materials to the battery supply chain?
AK: Let’s split this into today, medium term, and long term. Today, lithium production from recycled sources is close to nil. For nickel and cobalt, broadly speaking, those markets have a few single digit percentages recycled from alloys and other sources.
In the medium term, we all know about the extreme demand that is going to be out there for these materials, and recycling will ease pressure across the supply chain. For lithium, nickel, and cobalt, in the next 10 years recycling could supply 10% to 20% of the demand from the lithium ion battery sector. That may not sound like much initially, but to increase from close to nothing, to 10% to 20% of those markets is huge.
We are going to reach a point where the market will take all the material it can get. In the longer term, 20 to 30 years in the future, recycling could account for 50%, and up to 70% or more potentially, of the supply for lithium, nickel, and cobalt.
The big question is what does that mean for mining? We are not at a point where we know the answer to that yet. In the interim and for the foreseeable future, mining will be the main source of supply and recycling will be a critical secondary source to help minimise bottlenecks around the supply chain.