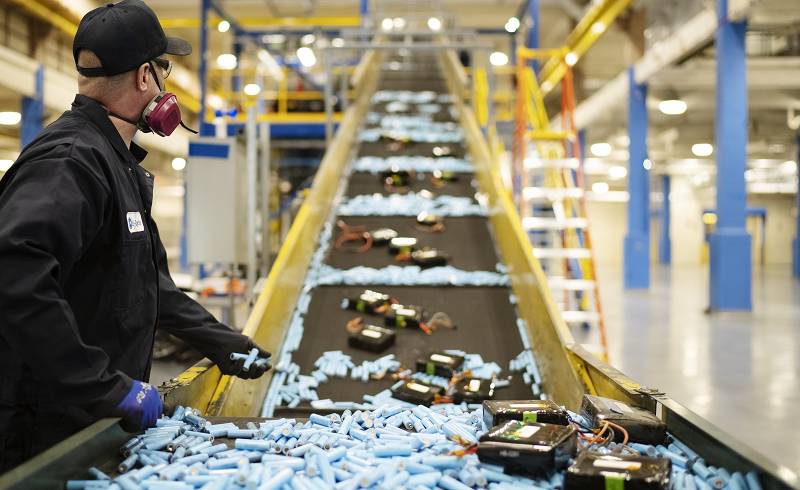
October 13, 2021
Carmakers try to head off supply crunch with battery recycler investments
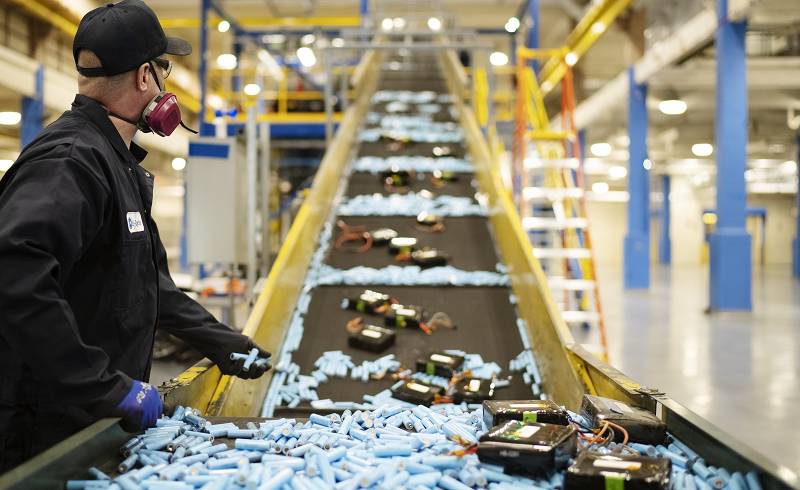
October 13, 2021
Original article published in S&P Global
Investors are pouring hundreds of millions of dollars into recyclers of battery materials, hoping to ease metal shortages, localize supply and make the electric vehicle industry more sustainable.
Demand for lithium, nickel and other battery metals will soar in coming years as the world works to decarbonize. Battery recycling is poised to ease anticipated bottlenecks for those metals while enabling battery-makers to keep part of their supply chains close to home.
Major players have begun investing in recycling upstarts: Koch Strategic Platforms will put $100 million into recycler Li-Cycle Holdings Corp., and Ford Motor Co. will partner with recycler Redwood Materials Inc. as part of its $11.4 billion electric vehicle expansion plans. Lithium miner Ganfeng Lithium Co. Ltd. already uses recycled materials in its own battery products. And a recent agreement between mining giant BHP Group, Japanese automaker Toyota Tsusho Corp. and Japanese battery-maker Prime Planet Energy & Solutions Inc. opens the door to expanded recycling infrastructure when metal supply deficits loom.
“We’re likely to see shortages of materials like lithium, cobalt and nickel,” said Asad Hussain, a senior analyst at PitchBook, a financial research provider. “What happens when every country is trying to decarbonize? We’re all competing for the same limited pool of resources to hit aggressive EV mandates and targets. Battery recycling is going to be an integral part of making those supply chains much more sustainable.”
Think globally, recycle locally
Clean energy technologies’ share of demand for lithium could surge by upwards of 90% over the next 20 years as the world strives to meet the emissions-reductions targets outlined in the Paris Agreement on climate change, according to the International Energy Agency. By 2025, the world could see a 30,000-tonne shortage in lithium carbonate equivalent, according to S&P Global Market Intelligence. Primary nickel supply may face a deficit in 2021, falling short about 128,000 tonnes. The anticipated deficit for refined cobalt has decreased in recent months, but markets will remain tight through at least 2025.
Recycled lithium, cobalt, nickel and copper are providing a negligible share of battery materials in 2021, but they will make up an estimated 8.1% of metals demand by 2040, according to the IEA. That may seem modest, but analysts agree that using these secondary materials, even in limited quantities, could help soften the need for new mining, regionalize supply chains and make electric vehicle manufacturing more environmentally and economically sustainable.
“Recycled materials are going to play a key role in filling the imbalances of supply-demand,” Landon Berns, a trader specializing in battery raw materials at Traxys, a global commodity trader and merchant focused on metals, said at an Oct. 6 webinar hosted by Li-Cycle.
Supply bottlenecks and consequent delays fueled by the COVID-19 pandemic have exposed vulnerabilities in global supply chains. Prices for lithium, copper and nickel have soared, and shipping backlogs have only exacerbated the problem. Recycling can ease some of those limitations.
“What recycling does is it creates localized supply chains where governments, [original equipment manufacturers] and battery manufacturers can have the materials that they need to buy and make the things that they produce local,” Berns said.
China’s Ganfeng Lithium, the world’s fourth-largest lithium producer, has a recycling arm that supplies its own battery production with most of the nickel, cobalt and manganese it needs, Xiaoshen Wang, chairman of Ganfeng Lithium’s sustainable development committee, said during an Oct. 5 conference hosted by Reuters.
Reduce, reuse, Li-Cycle
Li-Cycle announced in September a $100 million investment from Koch Strategic Platforms, a subsidiary of Koch Industries, Inc., to accelerate the growth of recycling facilities around the world. As part of the investment news, Li-Cycle also said it would explore possible collaborations with multiple Koch businesses, including Koch Engineered Solutions LLC, to expand the reach of the company’s operations.
Launched in 2016, Ontario, Canada-based Li-Cycle operates several commercial lithium-ion battery recycling facilities in the U.S. and Canada. The company uses a closed-loop process to recycle lithium-ion batteries, including manufacturing scrap from dealerships, to return battery-grade end products to the market.
“The need for lithium-ion battery recycling grows in lockstep with EV manufacturing volumes and the batteries that power them,” Li-Cycle president, CEO and co-founder Ajay Kochhar said during a Sept. 29 webinar. “The pace of manufacturing facilities for batteries has continued to exceed our expectation of only several months ago.”
By 2025, Li-Cycle plans to build 20 “spokes,” or facilities where end-of-life lithium-ion batteries are shredded to recover active materials, including plastics, copper, aluminum foils and battery anode and cathode materials. Li-Cycle also intends to deploy more “hubs,” or centers where the anode and cathode materials are refined to create high-purity battery chemicals for reuse.
The company is rapidly accelerating its network worldwide in anticipation of the “tsunami” of spent lithium-ion batteries in need of recycling within the next decade.
“We see that more into the late 2020s,” Kochhar said of the expected flood of end-of-life electric vehicle batteries.
Based on forecasts for electric vehicle sales, the volume of spent batteries retired from cars will likely balloon in the coming decades.
Ford has a better idea
Miners and automakers are also trying to hop on the recycling bandwagon.
As part of Ford’s $11.4 billion plan to build electric vehicle manufacturing campuses in the U.S., the automaker said it would expand infrastructure for refurbishment and recycling of batteries too.
“Ford is evaluating all avenues to secure raw material supply for its EV strategy, and this includes recycled feeds and domestic mining to support vertically integrating EV manufacturing,” a spokesperson for Ford said by email.
Nevada-based battery recycler Redwood Materials plans to partner with Ford to implement a recycling system. In July, Redwood Materials announced that it secured over $700 million in external investment to develop a closed-loop supply chain for electric vehicles and energy storage products from a handful of investors that included Goldman Sachs Asset Management LP, Canada Pension Plan Investment Board, Breakthrough Energy Ventures, Fidelity and Amazon’s Climate Pledge Fund.
On Oct. 4, BHP Group, the world’s largest miner, announced that it would launch a joint venture with automaker Toyota Tsusho Corp. and battery-maker Prime Planet Energy & Solutions to supply raw materials, including nickel sulfate, for electric vehicle batteries. The agreement left open the option of developing a battery recycling system at BHP’s Nickel West operation in Western Australia.
“This partnership has great potential to secure competitive raw materials for the EV value chains as well as to create battery material recycling loops, which is crucial for EV development in the future,” Masaharu Katayama, the COO of Toyota Tsusho’s metals division, said in a statement.
Waiting for batteries to die
The nascent battery recycling industry will need to overcome myriad hurdles if they want to keep up with the expected rush of used batteries.
A a surge in electric vehicle adoption rates in recent months will bring penetration rates globally to 9.6% by the end of 2021, according to Market Intelligence analysts, and it will be years before those batteries are ready to go to recyclers.
“Battery lifespans in EVs are reaching and surpassing 10 years, so recyclers will generally be seeing supply of materials based on demand 10 years prior,” said Max Reid, a Wood Mackenzie research analyst specializing in battery raw materials. “So, [recycled battery materials] may not be able to impact the supply chain this decade whilst EV penetration is still relatively low.”
Primary mined material will still be needed to meet the anticipated ramp-up in demand for batteries.
“We’re still going to be reliant on mining for quite a while,” said Rebecca Ciez, an assistant professor of mechanical engineering at Purdue University. “The scale of demand is just so big.”
Make it mandatory
Regulations incentivizing lithium-ion battery recycling have been slow to catch up with growing production.
About 99% of lead-acid batteries in the U.S. are recycled, due to widely adopted recycling requirements. But comparable mandates do not exist for lithium-ion batteries, which are recycled at a rate of roughly 5%, according to a 2019 report by the International Institute for Sustainable Development.
That could change with proposals coming down the pipeline in the U.S., Canada and the European Union.
“Europe has been more active in this space,” Ciez said of lithium-ion battery recycling regulations. “Europe has really tried to expand their definitions to include lead-acid batteries, but also electric vehicle batteries, [specifying] how much of them needs to be recycled and specifically calling out metals they think are most important.”