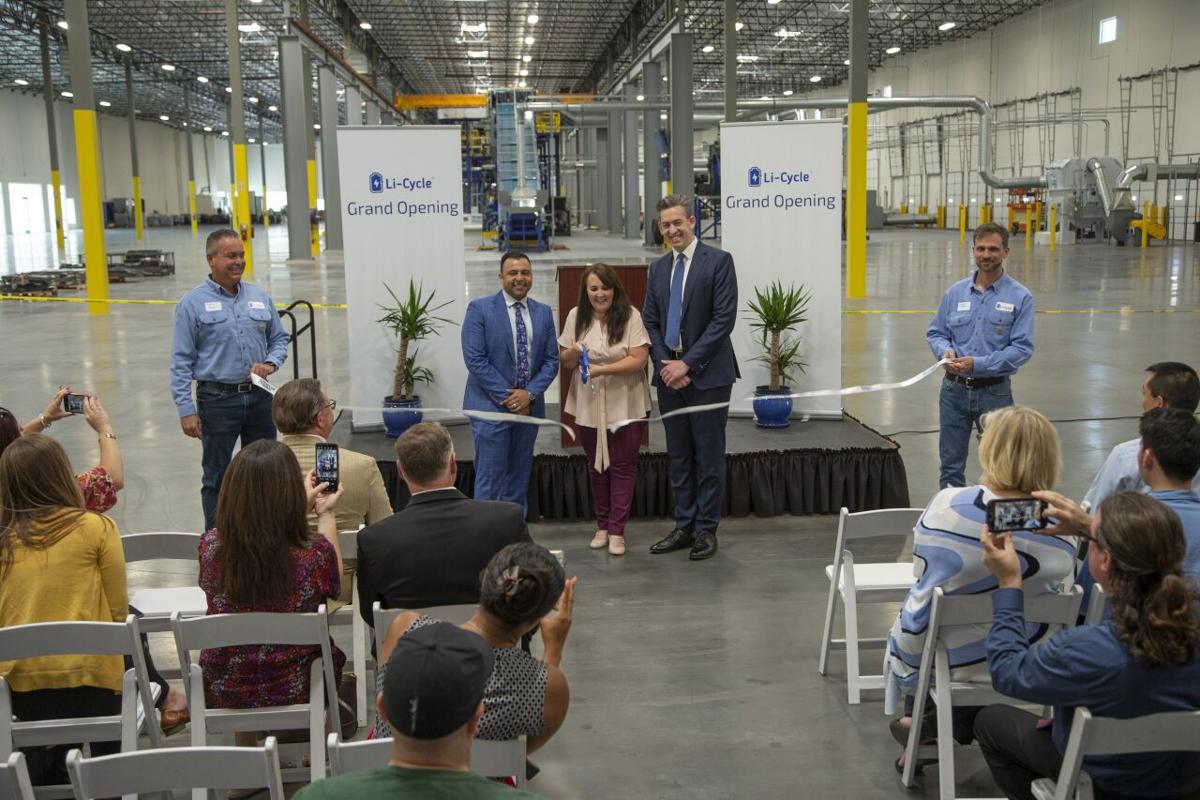
May 11, 2022
Lithium battery recycler opens Gilbert plant
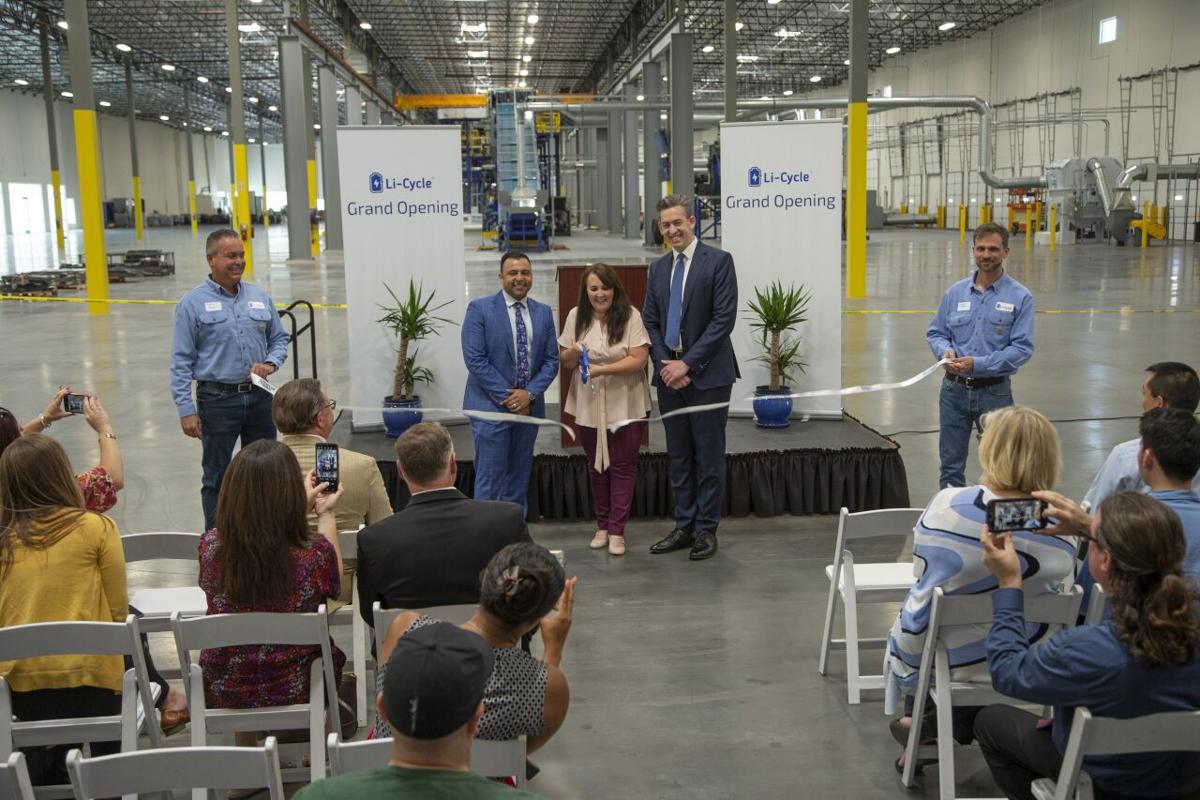
May 11, 2022
Original article published in Gilbert Sun News
A self-proclaimed state-of-the-art facility that recycles lithium-ion batteries has opened for business at Gilbert Gateway Commerce Park.
Li-Cycle, a Canadian company, held a grand opening May 3 at the facility near Power Road and Loop 202. Lithium batteries power consumer electronics such as cell phones, laptops and electric vehicles
According to the company, the facility is the largest commercial scale lithium-ion battery recycling operation to commence operations in Arizona to-date.
And that begs the question of how safe is the facility given the recent 9-day smoldering fire inside a battery-storage facility in Chandler.
It was that city’s first major lithium-ion battery fire, which Chandler firefighters let smolder for over a week due to their inexperience with handling these types of fires.
But Gilbert Fire says it has the expertise needed should a fire break out at Li-Cycle.
“Gilbert Fire & Rescue Department is home to one of the premier hazardous material response teams in the region,” fire spokeswoman Jennifer Snyder said in an email. “This HazMat team includes Special Operations Capt. Brent Bandura, who is one of two battery energy storage systems subject matter experts in the Valley.”
Snyder said the department has toured both the Li-Cycle recycling building and its storage facility multiple times and has developed a response to emergency situations in these facilities.
“With the current building suppression systems in place, the immediate response from GFRD, and the subsequent involvement of our HazMat Team, GFRD is well-prepared to deal with fires involving Battery Energy Storage Systems,” Snyder said.
A Li-Cycle spokesperson released a statement stressing that the safety of its employees and the public is the company’s top priority.
“Our Spoke facility in Gilbert and warehouse in Mesa comply with local, state and federal safety, environmental, and operational regulations and procedures,” the statement read. “Li-Cycle has also deployed its proprietary safe storage and handling procedures for lithium-ion batteries to minimize risks at our operations.”
The company’s Gilbert operation is housed in a 138,970-square-foot building on a 28-acre site zoned for light industrial.
Li-Cycle first announced in April 2021 that it was looking at Gilbert for its third commercial lithium-ion battery recycling facility. Its two other locations are in Rochester, New York and Kingston, Ontario.
At the time, it was announced that the $10-million Gilbert facility will create 40-plus jobs ranging from operations to management staff. The company also made a 10-year minimum commitment to stay in Town.
Dubbed “Spoke 3,” the facility has the capability of processing up to 10,000 metric tons of spent batteries and battery manufacturing scrap per year, doubling Li-Cycle’s current capacity, according to the company. The Gilbert facility also will directly process full-electric vehicle packs without any dismantling.
The discarded batteries and scrap are shredded into what’s known as black mass, a powder substance that contains a variety of metals, including lithium, cobalt and nickel.
The black mass then goes to Li-Cycle’s North American Hub for further processing into materials that are used to make new batteries.
According to the company, 50 percent of the battery waste source today comes from consumer electronics, followed by manufacturing scrap at 29 percent, auto original equipment manufacturer at 16 percent and energy storage systems, 5 percent.
By 2025, manufacturing scrap is anticipated to make up 68 percent of the source for battery waste, followed by auto OEMs, 25 percent; consumer electronics, 5 percent and energy storage systems, 2 percent.
The need to recycle Li-ion batteries has increased especially with more electric vehicles coming on the roads, according to Li-Cycle.
According to the company, electric vehicle batteries can either be reused or dismantled, and the lithium-ion in them repurposed for things like solar electricity generating batteries.
Li-Cycle claimed it has reinvented the recycling process by developing and validating a patented technology that enables recoveries of at least 95 percent of all materials found in Li-ion batteries through a zero-waste process, allowing it to fill a growing supply-chain need.
The industry norm is less than 50-percent recovery, according to Li-Cycle.
Also, Li-Cycle is unlike other recyclers that use lots of heat and wasted energy, but because it’s proprietary, not much can be disclosed about the company’s processing, a company representative has said.
The company also said the facility won’t produce odors because it won’t be discharging industrial wastewater, which is typically associated with smells.
Li-Cycle said it chose Gilbert because it is strategically located for the western-U.S. battery recycling hub, as well as being at the nexus of where there will be continued growth in the quantity of lithium-ion batteries available for recycling.
Li-Cycle was founded in 2016 and has over a dozen spokes located in Europe, China and Asia-Pacific countries. It touts it is currently the largest recycler of lithium-ion batteries in North America.
By 2025, the Toronto-based company anticipated a total of 20 operating spokes in North America, processing 100,000 metric tons a year and four total operating hubs.
According to Li-Cycle, its end products are “future proofed – providing the building blocks of batteries that are not at risk of technological obsolescence.”
And, reusing and recycling Li-ion batteries helps conserve natural resources by reducing the need for virgin materials and reducing the energy and pollution associated with making new products, according to the U.S. Environmental Protection Agency.