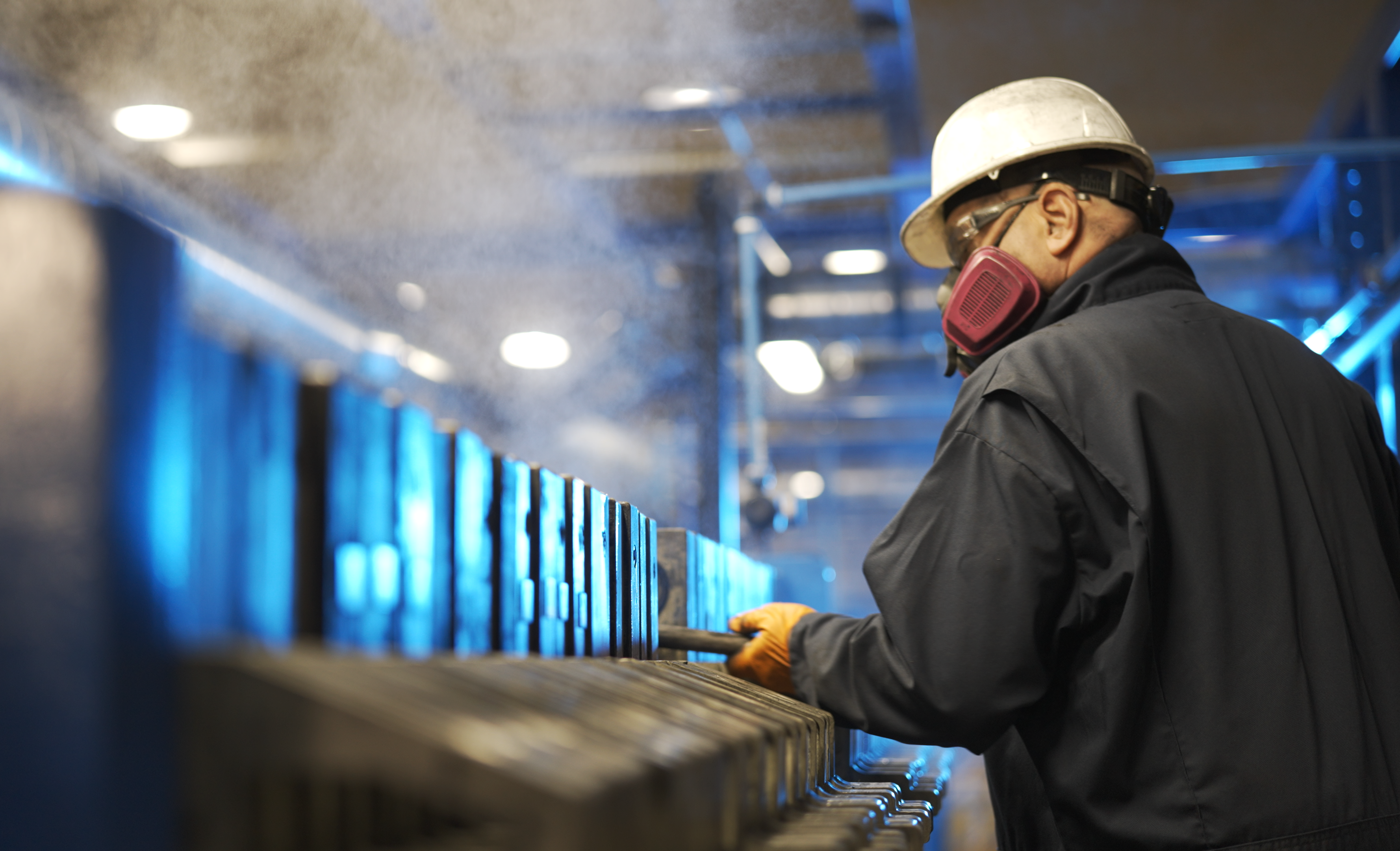
May 11, 2022
Recycling Makes Lithium-Ion Batteries The IT Technology
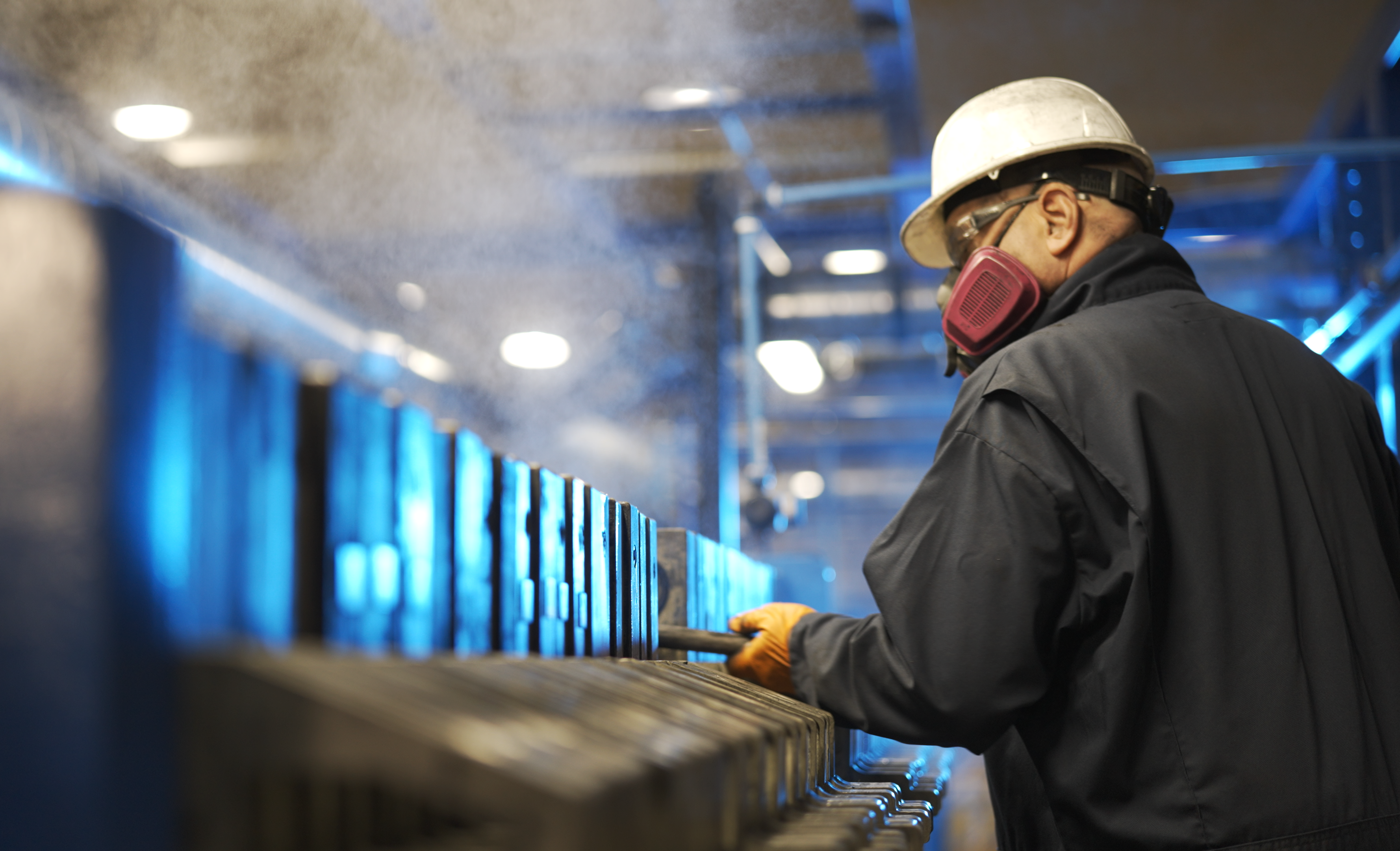
May 11, 2022
Original article published in Forbes
Lithium-ion batteries are the cornerstone of the New Energy Economy — driving the growth of electrification and decarbonization. Indeed, they are central to everything from cell phones to electric vehicles to grid storage.
But the value of such devices lies beneath the surface — made up of raw materials that are now trapped in a supply chain maze or come from unfriendly nations. Luckily, the recycling of those raw materials is becoming economically viable. Moreover, the quality of the reprocessed minerals can be as good as “virgin” supplies that are extracted from the Earth. However, mining will have to coexist alongside recycling until those scraps reach scale.
“We break down the batteries and extract critical materials. We refine those materials to produce chemicals that go back into batteries,” says Tim Johnston, co-founder and executive of Li-Cycle Holding Corp., in a chat with this writer.
“Those chemicals are the same as any mined materials: they are broken down to a molecular level, the metals are dissolved, and we rebuild them,” he adds. “We can recover up to 95% of all the materials in the lithium battery and return them to new batteries or to the economy. This is a net environmental benefit relative to mining these materials. Going to one source to process the materials is more efficient than the supply chain. There are fewer emissions, less water usage, and less soil displacement.”
The market potential for Lithium-ion batteries remains enormous. Market research firm Valuates says that the global lithium-ion battery potential was valued at $36.7 billion in 2019. But this figure is projected to hit $129.3 billion by 2027 — a compound annual growth rate of 18% between 2020 and 2027. Statista adds that the recycling market for such batteries could grow 10-fold over the next decade.
Electric vehicles will be a significant market. The European Union is phasing out the internal combustion engine by 2040, while this country wants half of all vehicles to run on electricity by 2030.
Lithium-ion batteries use five critical raw materials: lithium, nickel, cobalt, manganese, and graphite. They also use aluminum and copper. But the minerals can come from nations hostile to the United States or those with poor records tied to child labor. Russia, for example, is a leading supplier of nickel. And the Congo is a primary provider of cobalt — a country with poor labor practices.
The Circular Economy
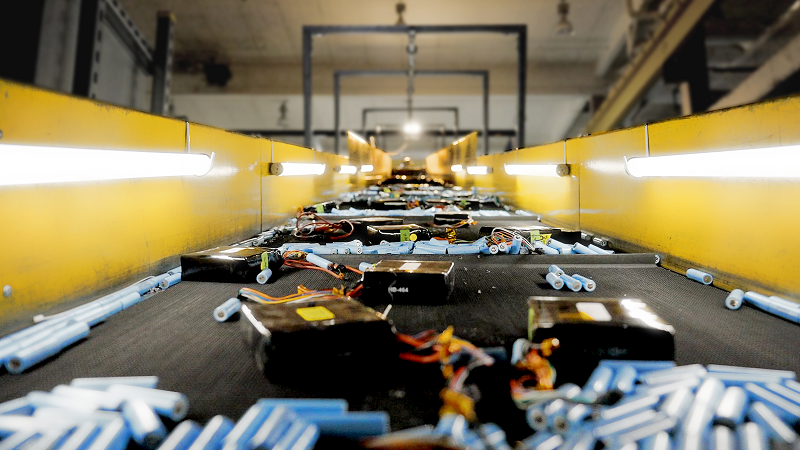
Li-Cycle says that it gets its materials from entities with ethical business operations. Consider its relationship to Glencorp, one of the largest natural resource companies in the world: Glencore will supply Li-Cycle with all types of manufacturing scrap and end-of-life lithium-ion batteries.
“This is a key step in establishing a strong long-term foundation for the vertical integration of the battery materials supply chain,” says Kunal Sinha, head of recycling at Glencore. “Together, we will be expanding the spectrum of battery material supply solutions to a broader global customer base, particularly in Europe and North America.”
LG Energy Solution, Ltd. and LG Chem, Ltd. — part of LG Corp. — have partnered with Li-Cycle. The two LGs will supply the battery recycler with lithium-ion battery scrap. Meanwhile, Li-Cycle has a similar deal with General Motors GM +1.1% and LG Energy Solution, which have formed a unit called Ultium Cells. It’s a mouthful. But the gist of it is that Li-Cycle will recycle 100% of the scrap generated by battery cell manufacturing at Ultium’s Ohio plant.
In all those cases, Li-Cycle recovers the raw materials contained in the scrap, transforming them into valuable products and contributing to the circular economy — the idea that nothing is wasted and everything is reused. Indeed, when measured against mining and importing, the business case for recycling gets even stronger: extraction and shipping result in greenhouse gases. And that does not include the lingering supply chain disruptions caused by COVID19.
The United States is regarded for its added value — computer chips and artificial intelligence. Stringent regulations make it nearly impossible for this country to catch up with the current exporters of raw materials. China mines 63% of all such minerals. But it controls 85% of the processing — the step made to separate the 17 minerals from the rare earth rock. The United States still produces 38,000 tons. But that is sent to China for processing.
“GM’s zero-waste initiative aims to divert more than 90% of its manufacturing waste from landfills and incineration globally by 2025,” says Ken Morris, vice president of electric vehicles. “Now, we’re going to work closely with Ultium Cells and Li-Cycle to help the industry get even better use out of the materials.”
Peek Under the Hood
Tesla may be a harbinger of things to come. It expects to sell 20 million electric vehicles by 2030 — a company that thinks it can recover 92% of a battery’s materials. While fossil fuels are extracted and used once, recycling allows the raw materials to have an afterlife. And Tesla TSLA +1.6% says that recycling cost much less than purchasing those minerals to build new batteries.
What’s the price differential between mining raw materials and recycling those same minerals? For now, there’s a co-dependence. Battery growth is such that mined materials are still essential. But as electric vehicles age, those devices will need to be replaced. And harnessing the raw materials from scrap products will take time.
As to which one is cheaper is a tricky question. That’s because the recycling and reprocessing technologies can vary. But Li-Cycle says that recycling is competitive — if not cheaper. Think of it this way: lithium-ion batteries use 17 raw materials that do not exist in one place. Each must be mined before it is shipped and placed in a device. Conversely, a battery to be recycled has all of those minerals in one place.
“As we scale, we can be higher revenue and lower cost-based source,” says Ajay Kochhar, Li-Cycle Co-Founder and Chief Executive Officer, in a conversation. “But we need to scale. We will not have to rely on shaky supply chains. For now, we need to get those materials in greater quantities from virgin sources and recycle as much as we can. It will take time for recycling to make up most of the demand. The recycling of materials must be efficient to be as beneficial.”
The bottom line is that lithium-ion batteries are used chiefly for transportation and grid storage — things that reduce fossil fuel usage. The storage devices will get better and cheaper. But just as importantly, their reach will expand and help decarbonize the economy.
If one peeks under the hood to see what’s inside those batteries is a rarity, they will learn that the raw materials are dirty to mine and expensive to ship — an exercise that encourages the case for recycling. Indeed, that’s a healthier pursuit that will make it easier for electric vehicles to merge into the global economy.