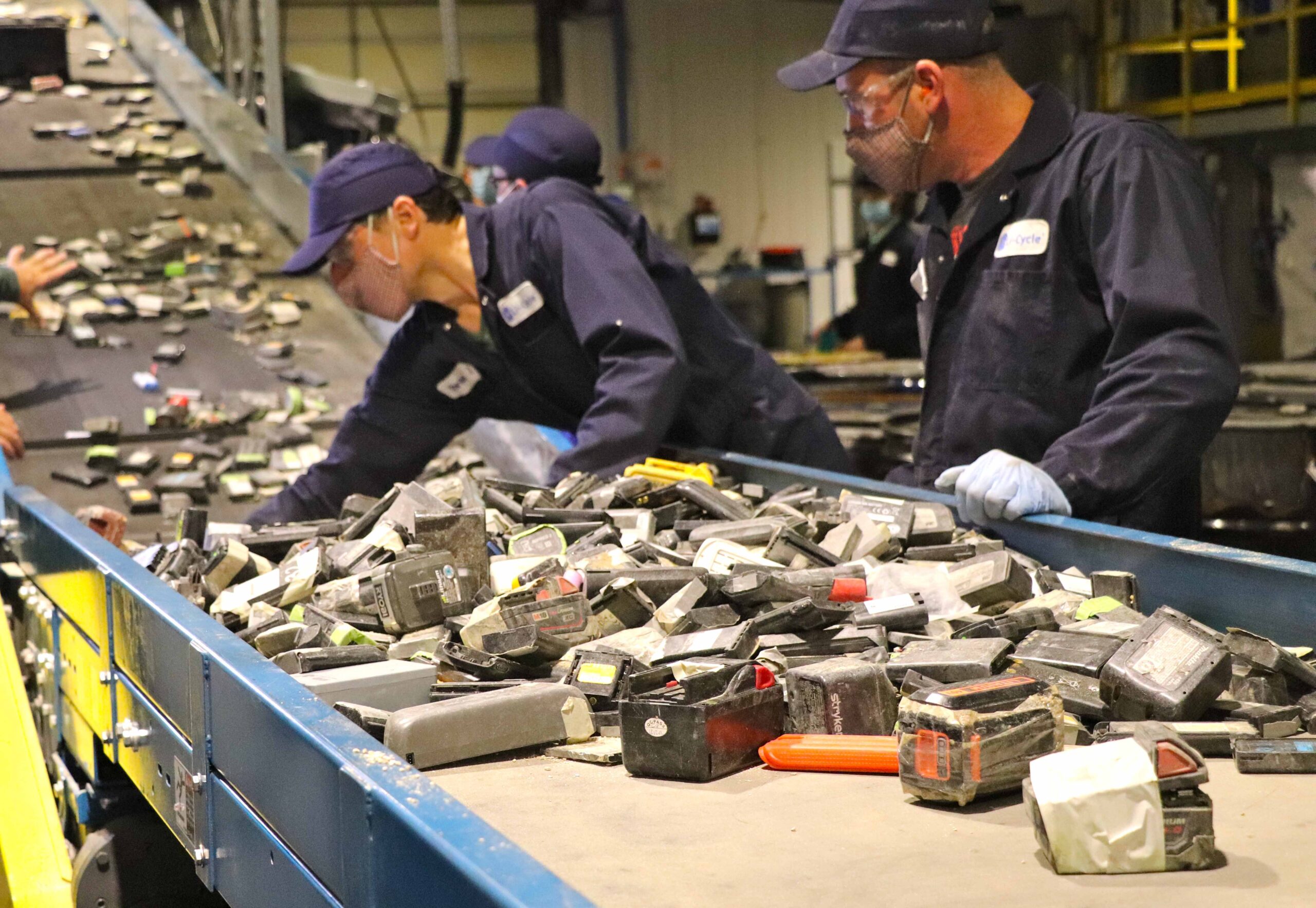
February 3, 2021
What to do with the mounting heap of spent lithium-ion batteries – Recycle them!
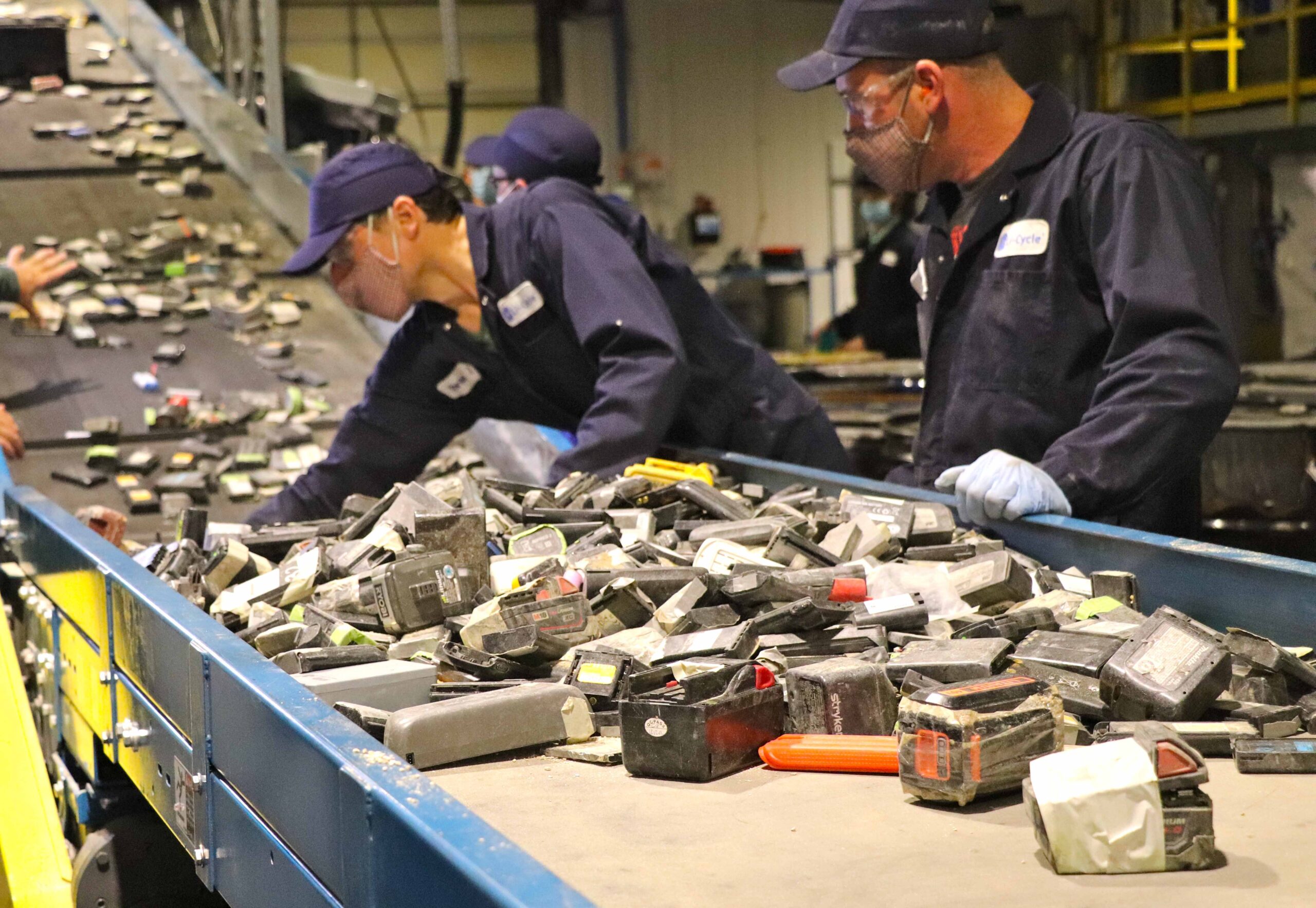
Original article published in Green Energy Futures
February 2, 2021 – David Dodge
Lithium-ion batteries have been the secret sauce fueling the explosion of super portable, wireless electronics such as smartphones, laptops, tablets and tiny wireless products such as Bluetooth headphones.
They are also what makes the modern electric vehicle viable and able to feature ranges of 500 kilometers and more.
But increasingly people are worried about what to do with the mounting heap of spent lithium-ion batteries that are full of things like nickel, cobalt and lithium and if mishandled can catch fire.
This is exactly what AJay Kochhar and Tim Johnston were wondering as they were providing engineering services to lithium-ion battery producers around the world.
At the time people were working on extracting nickel and cobalt from the spent batteries, but Kochar and Johnson wanted to be able to also extract the lithium, and reprocess the elements back into a raw material that was good as new.
Li-Cycle co-founder Tim Johnston Li-Cycle co-founder Ajay Kochhar
So they formed Li-Cycle, a battery recycling company based in Kingston, Ontario.
Their goal was to take a challenging waste problem and make lithium-ion batteries part of “a truly circular and sustainable product.”
Today Li-Cycle has operations in Kingston, Ontario and Rochester New York and appear ready to expand to other locales around the world with their patented process.
There are “about half a million tons per year globally of lithium-ion batteries reaching the end of life and available for recycling” around the world, says Kunal Phalpher, chief commercial officer at Li-Cycle.
Solution to growing pile of battery waste
With the rapid ascent of electric vehicles this Li-Cycle expects this number to soar to 2.5 tonnes of waste per year by 2030.
“And that is a large amount of high value materials like cobalt, nickel, lithium, that can be recovered and brought back into the supply chain to really create a circular economy,” says Phalpher.
Li-Cycle has developed a hub and spoke process that they say can recycle up to 95 per cent of the materials in these lithium-ion batteries.

Spoke – A smaller strategically located facility where spent batteries are collected and shredded. Li-Cycle has facilities in Kingston, Ontario and Rochester, New York.
Hub – A large facility where the recovered “black mass” is re-refined into battery quality raw materials. Li-Cycle has a pilot facility in Kingston, Ontario and is building a major hub in Rochester, New York.
Recycling 10,000 EV Batteries
“We’ve built two 5,000-tons per year facilities, one here in Kingston, Ontario, Canada, and one in Rochester, New York. Each of these can process the equivalent of ten thousand electric vehicles a year,” says Phalpher.
At Li-Cycle’s two “spoke” facilities spent lithium-ion batteries are collected from electronics and electric vehicles. Here the batteries are shredded and separated into a “black mass” which contains the reusable materials (nickel, cobalt and lithium) that can be recovered at a hub facility.
The spoke facilities are located close to markets where spent batteries need to be recycled.
“Kingston’s right smack dab between the Toronto-Montreal corridor,” says Phalpher adding from a collection point of view this is right in between the Ontario and Quebec markets which have high electric vehicle penetration and large quantities of electronic waste. The other location is Rochester, New York.
Li-Cycle built a pilot scale hub plant in Kingston, Ontario, but a large $175 million production plant is under construction in Rochester, New York.

“So that [Rochester hub] can take equivalent of 60,000 tons per year of material, equivalent to about 100,000 electric vehicles.”
There’s gold in that black mass
Out of the black mass of material extracted from lithium-ion batteries Li-Cyle will “produce thousands of tons of nickel, cobalt and lithium to bring back into the market.”
The idea is to re-refine the recovered materials into a battery-grade raw material that can be sold back to battery manufacturers, thus completing the circle in a circular economy approach.

Li-Cycle sees a lot of value in the nickel, cobalt and lithium that they recycle. “Demand for these critical materials is seen as a bottleneck to the EV growth.” Indeed shortages are already surfacing.
In other words automakers who have pledged $300 billion towards the development of 700 new models of electric cars, mostly by 2025, need a secure supply of those raw materials.
Li-Cycle will make money on waste management through tipping fees, by taking this specialized waste off companies hands and dealing with it.
Secure supply for soaring EV market
But in the long run Phalpher says Li-Cycle’s revenue stream will be fueled by selling these valuable commodities back into the battery market.
The company already has numerous locations in mind for local spokes (shredding facilities) in California, other places in the United States, and in China and Asia.
Phalpher says the next big step is completing construction of their hub facility in New York.
“It’ll be a major nickel cobalt lithium producer in North America that really completes our spoke and hub and commercializes all the technology.”
Recycling 95 per cent of the materials in lithium-ion batteries addresses one of the really big concerns people have had about electric vehicles.
Green Energy Futures CKUA Radio Podcast – Recycling Batteries