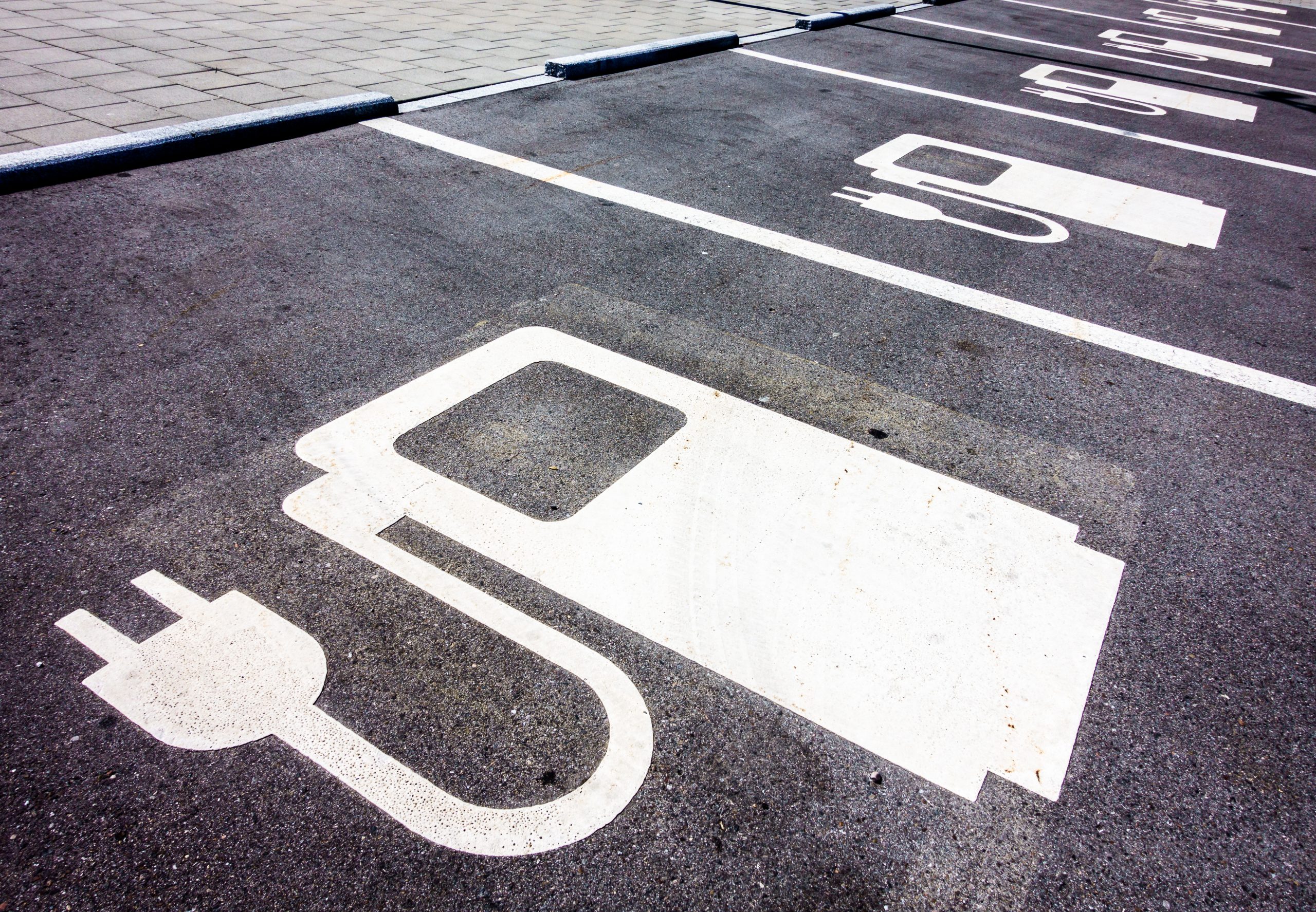
April 26, 2021
Can Ontario boost EV battery recycling before it’s too late?
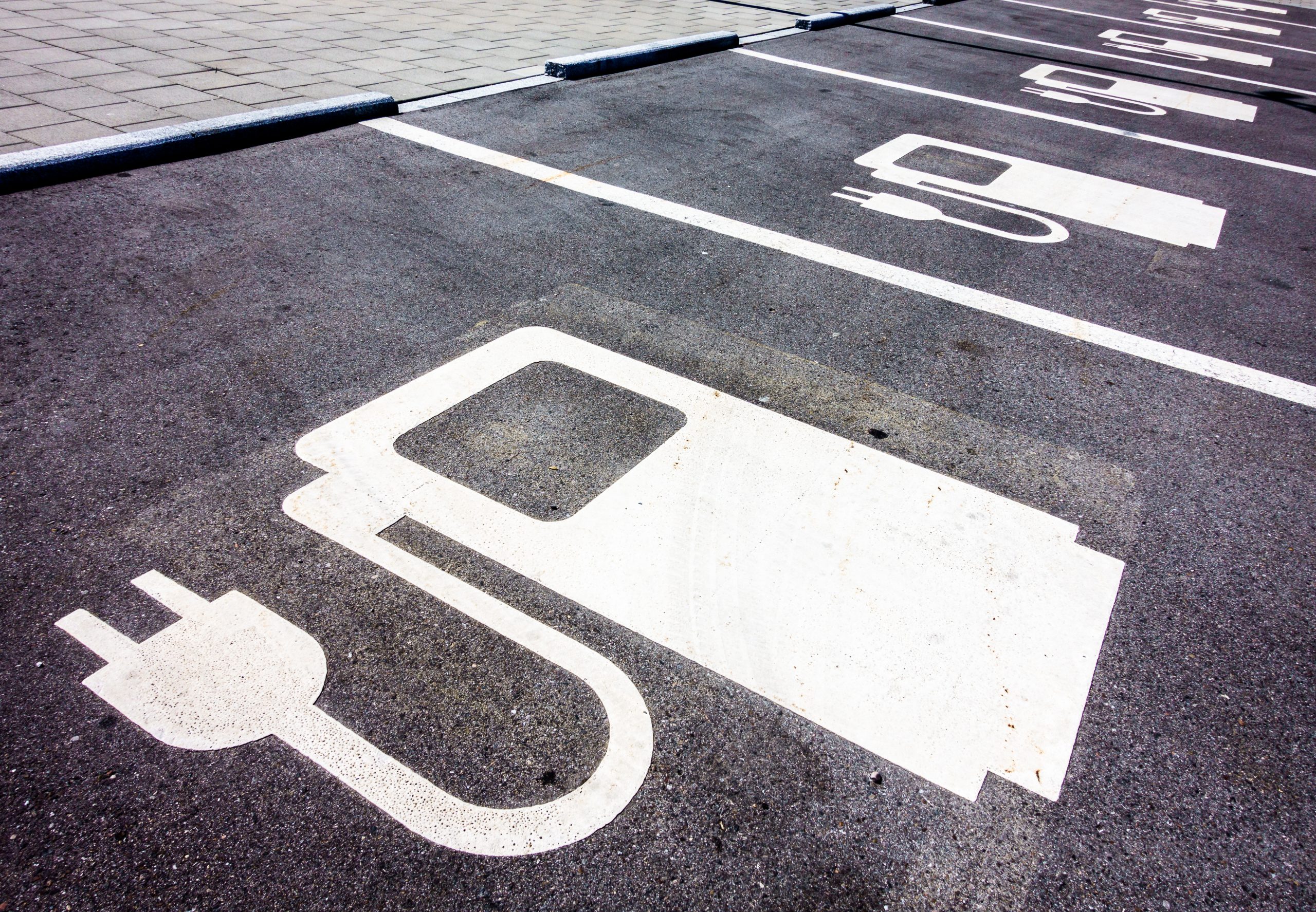
Lithium-ion batteries are meant to power the future — but that won’t happen if we don’t tackle recycling
Original interview published in TVO
April 22, 2021
First, batteries that once powered an iPhone, a laptop, or an electric car are loaded onto a conveyor belt at Li-Cycle’s Kingston facility. They are guided into a feed hopper and disappear into a vat, where they’re shredded and stripped.
Roughly 15 minutes later, the plant spits out its three end-products: shredded metallic cloth of copper and aluminum; low-density plastic; and black mass (a mixture of battery chemicals and metals). They’re then funnelled into bulk bags and loaded onto pallets, ready to ship.
The metal and plastic are sold off to other producers or recyclers, while the black mass is driven to another facility, where it goes into reaction tanks made of steel or plastic. Here, it soaks in an acid bath, which dissolves the metals, and works its way through multiple stages of solvent extraction. Over the course of 24 hours, the process, known as leaching, transforms the sooty black mass into striking piles of battery chemicals: Dazzlingly turquoise nickel sulphate. Cobalt sulphate, which looks like glittering ochre. Manganese carbonate, which resembles playground sand. And fine white lithium carbonate, like piled chalk dust. These chemicals will then be sold back to manufacturers and used in new batteries.
Li-Cycle claims to be the largest recycler of lithium-ion batteries in North America. This year, it has the capacity to process 10,000 metric tonnes of battery material through contracts with Volkswagen, Porsche, Honda, and General Motors, among others. When Tim Johnston and Ajay Kochar founded the company in 2016, it was a solution waiting for a problem: a heap of batteries once used to power electric vehicles and in need of recycling. “People told us that this was going to be a problem in five to 10 years’ time,” Johnston says. “Fast-forward five years’ time, and now we’re sitting in this very interesting crossroad.”
That’s because the first wave of electric vehicles is now coming off the roads — and creating a thorny environmental predicament. Swapping gas-powered engines for battery-powered alternatives is essential if Canada is to meet emissions targets and avoid the worst effects of climate change. Lithium-ion batteries will become only more important in daily life, as the clean electrification of the power grid is a necessary step toward decarbonization. But that presents its own threats. Electric cars do not run on truly renewable energy: the batteries require finite materials that are mined from the earth at both an environmental and human cost. At the end of its lifespan, a discarded battery is dangerous to handle and can leak hazardous material in a landfill.
Roughly 3.4 million electric vehicles were produced globally in 2020. By 2024, some projections put the number near 13 million — others go even higher. The global market for EV batteries is projected to be worth nearly $1 trillion in 2030, when the International Energy Agency predicts that nearly one in three new vehicles on Canadian roads could be electric. “We have maybe 20 years before all the vehicles become electric,” says Asmae Mokrini, the team lead in materials for energy technology at the National Research Council’s lab in Boucherville, Quebec. “The actual supply chain will not withstand the transition without recyclable materials.”
Ontario is trying to carve out its place in the EV market. The 2021 budget highlighted $4.3 billion in investment from automakers to build electric vehicles in the province, introduced tens of millions for research in the sector, and announced a strategy for extracting battery minerals. The federal budget, announced Monday, likewise included funding for EV research and the mining of battery materials. But experts say that any strategy to become a leader in electric vehicles must include battery manufacturing and recycling.
Zhongwei Chen, a chemical-engineering professor at the University of Waterloo and the Canada Research Chair in advanced materials for clean energy, says that a manufacturing future requires a “closed loop” — raw materials, battery manufacturing, automanufacturing, and an end-of-life strategy. Recycling offers a solution to two of those steps.
“We have to recycle the lithium battery to avoid pollution, right? If we don’t recycle, if we bury them underground, that’s not good for the environment,” Chen says, adding that “the elements used in the lithium battery are a limited resource. Lithium, for example: globally, we don’t have enough lithium for the future.”
The modern lithium-ion battery, which traces back to developments in the 1970s and has been in commercial use since the early 1990s, has three basic parts: a graphite anode, the negative end; a lithium-cobalt oxide cathode, the positive end; and the electrolyte, a liquid substance that sits between them. Electrically charged atoms called ions travel between the two ends, using the electrolyte to create an electric current, which powers whatever is hooked up to the battery. Today, cathode chemistries vary and are always changing, but the basics remain largely the same.
The battery is quickly becoming a crucial piece of global infrastructure because it packs a lot of power into a small package, is cheap to make (and getting cheaper), and can be manufactured at a large scale. Looking forward, experts say, these batteries will not only power our cars, buses, trucks, and planes, but also be integral to our grid — storing energy to power our homes, our factories, and our cities.
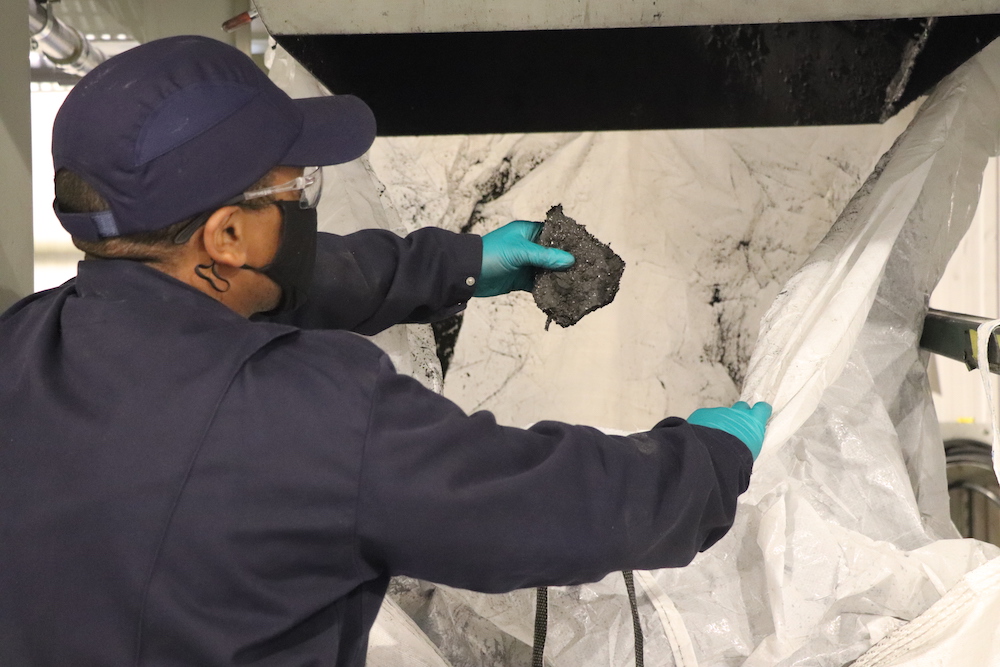
Scientists such as Chen and Gisele Azimi, an associate professor of chemical engineering and materials science at the University of Toronto, are working on so-called post-lithium batteries that may be more efficient or last longer, but few expect an innovation that could remove lithium-ion from prominence. “Even if they become viable and commercially available, they will not replace lithium-ion batteries,” Azimi says. “Lithium-ion batteries are so intertwined with our life that we cannot eliminate them and put them aside and use, for example, aluminum-ion batteries. We will use them in parallel, so you will always have a stream of lithium-ion batteries.”
The recycling process for lithium-ion is more complicated than for a typical alkaline battery, which is partially why less than 5 per cent of the batteries are recycled worldwide. Those that are recycled usually go through one of two processes: hydrometallurgical, which uses a liquid solution; or pyrometallurgical, which uses fire. Pyrometallurgical solutions, otherwise known as smelting, require a great deal of energy — which is generally created by fossil fuels.
In Canada, recyclers including Li-Cycle, Lithion in Quebec, and Retriev Technologies in British Columbia rely on hydrometallurgical technology.
But it comes with its own drawbacks. The batteries require expensive pre-processing before leaching, and the chemicals used can themselves be harmful to the environment. Li-Cycle, which turned a former Goodyear processing plant into an open-concept office and facility in Kingston, says its closed-loop system means that no hazardous material is left behind. The company says its process recovers 95 per cent of the raw materials and produces no impact emissions, no wastewater, and no solid waste.
Ben Yu, the team lead for mineral processing at the NRC’s Ottawa lab, is, alongside Mokrini, part of a project called End of Life Lithium-Ion Battery Options. Made up of 25 scientists from 10 NRC labs across Canada, it has partnerships with the University of Toronto and Dalhousie University. He says that “you’ll hear companies say they’re 95 per cent recycling the material, but a lot of the times they may not be recycling back to a material use.” While companies may recover that material, it might not be going back into batteries. It may not economically viable or perform as well as fresh raw material, or there could be gaps in the supply chain.
At Li-Cycle, chemicals are targeted for batteries, but some materials will wind up in other industrial applications, including steel manufacturing and lubricants. Johnston and Kochar are anticipating that that their “spoke and hub” production design will make the company financially successful — local spokes do the pre-processing and feed to regional hubs, which do the leaching. The Kingston plant was the company’s first spoke and is home to a small-scale hub for research and development. The first commercial hub, set to open in Rochester, New York, is in late-stage development.
While the company is based in Ontario, it plans to go global. Over the next five years, it intends to open 18 more spoke facilities and four hubs across North America, Europe, and Asia. Those plants will process 100,000 tonnes of material per year and 240,0000 tonnes per year, respectively. “So it’s going to be a great time from a Li-Cycle perspective — a lot of work to be done,” Johnston says. “But we see that, in five years’ time, and then going beyond that to that 10-year horizon, Li-Cycle will be a core part of the global infrastructure when it comes to dealing with waste materials generated from the production of lithium-ion batteries.”
But there will be challenges. While Li-Cycle may stand out in North America, Johnston acknowledges the sector here is years behind China — and most of the world’s recycling is concentrated in Asia. The company will also have to contend with the fluctuating costs of mined materials.
The batteries themselves will change, too. Manufacturers are constantly adjusting chemistries to reduce cost or extend life. What comes off the roads next year might no longer be what manufacturers want — and they’ll also likely skew toward cheaper materials. Then there’s the fact that some chemistries lend themselves more toward recycling than others, meaning the business is one of constant tinkering.
Yu, whose lab is in Ottawa, says that, in the past five years, preferred chemistries have already changed multiple times: “With recycling, one of the issues is you have to stay very flexible and be adaptive.”
Beyond tweaks, lithium-ion batteries are on the verge of a major shift. The current design, with a liquid electrolyte, tends to explode in high temperatures, which has led to recalls of both electric vehicles and smaller electronics in recent years. Scientists believe a solid-state battery would solve that problem. In the United States, some think a glass electrolyte could be the answer. Chen has spent five years working on a solid-state battery. “We can do very important things with this battery,” he says.
New recycling processes might also emerge. A third form, called direct recovery, is popular among researchers for its simplicity and potential cost-saving — it recovers and reuses materials without first causing a chemical change. Mokrini’s lab, which has a battery-manufacturing line, is working on direct recovery of material.
However, much of the related research is being conducted by the ReCell Centre; created by the U.S. Department of Energy in 2019, its purpose is to study and develop the future of battery recycling — with a focus on direct recovery. In the United Kingdom, 50 scientists are researching the future of battery recycling and sustainable-materials management as part of the ReLib project, led by the Faraday Institution and the University of Birmingham. “I think in the U.S. and Europe they understood [the importance of recycling],” Mokrini says. “So that’s why they are really putting a lot of efforts in introducing recycling.”
The NRC project, Canada’s national equivalent, is just one part of the larger federal advanced-clean-energy program. It has three main areas of focus: diagnosing the actual health of a supposedly end-of-life battery, materials-recycling research, and adapting global research to a Canadian context. “You need to charge your battery, and we’re obviously going to plug into a Canadian electrical grid for energy,” Yu says. “So we have to understand from a life-cycle assessment perspective what happens if it’s plugged in in Ontario versus in Alberta.”
Back in Toronto, Azimi, who is also the Canada Research Chair in urban-mining innovation, is herself working on a battery-recycling project. Her lab uses supercritical carbon dioxide — which has been taken from the air and run through a reactor to boost its temperature and pressure — as a solvent. It produces no waste and limits the need for hazardous chemicals, she says. Although, like most of the fledgling alternatives, it is still in the research phase, she hopes that in two to three years it could be ready for a pilot. “Our process really doesn’t consume chemicals that much,” she says. “And [carbon dioxide] is available at large volumes, so it’s really an environmentally sustainable process.”
Despite its stated support for the burgeoning electric-vehicle industry, Ontario is not home to a battery manufacturer and does not have a plan for battery recycling. In an emailed statement to TVO.org, a spokesperson for the Ministry of the Environment says, “The technology for repurposing or recycling EV batteries is still being researched and developed, and many options are being considered. The ministry will continue to monitor this industry to determine if any regulations are needed in the future.”
Vic Fedeli, the minister of economic development, says that the province understands the importance of the sector: “In order to have a good sales position in the electric vehicle sector, you need to have proper integrity through the whole system — and that starts with clean energy. And it continues all the way through the reusing and recycling. It’s all integrated. It’s hard to have one without the other.”
Li-Cycle and Lithion have accessed funding through Sustainable Development Technology Canada, an arm’s-length foundation funded by the federal government, and Johnston credits local governments for their support. But the National Research Council’s project is not at the scale of ReLib’s or ReCell’s, and there is no comparable cross-institutional project focused specifically on recycling. Yu notes that Canadian versions may not be necessary, as his scientists can build off international research — and that his team is in contact with both ReLib and ReCell. “When it comes to recycling, and in general GHG emission as a whole, it really is not restricted by borders — it’s a global effort.”
But coordinated research does have benefits. “I think that would be a useful thing to have, and I think that will be the future,” Azimi says, adding that she and her colleagues at U of T met with a representative from the provincial government last week. “It really is a new topic — you know what I mean? It’s becoming hotter and hotter every day, but this really started very recently. Maybe in recent years, it has become so obvious that this is the direction we have to move to.”
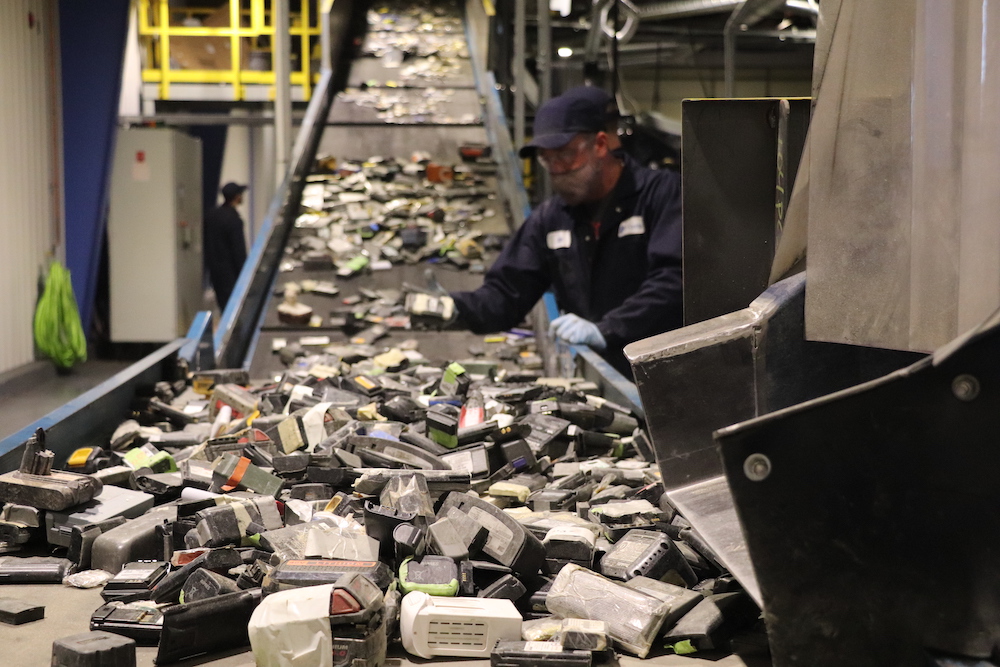
Batteries might one day be designed to be recycled, Yu says. “We always design batteries thinking of performance, about the energy density, resolving range anxiety — but we never thought about, how could we design a battery with recycling in mind so that it makes it easier and more efficient? I think that’s really the next thing to do.”
Mokrini’s lab is working on ways to introduce recycling into the manufacturing process — for example, by replacing an existing polymer coating with one that is water soluble. The challenge is to avoid sacrificing performance. “I think it’s a matter of time, and it’s going to come, because we don’t actually have a choice,” she says. “Demand for the raw materials, in general, for batteries will force industry to think about recycling materials from the beginning.”
Regardless of their make-up, lithium-ion batteries will soon power an increasingly large portion of our daily lives, and EV batteries will be crucial. When a battery is no longer suitable to power a car or a bus, it can find a second life providing, among other things, grid storage, until it dies completely. Chen says that, moving forward, electric vehicles will also be able to plug in to the power grid and provide storage — drivers may even have the option to sell excess power back to the grid. “Your vehicle could be a very important energy-storage component of the whole power grid,” he says. It’s easy to imagine a time when second-life batteries and cars running off batteries made of recycled materials play a critical role in powering the province.
“All of Ontario could be connected,” he says. “And that’s what I believe is the future.”
Next articles
View AllRochester companies move tech forward, innovate amid pandemic
In the News, Rochester
April 23, 2021
Original interview published in Rochester Business Journal April 09, 2021 Innovation and technology has been part of Rochester’s core for more than a century, and the path paved by the...
Li‑Cycle Shareholders Approve Plan of Arrangement
Press Releases
April 23, 2021
Original article published in Businesswire TORONTO–(BUSINESS WIRE)–Li‑Cycle Corp. (“Li‑Cycle” or the “Company”), an industry leader in lithium-ion battery resource recovery and the largest lithium-ion battery recycler in North America, announced...
Expansion into Arizona is just the ‘top of the first inning’ for battery recycler Li-Cycle
In the News, Arizona
April 22, 2021
Original interview published in BNN Bloomberg April 20, 2021 As the first generation of electric vehicles nears retirement, more voices in the industry are highlighting the importance of recycling components...