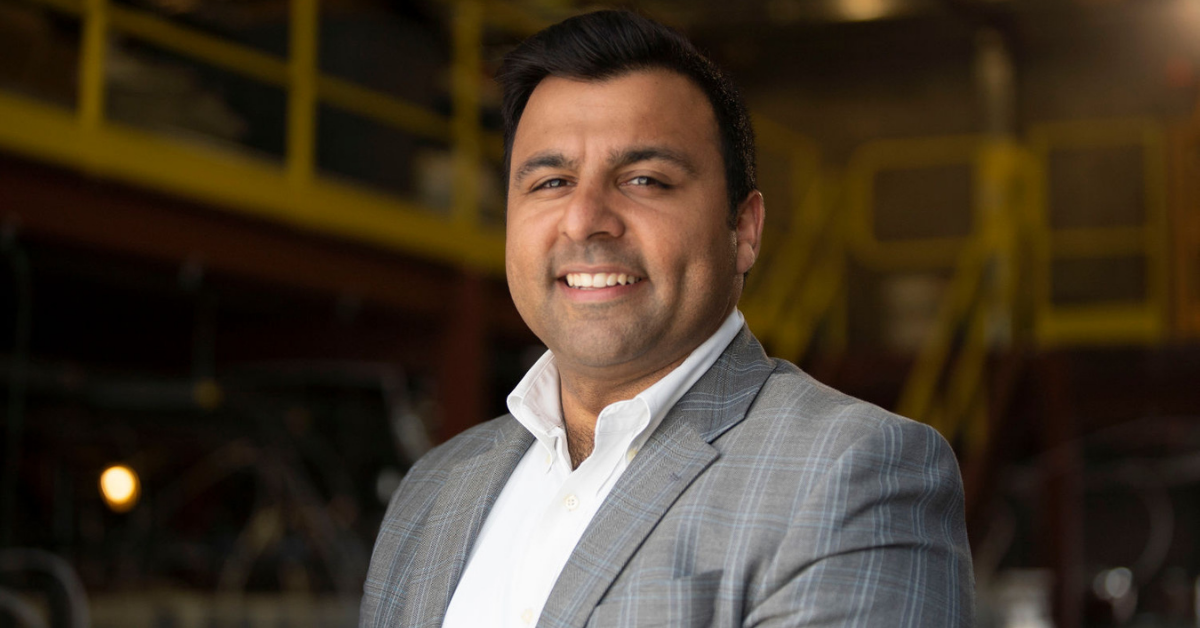
June 2, 2021
Interview: Ajay Kochhar, CEO Li-Cycle: “Electric Cars Will Create Battery Tsunami in the coming years”
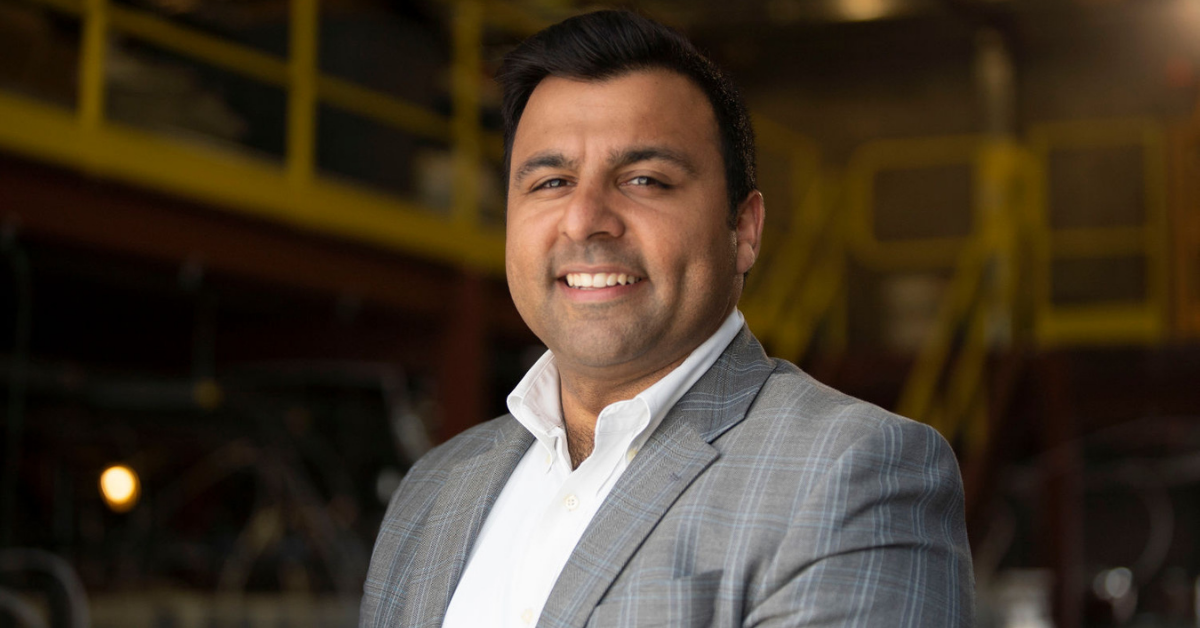
Founder and CEO of Li-Cycle, Kochhar provides an overview of the impact of batteries in the coming years and how the problem can be solved in a sustainable way
May 31, 2021
Original article published in Zev.News
Batteries are a hot topic in electric mobility. From the concern to obtain raw materials to their end-of-life destination. Aspects by the way used by some voices to question the real sustainability of electric vehicles.
The theme gains relevance in light of the exponential increase in electric vehicles expected for the coming years. A perspective that, outside the prism of concern, becomes an enormous opportunity for those capable of solving the problem and converting it into business.
Precisely the proposal of Canadian Li-Cycle. The startup founded in 2016 developed technologies to replace materials in the battery production chain. In a low-emission and scalable process, capable of partially replacing mining as a source of raw materials.
Li-Cycle is now operational. And accelerating as a business, as demonstrated by the beginning of the process for listing on the New York Stock Exchange. The startup claims to have one of the ways for electric mobility to achieve the so desired circular sustainability.
To learn how Li-Cycle delivers such a vision and give an overview of electric vehicle battery recycling, Zev.News heard from Ajay Kochhar, CEO and co-founder of Li-Cycle.
Zev.News – Ajay, what is your experience before founding Li-Cycle?
Ajay Kochhar – Me and Tim (Johnston), co-founder and Executive Chairman of Li-Cycle, come from the chemical and metals industry for batteries. We worked together at Hatch, a multidisciplinary global management, engineering, development and consulting firm. There we were focused on chemical and hydrometallurgy plants for the production of metals for batteries.
Zev.News – And what made you think: “Okay, there is a huge and growing problem, and I believe I can found a startup to solve it?
Kochhar – At Hatch, we noticed a huge hole in the global economy, which is increasingly electrified. We knew the industry, and we knew the problem. And, most importantly, we knew how to develop a game-changing solution. That was the reason why five years ago we left the company to found Li-Cycle. The goal was to answer questions everyone was asking: “What’s going to happen to all these lithium ion batteries? And before that: “What will happen to the leftovers from the manufacturing process?”
Zev.News – And what are the answers to these questions?
Kochhar – Solve the global issue of battery manufacturing waste and end-of-life batteries. At the same time, create a raw material supply chain to ensure a sustainable future for the planet. We saw opportunities in the lithium battery industry for two reasons:
First, the current process for obtaining raw materials is unsustainable. Second, the traditional (recycling) process uses high temperatures, which not only wastes approximately 50% of the materials, but is also harmful to the environment. That’s why we developed our Spoke & Hub Technologies™. It uniquely utilizes low temperatures and chemical liquids, which reduce costs and maximize profitability and recycling rates. Our process does not waste water, does not emit pollutants directly, and is the most energy efficient commercially available.
Zev.News – And what is the future vision of these answers?
Kochhar – Vision is an alternative to mining. Economically and environmentally more sustainable. Resulting in cheaper batteries and more affordable end products. Through solutions like ours, materials don’t have to go to landfills. Can be efficiently recycled.
Zev.News – Can you explain how the Li-Cycle recycling process works?
Kochhar – Li-Cycle has figured out how to reuse salvaged materials to make new batteries. In a circular and sustainable way. Technology already proven in the North American market. Our Spoke & Hub Technologies™ employs a two-stage model, using low temperature and liquid chemical solutions, which in addition to being cheaper compared to thermal melting, makes it possible to recover 95% of materials at an unparalleled rate.
The first stage is a mechanical shredder (Spoke), in which leftover batteries and end-of-life batteries are converted into intermediate products. Including “black mass”. Which is a powder containing materials such as lithium, cobalt and nickel (raw material for batteries). Facilities can process any Li-ion batteries. From the smallest to electric car batteries. Or even bigger.
Through shredding, we produce three key products: chopped aluminum and copper, which is the metal associated with lithium-ion batteries, and a low-density plastic mixture. Both have secondary markets. To which we can sell. The third element is the most important: the black mass (which will be provided to our future Hubs processing centers). At the centers, we will process the black mass recovered from batteries through a hydrometallurgical circuit. To thus produce valuable materials such as lithium carbonate, cobalt sulphate and nickel sulphate, which can go back to the economy.
Zev.News – Li-Cycle recycles all types of Li-ion batteries. However, according to the startup’s projections, in 2025 electric vehicle batteries will be the main source. What are the differences in recycling electric vehicle batteries compared to electronic devices, for example?
Kochhar – Electric car batteries will be the biggest source of recycling, driven by the revolution taking place globally. Global sales of electric vehicles were approximately 2.5 million in 2020. It is projected to reach 9 million in 2025. And 26 million in 2030. Electric vehicle batteries are quite heavy. With approximately 250 kilos of valuable material. And they will create an end-of-life battery tsunami for years to come. The world needs to be prepared for efficient recycling. That’s where Li-Cycle comes in. When it comes to recycling electric vehicle batteries, the biggest challenges are the thermal hazard of the batteries (lithium is flammable), the dimensions and quantity (there will be many). Which raises the question of scale.
For processing lithium ion batteries, our shredders operate at a low temperature, and shred the submerged batteries into a proprietary solution, which reduces thermal risk and prevents harmful emissions. This gives us the ability to safely recycle electric vehicle batteries. As for size, our shredders are equipped to process them. Our newly announced plant in Phoenix (Arizona) is designed to process electric car battery packs without any disassembly. Today, we still minimally disassemble them.
Zev.News – But there is still another issue, the aforementioned “battery tsunami”…
Kochhar – As we plan to launch 20 shredding plants (Spokes) and four global centers (Hubs), this will result in the capacity to process, respectively, 105,000 and 240,000 cubic tons of lithium-ion batteries per year. This equates annually to the batteries of 210,000 electric cars in our shredders, and black mass and battery leftovers from approximately 720,000 electric vehicles in our centers. Clearly, we will be prepared for the flow.
Zev.News – You also mentioned a curious point a few times. And that perhaps most of our readers are not aware of: material leftovers during battery production. How will this aspect be impacted by the growth of electric cars?
Kochhar – When producing batteries there is a rate of leftovers and rejects, typically 5 to 10%. But regardless of the percentage of waste in production, one aspect is certain: in the immediate future, it will be the main factor for growth in battery recycling. Before the end-of-life battery tsunami. As the numbers of battery factories increase, the volume of leftovers will increase proportionately. The electric vehicle revolution is fueling the growth of leftovers. Therefore, it is imperative that battery recycling grows in tandem with this exponential increase. Battery makers may see leftovers as waste, but Li-Cycle sees them as a huge business opportunity. Opportunity that delivers value to our customers. Let’s not just solve the leftovers problem,
Zev.News – In addition to government impositions, industry and consumers today consider the origin of raw material in contract and purchase decisions. That is, it is no longer just about choosing the lowest price. However, price is still an important factor. Today, what is the difference in the price of raw material extracted from nature compared to recycled ones? And what is the projection for the next 5 to 10 years.
Kochhar – Li-Cycle is a source for critical and strategic materials: lithium, nickel and cobalt. Just to name a few. We are at the epicenter of three rapid, gigantic and critical changes to the zero carbon economy: the electric vehicle revolution, the local scarcity of raw materials and the need for sustainable recycling. And considering the favorable wind provided by government aspects, associated with the scarcity of raw materials, we are cheaper than any mining.
Today, recycling is imperative to the raw material chain. And the need will only increase in the next 5 to 10 years. And an important aspect cannot be overlooked: the materials used in lithium ion batteries are finite. We’ll run them out if we’re not careful. You can imagine how this threatens prices in the markets. Li-Cycle is a business with a patented solution already operational, and we are poised to grow as our customers continue to grow, electrifying vehicles and expanding the application of batteries.
Zev.News – The first generation of electric vehicles hit the streets a few years ago. So, proportionally to the growth in production, there is still not as much material available from this source for recycling. What is your view on the scenario?
Kochhar – Although the huge amount of batteries that end up coming from electric vehicles has not yet reached the market, today there is still a huge amount of batteries that need to be recycled. By 2020, 456 cubic tons of ion and lithium were available for recycling. That number will grow to 1.3 million by 2025. And to 2.6 million by 2030. It’s important to keep in mind that even the best manufacturing process produces waste requiring recycling at a rate tied to electrification.
There is not only a lag in recycling volume due to the proliferation of lithium-ion batteries and electric cars. There is actually a lot of material available to be recycled today. This was before the battery tsunami caused by electric vehicles that hit the streets a few years ago or are in circulation.
Zev.News – Ajay, in closing: how operational the Li-Cycle is today. And what are the goals for the next 5 to 10 years?
Kochhar – We are fully operational. Today we have two shredding plants, one in Kingston (Canada) and one in Rochester (New York). We also recently announced plans for a third shredding facility in Phoenix, Arizona, next to what will become an end-of-life battery generation core. We have more than 40 commercial contracts with chip suppliers and agreements with the largest vehicle and battery manufacturers for electric vehicles. The road is promising. We recently started the merger with SPAC Peridot Acquisition Corp. And once the transaction is completed, we will become a company listed on the New York Stock Exchange (LICY). The capital will allow us to continue growing as we plan to launch 20 Spokes and 4 Hubs by 2024. It’s just the beginning. I look forward to the next milestones, working towards a sustainable future.