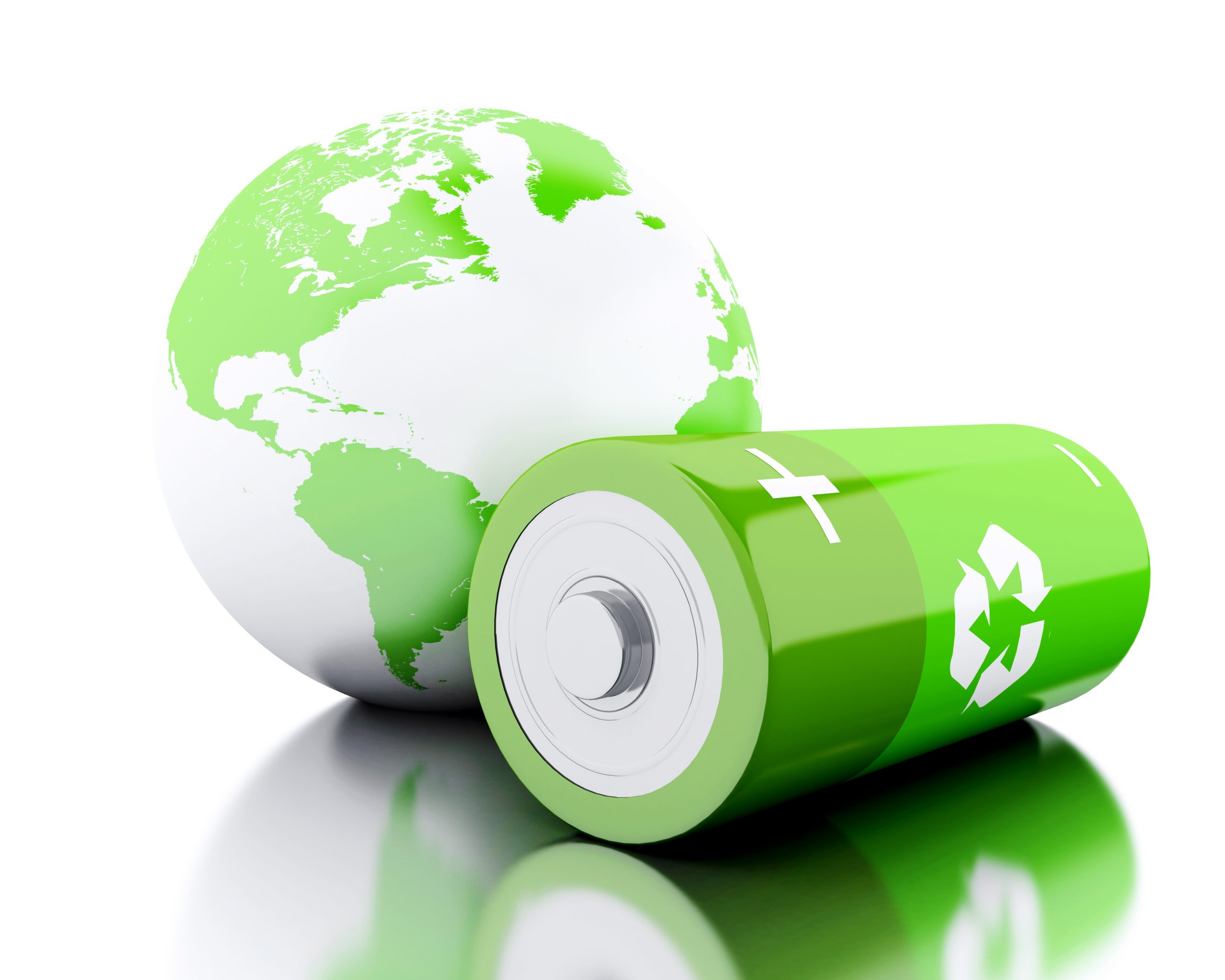
June 27, 2021
Li-Cycle: Hydrometallurgical Recycling of Lithium-Ion Batteries
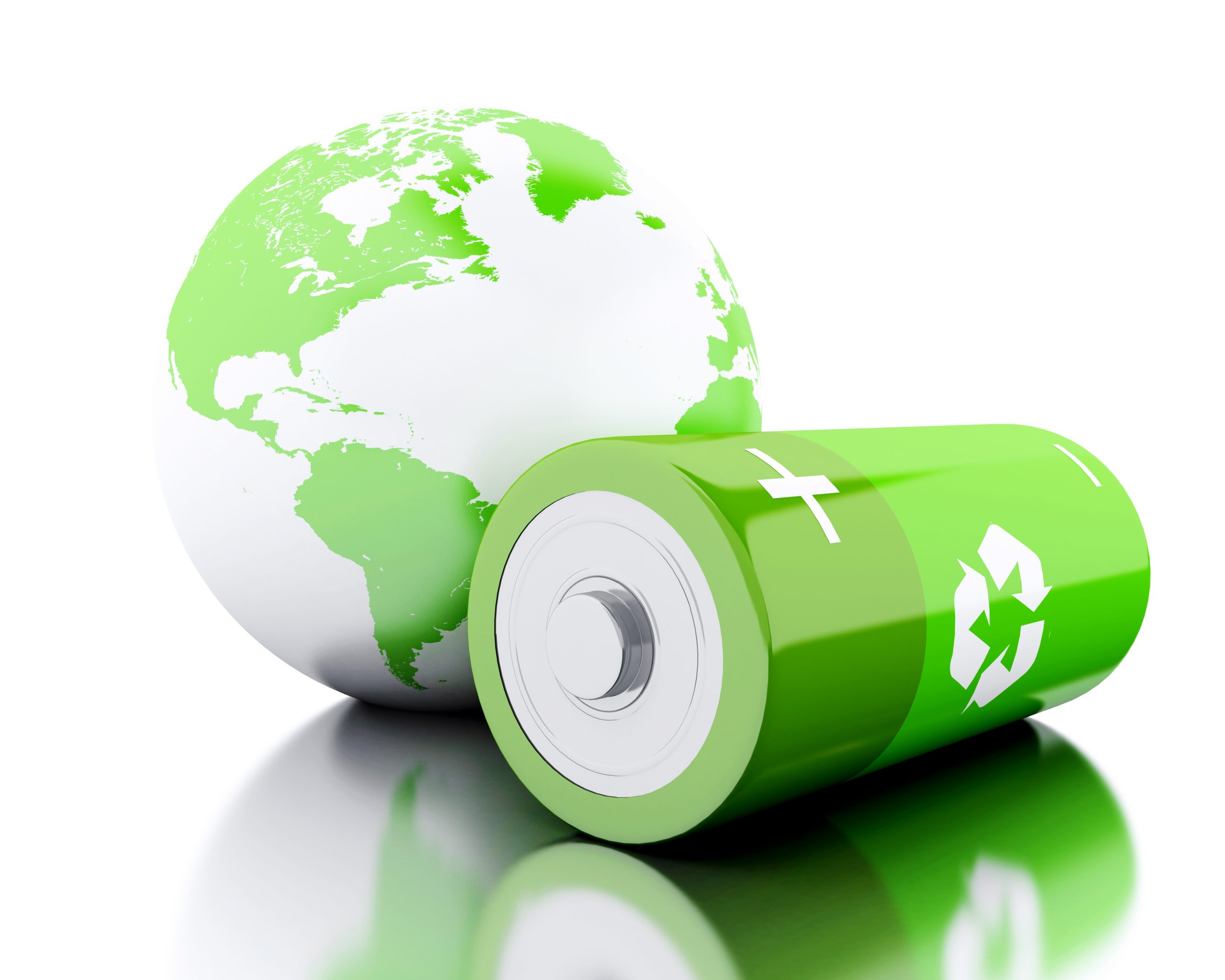
June 24, 2021
Original article published in AZoCleantech
Li-Cycle, an Ontario, Canada-based battery recycling company, is working to link lithium-ion batteries into the circular economy by making them a more sustainable product. Using hydrometallurgical recycling, Li-Cycle hopes to solve the global battery recycling problem which sees tons of materials and energy wasted each year.
Hydrometallurgical Recycling and Battery Recycling Solutions
Li-Cycle’s method involves two distinct, proprietary processes – collected into so-called “Spoke” and “Hub” technologies. The company’s Spoke operations entail mechanical safe size reduction of incoming used batteries. Hub operations involve hydrometallurgical recycling and resource recovery methods which have been designed specifically for recycling lithium-ion batteries.
Mechanical Safe Size Reduction: Spoke Operations
The Spoke element of Li-Cycle’s battery recycling solutions business can handle any type of lithium-ion battery. Batteries coming into these facilities undergo a mechanical safe size reduction process which makes them safe for further processing.
Incoming batteries are converted from a charged state to inert objects safely and efficiently. The process is totally sustainable and results in no solid or liquid waste being produced at the facility.
The large-scale industrial facilities can receive lithium-ion batteries in any size, format, chemical makeup, or state of charge. A mechanical process sorts batteries for safe and efficient processing.
Batteries are mechanically broken down into inert materials, with no risk of fire or explosion. These materials are then further separated into two product lines: a so-called “black mass” of battery materials and mixed copper and aluminum.
Black mass comes from battery materials from cathode and anode batteries. Retrieved materials include lithium, nickel, cobalt, graphite, copper, and aluminum.
The copper and aluminum retrieved with mechanical safe size reduction can be commonly and efficiently recycled, especially in the case of aluminum. Black mass is transported to Li-Cycle’s Hub facilities for further processing into new batteries.
Hydrometallurgical Recycling: Hub Operations
At central hydrometallurgical recycling plants called Hubs, Li-Cycle processes black mass from cathode and anode materials into battery-grade end-products which can be reused to produce lithium-ion batteries. Li-Cycle is also finding other applications for its high-performing recycled battery material products.
Hydrometallurgy is the extractive metallurgy field method for obtaining metals from metal ore. Hydrometallurgical techniques employ water-based solutions to retrieve metals and are used to retrieve metals from ores and concentrate, as well as for recycling.
Li-Cycle’s hydrometallurgical recycling technology retrieves lithium, nickel, cobalt, and other metals from black mass. It produces these metals at such a high grade that they can be used to create new batteries.
The circuit at Li-Cycle’s hydrometallurgical recycling facility retrieves metal sulfate and carbonate materials from black mass with enough purity to later use the metals to produce cathodes and precursors for new batteries.
Retrieving 95% Battery Materials with Hydrometallurgical Recycling
This technology works with all formats and chemistries of lithium-ion batteries and can recover at least 95% of the batteries’ constituent materials (black mass). The following high-performing metal products produced from this black mass come with battery-grade purity levels.
Lithium carbonate
This micronized lithium carbonate can be used in applications such as lithium-ion and lithium-polymer battery production. The hard material is also used in glass and ceramics manufacturing.
Cobalt sulfate
Cobalt sulfate is used in cathode materials for lithium-ion and lithium polymer batteries.
Nickel sulfate
Nickel sulfate is another material that is used in cathodes for lithium-ion and lithium polymer batteries.
Manganese carbonate
Manganese carbonate derived from lithium-ion batteries’ black mass has several chemical applications. Through the process of calcining, it releases carbon dioxide as it decomposes. Manganese dioxide – used for dry-cell batteries and ferrites – is produced by manipulating this process.
Manganese carbonate also has applications in medicine as a hematinic, is used in health foods, and is employed in the production of ceramics and concrete.
Li-Cycle: Battery Recycling Company is Charging Forward
Li-Cycle, founded in 2016, is a rapidly growing battery recycling company. The company had its first pilot in operation in 2017, and a demonstration Spoke and Hub facility in Kingston, Ontario, in 2018.
The first commercial Spoke facility was commissioned in 2019 with the ability to process 2,500 tons of lithium-ion batteries annually. One year later, it was upgraded to twice that capacity. A second 5,000 ton-capacity facility was added in 2020, in New York, US.
The battery recycling company continues its growth with a third Spoke operation due to open in Arizona. This facility will be able to recycle 10,000 tons of lithium-ion batteries every year when it opens in 2022.
In early 2023, these facilities will be connected by a North American Hub site, which will process 60,000 tons of lithium-ion batteries’ retrieved materials annually.
References and Further Reading
Fathi, Habashi (2019) Metallurgy. Kirk-Othmer Encyclopedia of Chemical Technology. [Online] https://doi.org/10.1002/0471238961.1921182208091911.a01.pub2
Li-Cycle. [Online] Available at: https://li-cycle.com/
Reidies, Arno H. (2007) Manganese Compounds. Ullmann’s Encyclopedia of Industrial Chemistry. [Online] https://doi.org/10.1002/14356007.a16_123