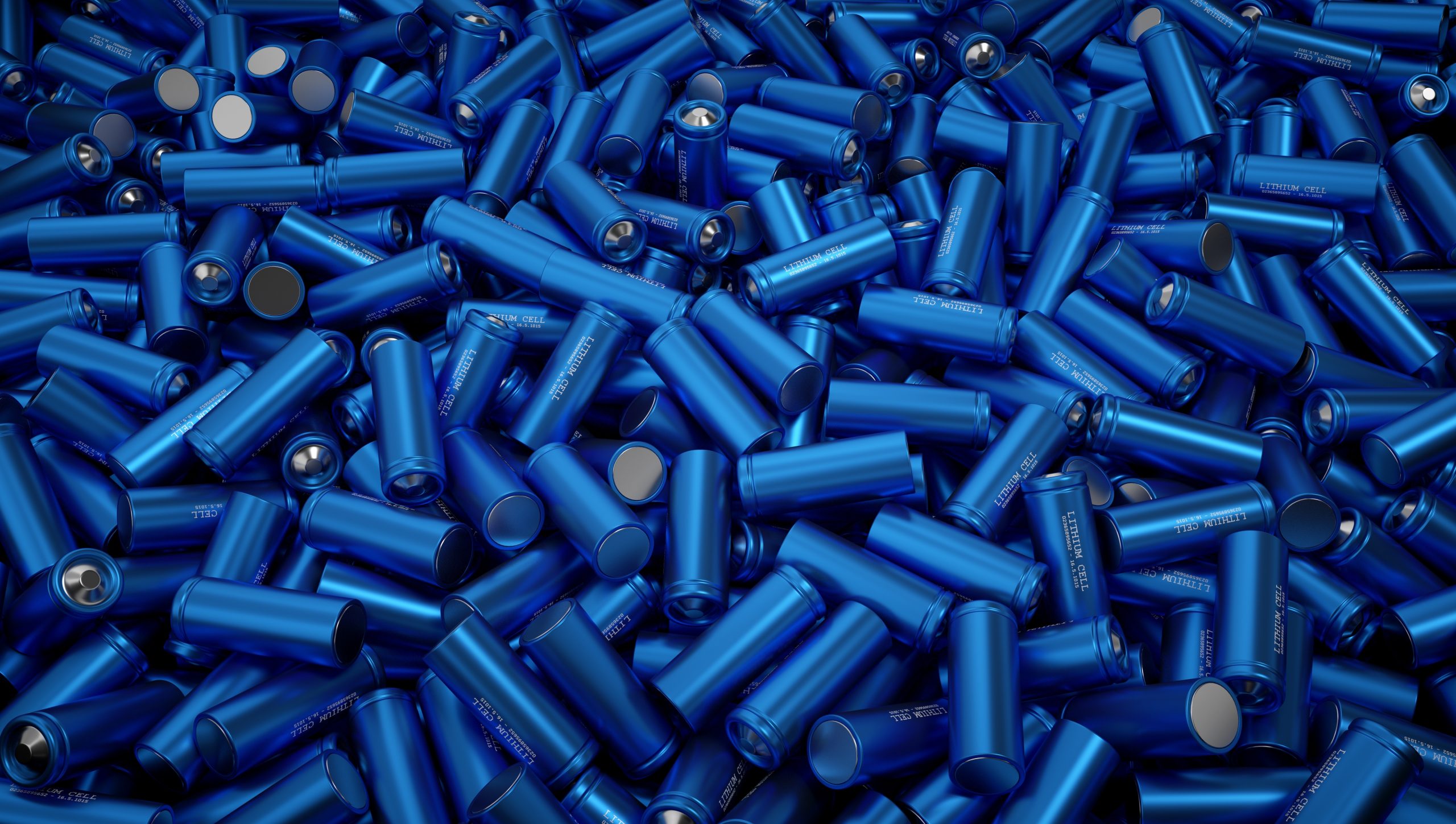
November 27, 2018
The Future of Lithium-ion Batteries and Resource Recovery
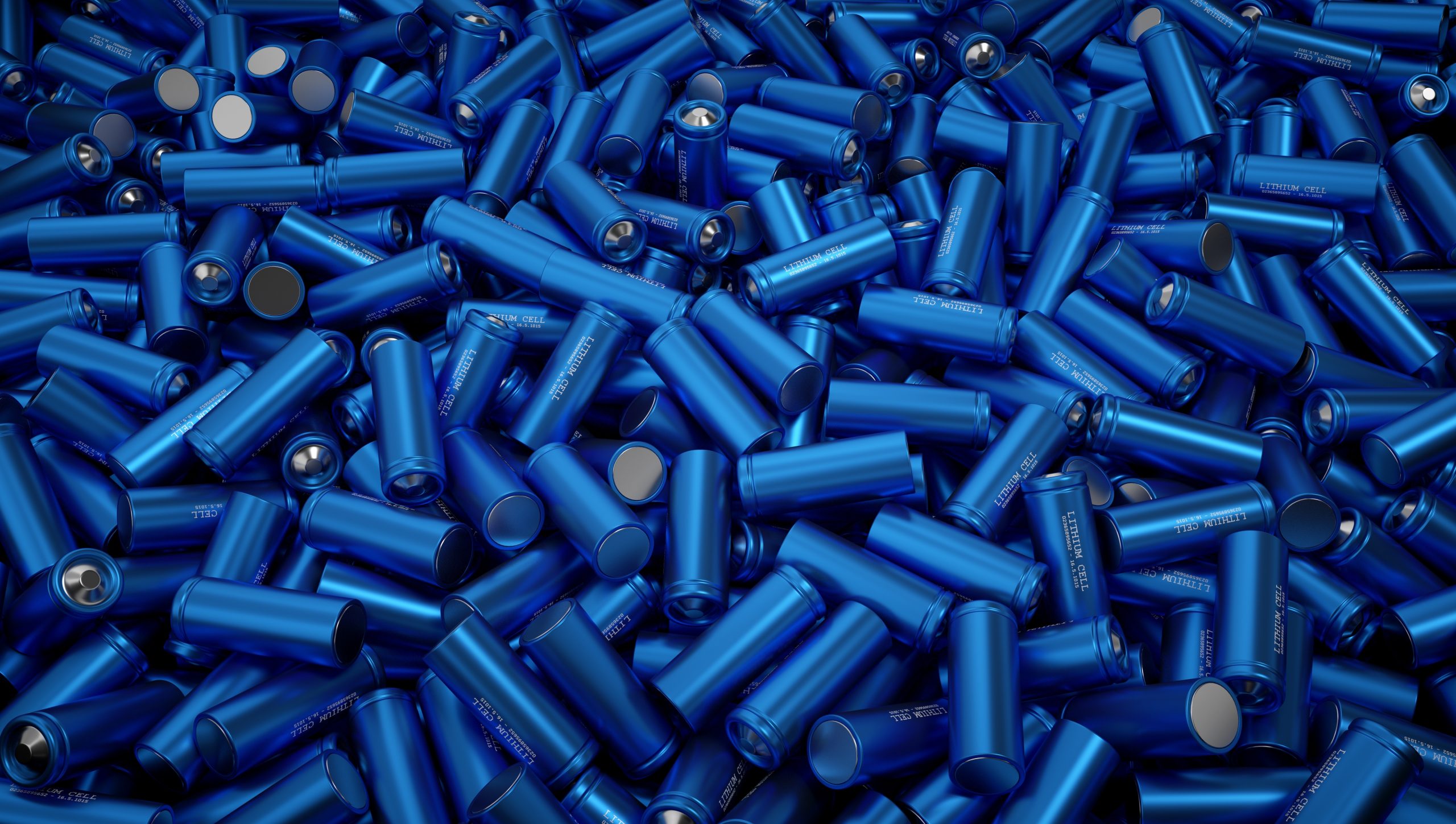
Despite the constant news flow regarding new battery innovations, energy storage technology advancements typically require long development lead times from concept to full-scale/commercial manufacturing. MIT’s Technology Review highlighted this in an article in 2017, documenting the challenges faced by many clean energy start-ups and growth-stage companies. In the article, Ilan Gur, a co-founder of a battery company that was acquired by Bosch, states “don’t hold your breath for the things that come after lithium-ion. We’re much more likely to ride the lithium-ion cost curve for another few decades.” There are two key drivers for the likely long market life of lithium-ion technology: cost and performance.
The price of lithium-ion battery packs have dropped below $209/kilowatt-hour according to a Bloomberg New Energy Finance survey, and some estimates put them as low as $190/kilowatt-hour, with the cost expected to continue falling to below $100/kilowatt-hour by 2025. By comparison, existing competitive alternative energy storage technologies typically have not fallen below the $200/kilowatt-hour level. Emerging technologies that have improved cost and performance require substantial investments to support R&D and to progress to the economies of scale that lithium-ion batteries continue to benefit from.
Nonetheless, lithium-ion batteries have significant room for improvement. As a result, there are a substantial number of evolutionary and revolutionary advancements to lithium-ion battery technology under development. Alongside, a cradle-to-cradle approach is required to assess the value chain opportunities and challenges that emerge as evolutionary and revolutionary changes progress.
Evolutionary Advancements
Active material advancements are a key focus of the evolutionary shifts in lithium-ion battery technology. For example, the evolutionary advancements in cathodic materials are focused on tailoring lithium-ion batteries for a broad range of applications, while optimizing for key performance indicators such as cost, cycle life, energy density and safety.
The lithium nickel manganese cobalt oxide (NMC) cathode chemistry family was initially commercialized with a 111 composition – 1 part nickel, 1 part manganese, and 1 part cobalt. Since the inception of NMC technology, the reduction of cobalt content has been a key research and development focus, with a focus on reducing cost and reliance on the cobalt supply chain, including cobalt’s Democratic Republic of the Congo (DRC) centricity and resulting ethical concerns (for more information, please refer to Li-Cycle’s blog post regarding the cobalt supply chain). As a result, NMC cathode technology has gradually progressed to new stoichiometries/mixes, including 422, 622, and recently, 811 compositions. While commercial use of the NMC 811 cell is not likely to occur for at least 2-5+ years, developers have driven key enhancements through research and development to date, including improvements in cycle life, better capacity retention over the battery lifecycle, and lower production costs.
As evident in the chart below, the NMC cathode chemistry family continues to experience consistent growth, even as key entities such as Tesla have prioritized the lithium nickel cobalt aluminum oxide (NCA) chemistry in their electric vehicle product segment.
Revolutionary Advancements
Moreover, in 2017, UK-based Dyson announced that it would be investing USD $2.7 billion to bring an electric vehicle with a solid-state battery to market by 2020. However, this timeline has recently been brought into question after a new report indicated Dyson’s first generation of electric vehicles may not feature this technology. Nonetheless, various global startup and growth-stage companies globally are pushing ahead to address the challenges with solid-state lithium-ion battery scale-up, including Massachusetts-based Ionic Materials and Colorado-based Solid Power.
Advancing Resource Recovery/Recycling Technology and Li-Cycle™
Li-Cycle is on a mission to solve the global lithium-ion battery recycling challenge and meet the rapidly growing demand for critical battery materials. The company seeks to ensure that electric vehicles and lithium-ion batteries have a truly positive environmental impact over their entire life cycle. In turn, Li-Cycle aims to enable the momentum behind the global transition to electro-mobility and reduce greenhouse gas emissions on a global scale.
As lithium-ion battery technology continues to undergo evolutionary and revolutionary changes to further advance the capabilities of the batteries that power our world, Li-Cycle is strategically positioned to provide an end-of-lifecycle recycling solution to all types of lithium-based batteries. In doing so, Li-Cycle aims to create a true closed-loop system, enabling low cost, environmentally sustainable recycling processes and industry-leading safety standards to support the battery industry as it continues to drive global electrification.