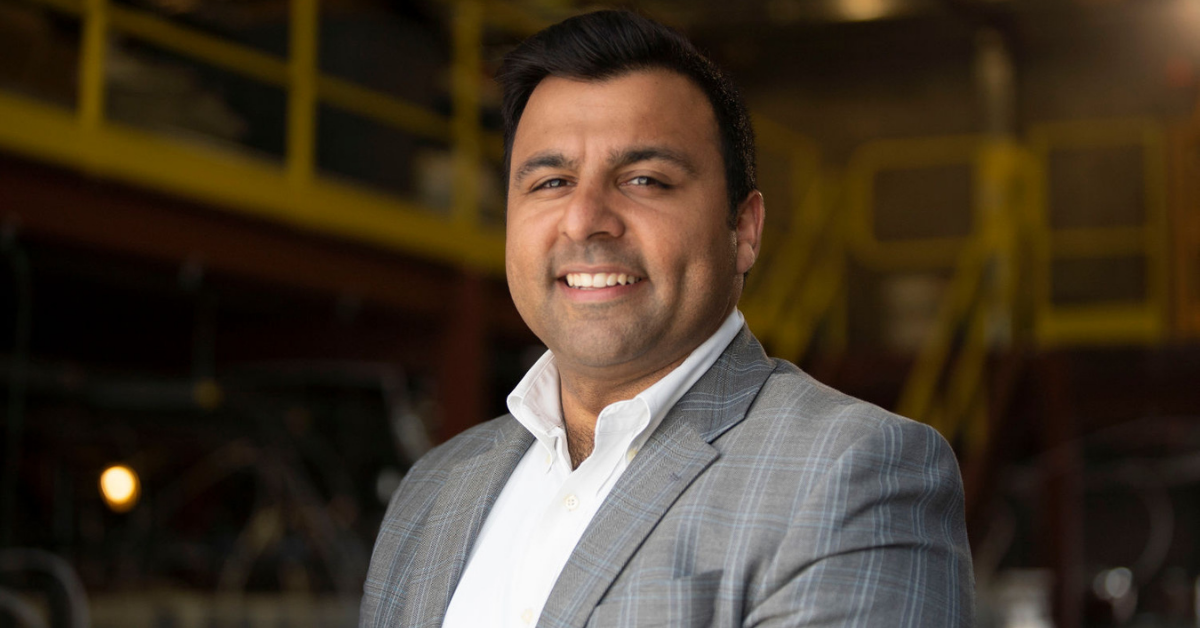
August 28, 2020
Li-Cycle recovers usable battery-grade materials from shredded Li-ion batteries
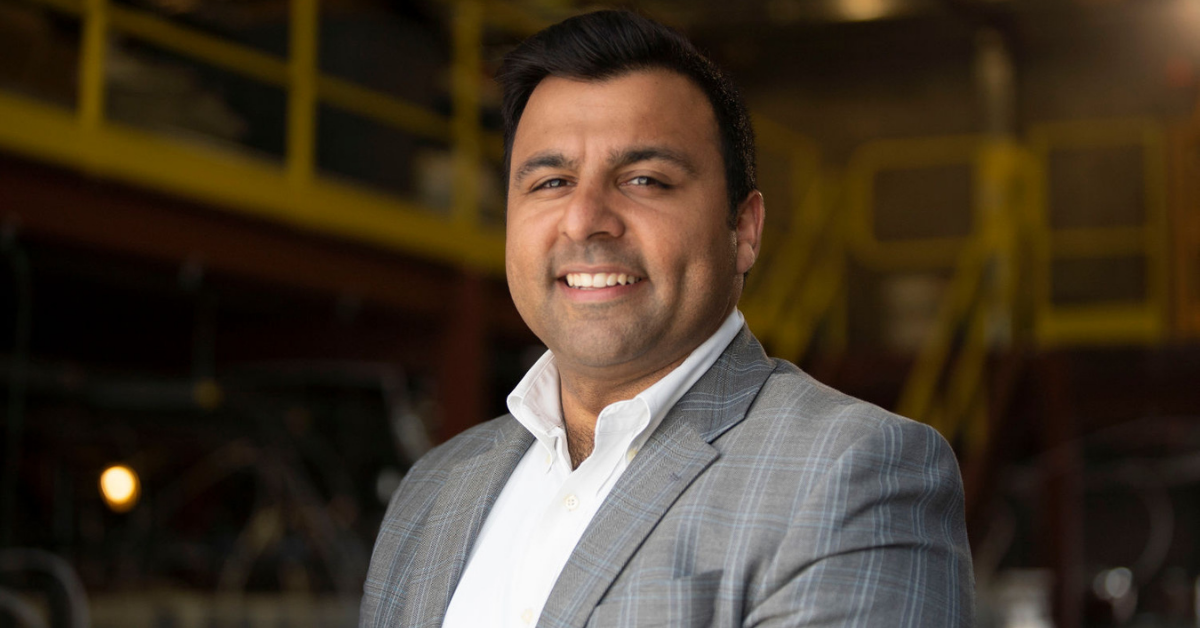
Original article published in CHARGED Electric Vehicles Magazine
August 24, 2020 – Charles Morris
Q&A with CEO Ajay Kochhar
It’s usually one of the first objections cited by EV naysayers: batteries can’t or won’t be recycled, and they contain hazardous materials that will end up in landfills. In fact, no such sinister scenario is likely—most of the components of Li-ion batteries are valuable, and it’s quite feasible, technically and economically, to recycle them. Several auto OEMs, research institutes and other industry players around the world are developing systems to do just that.
However, it is fair to say that it’s early days for battery recycling, and that there is much work to do to build a recycling regimen that will be able to handle the volume once substantial numbers of vehicles are electrified. Charged spoke with Li-Cycle’s Co-Founder, President and CEO, Ajay Kochhar, who explained what his company is doing to build a sustainable battery recycling ecosystem.
Ajay Kochhar, a chemical engineer, and Tim Johnson, a mechanical engineer and Chartered Financial Analyst, founded Li-Cycle (pronounced LIE-cycle) in 2016. “We come from the lithium industry,” Kochhar told Charged. “We used to work for companies that produced lithium chemicals that go into cathodes, cells and, ultimately, battery packs. Way at the other end of the supply chain—mining and refining, particularly the refining piece.”
Kochhar chatted with Charged about the company’s history, its unique system for collecting and processing materials, and the future of the battery recycling ecosystem.
Charged: What inspired you to start Li-Cycle?
Ajay Kochhar: We were leading a practice, a consultancy, essentially consulting with companies to build large chemical plants. And we’d be asked as lithium consultants and experts to look into these looming questions: “How environmentally friendly are batteries? And what’s going to happen to all these batteries?” It was very opaque, hard to figure out what was happening. Sometimes you can’t even figure out who is dealing with the batteries. So, we didn’t find very satisfying answers.
It’s all about critical material supply—supply of lithium and nickel and cobalt to go back into batteries. We’d be asked, what’s actually happening to all these batteries, at end of life? Is there really some sort of recovery of these materials to go back into batteries? And again—this is now four or five years ago—it was very opaque, unclear. Most of the time we concluded, for some materials like lithium, there really wasn’t any recycling happening to process that material back into lithium-ion batteries.
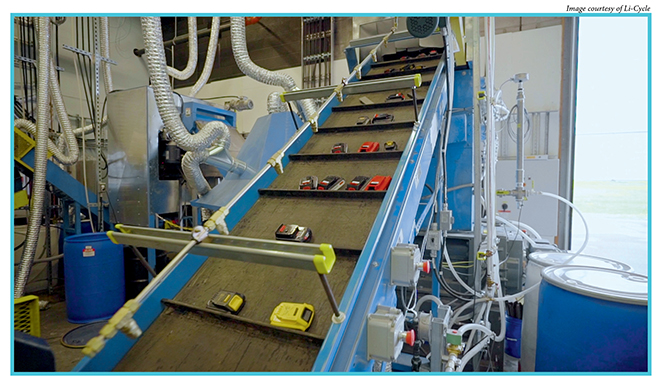
Charged: So, all of the batteries used in laptops and phones, there’s not been much material recovery?
Ajay Kochhar: No, not so much has been recovered. I’d say the general approach has been reuse. It’s typically either mom-and-pops or individuals that are—in the case of laptop batteries—taking them apart, and selling the cells. There’s a lot of that that happens.
Or, if it’s large quantities, it usually is a waste approach. You have these generalized “recyclers” that deal with those batteries. They often thermally treat them—they’re burning off plastic and electrolyte in the batteries and are not really focused on the material recovery. It’s mainly the cobalt, the nickel and the copper that they can get via that method, but that’s usually it. Lithium is burned off, or it goes into a waste fraction. Other components, like plastics, electrolytes, graphite, they’re all essentially burned off, typically. It’s not usually overtly apparent—you have to dig in and understand. Our team has been to a lot of these facilities, and that’s usually the case—it’s usually a waste approach, not resource recovery, and not very efficient.
Charged: So, you guys came along to fix that.
Ajay Kochhar: Exactly. We launched the company in 2016, after a couple of years of intense R&D. Instead of a thermal process, what we do is a mechanical and chemical process. It’s two steps. Both are patented, owned by the company. We handle all types of lithium-ion batteries, from laptop and cellphone batteries all the way up to EV batteries. There’s not a large quantity of end-of-life EV batteries yet, but we’re starting to see some here and there.
In the first step, we basically size-reduce the batteries. It’s a shredding process, which may not sound that spectacular, but it’s really all about safety—how do you do that without risk of fire or a thermal event?
In the second step, we take those physically separated materials, and we reprocess that intermediate material to recover battery-grade end chemicals—lithium, nickel, cobalt—that are suitable to go back into cathodes again. Overall, it’s 95% recovery, and the materials that we make are equivalent grade, if not better, to mined and refined materials, and very competitive in terms of price with virgin materials.
At a high level, this is very different from what’s been happening in the industry to date. Materials don’t actually go back to the lithium-ion battery supply chain, they go to some other lower-quality use, typically. So, ours is a completely different approach.
We’ve had a couple of years of R&D, and now we’re in the commercial operations and building phase.
Charged: Would you say this is analogous to the process for recycling lead-acid batteries, in which they reuse the materials?
Ajay Kochhar: Yeah, that’s where we’re trying to get to. Lithium-ion is quite a bit more complex, obviously, than lead-acid. With lead-acid, you have a few different types, but on the whole it’s pretty homogenous. The complication with lithium-ion—and this is why there’s the need for innovation—is that there are so many different types. It keeps on getting innovated, keeps on changing year-on-year. You have different chemistries, different flavors, different form factors. It doesn’t end. So, that’s the challenge. How do you get a process that’s agnostic, and at the same time is going to be economic no matter what, on a mixed basis? That’s been our mantra from the start—to ensure that you can take any lithium-ion battery in a mixed fashion and ensure it’s scalable. And now, we’re operating at commercial scale and on the verge of expanding internationally.
Charged: You said step one is to safely shred the batteries. Can you tell me a little bit about how you do that safely? Do you fully discharge them?
Ajay Kochhar: It’s a Hub-and-Spoke model, like a wheel. The Spokes are the decentralized satellite sites that do the shredding, and the Hub is the refining, the chemical process.
A big problem in this industry has been logistics. If I’m an automotive company, and I have a battery I have to get rid of, if I have to pay somebody to take care of the battery, that’s a big issue. Because you have to pay quite a bit to ship these heavy batteries any distance. So, the solution to that is our Spokes. We get close to the source. Modular, scalable plants, low-footprint, almost “Lego-built” facilities. That’s how we set it up for them, regionally deploying these sites to get batteries close to the source, convert into not-a-battery and then ship that intermediate material, which is now safe, can’t catch fire, and is cheaper and easier to ship in bulk.
Charged: I know there’s a lot of regulations around shipping lithium-ion, so this gets you around that, I imagine.
Ajay Kochhar: It does. So, how to deal with this safely? We’re essentially shredding in such a way that there’s no access to oxygen. There’s a variety of ways to do that—we do it in a particular way, it’s patented. But from a safety standpoint, it’s not only the actual processing, but there’s a lot of standard operating procedures and health and safety requirements around storage, logistics, handling. We’ve had to develop a lot of this safety stack of approaches.
Charged: When you have a barrel of your shredded material, what is handling that like? Are there any special precautions you have to take with the shredded stuff?
Ajay Kochhar:Handling the shred products is way easier. It’s basically mixed metals—quite inert. At the Spokes you get batteries going in, any type, minimal dismantling. Mixed small and large, one stream, one process. And coming out the other end we have separated plastics, copper, aluminum. And the key fraction, which is the most valuable, is the cathode and the anode in the battery. The cathode always contains lithium, and potentially nickel, cobalt, other metals. And the anode is usually graphite.
So, that cathode/anode mixture, that’s the most valuable. All that’s inert, not a big deal to be shipping that around relative to batteries. There are some key regulatory aspects you have to ensure that are met, but way easier than batteries. That black powder is the feed to our Hub process, the refining process.
Charged: So then, at that step you use chemical processes?
Ajay Kochhar: That cathode/anode material, we recover everything in it: graphite; lithium, you recover that as a lithium chemical; cobalt, you recover that as a cobalt chemical; nickel, as a nickel chemical, and so on. There are about eight different products from our hub facility.
In the first step, it’s a lot about safety and automation. In the second step, it’s mainly about dealing with the variability. You get such a large variation of different types of lithium-ion batteries. You have types that are really high cobalt, types that are really high nickel. So, that’s the difficulty and the innovation that we’ve now had to deal with.
Around the world you have a lot of [variation]. In China, for example, you have a lot of refineries that are taking this cathode/anode material and recovering cobalt and nickel. But the interesting thing is that they don’t usually recover lithium. There is basically no commercial, battery-grade, lithium chemical recovery from any facility around the world. You have a lot of people that are doing bench-scale work, pilot work. But the reality is, in the market there’s no one who’s actually getting the lithium out of a lithium-ion battery, which is very ironic.
We do. We actually get the lithium, in a battery grade, out of lithium-ion batteries. And I think we’re the only facility in the world that can do that. So, it’s another key differentiator of what we’re doing.
Charged: Is that just due to the market cost of lithium?
Ajay Kochhar: I think it’s two things. If you rewind about 10 years, lithium prices were way lower than they are today. So that’s probably part of it. I think the second is that this industry is on the precipice of turning from a niche business with low volumes into one that’s going to have quite high volumes in the future. It’s going to take some time to get there, but if you still have these old, inefficient, generalized processes, you’re losing out on a lot of the material in those batteries that can be recovered.
Charged: When a battery dies or loses capacity, it’s largely due to side chemical reactions that are unwanted and build-up or damage to the interfaces of the electrodes, etc. But all the originally materials are still present, so your process separates those and starts from scratch, correct?
Ajay Kochhar: Yes, exactly. The way the batteries usually die is through these side, or parasitic, reactions. And usually it’s a physical change or morphological change within the battery. There’s a number of ways that batteries can die, but commonly you have, call it lithium inventory, it ends up in parts of the battery that it shouldn’t be, it gets locked up in these side products, so you lose the ion, which is basically the thing shuttling back and forth to create the charge. Over time, the inventory of that changes. That’s actually the most common way that the battery dies. So, you lose your capacity because the “runner” got stuck somewhere, or a few of the “runners” got stuck in some other places and now you can’t use them to create electrical charge.
It’s a location or a form change that’s happened in the actual physical form. We go back to the fundamental building blocks. The actual lithium is still there, it’s just in a different form. We’re basically going back to the fundamental atoms, then we’re rebuilding those chemicals that are reused in a lithium-ion battery.
Charged: You’re entering a new phase now, into a commercial process. Can you tell me where you are now and where you’re headed next?
Ajay Kochhar: Right now, we’re the largest recycler of lithium-ion batteries in North America. In pretty quick order that’s become the case. We have an existing facility in Ontario, which grew out of our R&D center and is now a commercial facility—North America Commercial Spoke 1. And we have a second facility (North America Commercial Spoke 2) that we’re building in Rochester, New York in the old Eastman Kodak business park, which has now turned into a hub of activity for cleantech, which will be live later in 2020.
Where we’re going is twofold: we’ll continue to grow in North America. And, outside North America, what we’re doing is partnering up via joint ventures. Our philosophy behind that is that this is a very regional market, the nuances are very regional, regulations are very regional. In every region of the world it’s going to have a different approach, so you really do need regional partners to help you get to speed at scale.
Charged: In terms of a business model, are you buying the used batteries, or are they paying you to process them?
Ajay Kochhar: It really depends on the type of battery, and the region around the world. In some regions there’s a norm that groups pay for batteries and in other regions it’s the norm that it’s a service. Within that there’s variability, because some batteries have a lot of valuable materials, and some don’t. But from a high level, if you talk to any vehicle manufacturer, anybody that has batteries that will need to be recycled in the future, what they want is for this not to be a liability. They want it to be either zero-cost or even, ideally, a value. That’s why we started this company, in large part, was a customer need. It’s basically folks saying, “Why are we paying for this? Isn’t there a lot of valuable material in here? Why hasn’t there been an innovation to solve this?”
As the scale gets there in the next five to ten years, we believe we can transform that norm and make it clearer. Is this a cost? Is it net zero? It’s a bit immature today, but in the medium and long term, our objective is to change that into a clear economic position.
Charged: Are you currently selling the raw materials on the open market?
Ajay Kochhar: We actually do commercially sell a lot of our materials back to the market today. It is a very rigorous process to qualify the material, convince people of its quality. Usually, you start with a small sample and then you get to a medium-size sample and then a larger sample, and that’s the thing that basically leads, ultimately, to a contract. That takes a long time. And we’ve progressed to that for a lot of the materials that we produce. We’re delivering materials under contract to groups that make battery materials that go back into batteries again.
Where I’d love to see us go in the next, say, three to five years—and this isn’t quite there yet in the market—is the circular economy model. Say you get battery materials from a certain manufacturer and you recover the materials out of that, then you integrate that right back into the same manufacturer’s supply chain or a few suppliers’ supply chains. We’re getting there, we can definitely enable that, but that’s going to be a medium-term reality.
Charged: In terms of the quality of the materials that are the product, in most cases it’s identical to the virgin material? How do you quantify that for people for graphite, for example?
Ajay Kochhar: Yes. There are a variety of nuances as it relates to the quality of lithium and nickel and cobalt. And in graphite, for example, these are almost tailored, specialty chemicals. You have a specific customer, they’re going to want a little bit less of this and a little bit more of that, etc. There’s a generalized specification that you can work to, but the reality is that when you actually engage with specific groups they’ll say, “Actually, we want a little bit less of that.” And, “Oh, that’s too high.” We’re talking about levels of parts per million—very, very small levels of materials. So, we’ve gone through that qualification with a variety of groups for lithium and nickel and cobalt.
We make lithium carbonate and nickel sulfate and cobalt sulfate. That’s gone very well, and it just takes iteration. Being in the market, having materials to market, iterating the physical properties of that specification, etc.
Lithium, for example, that goes to a cathode manufacturer, it has to meet a certain spec. There are certain impurity sensitivities, and you have to be below those thresholds. So, we supply to meet that spec and then they would use that lithium in making a new cathode. That’s one example where it integrates back into the supply chain.
There are, however, parts of the battery where it’s tougher and it’s going to cost a lot and maybe it’s not worth it, or there are difficulties, and graphite is one of those examples. So, we make the graphite, say technical grade or concentrate material, that can go back to other applications of graphite, like electrodes or pencils, whatever it might be. But graphite is very sensitive. It’s down to the physical properties of it. You have different types of graphite—synthetic, natural. We are getting the complete mix of all that. In one stream, we get synthetic, mixed, this size, that size, etc.
So in theory, yes, you could go back to a graphite battery-grade product, sure. But there’s some strategic decisions where we’ve looked at it and tried a variety of things, and we just said, “No. There’s not as much net value.”
It’s a big step up not to be burning graphite, which has been the norm to date. We’re giving back to the economy, that’s important. But there are some technical realities. You can’t be taking this mixed feed in and getting a perfect graphite product. There’s some situations where we are trading back into the battery supply chain, and there’s others where it’s more difficult and the priority is to get it back to the economy through other markets.
Charged: There are regulations that mandate the amount of lead-acid batteries that have to be recycled. Do you see that becoming the norm for lithium-ion as well?
Ajay Kochhar: Yes. If you had asked me about maybe 12 months ago, I think it was much more unclear. But we’ve seen a lot of movement, even in the last year, from jurisdictions such as China, Europe, certain states in the US, provinces in Canada. There’s an emerging theme of two things. One is, there is an emerging priority of who is responsible for the battery at end of life. And that’s been a big question. Who is going to deal with this and who’s responsible? In the case of China, it’s been made very clear that it is the automotive manufacturer that is responsible for the battery’s end of life.
Second, it’s about recovery. Typically, if you have regulations on recycling, they do mandate some level of recovery. For example, in Europe to date, the mandated recovery for lithium-ion batteries has been 50%. But there is an upcoming renewal of that regulatory framework that will likely push that number up. And that’s the same theme around the world. We see a lot of different regulations that are stipulating recoveries that are way above 50%, typically 70%, 80%, even 85% plus. And that’s really interesting because on the one hand, as a recycler that can achieve that, that’s great. That’s locking in a lot of acceleration for us. However, we have to be a bit careful about the staging. In some parts of the world that solution may be available, in other parts not. And so, I think that’s typically the place that the automotive companies are trying to plug in and make sure that it’s not being introduced prematurely. That it’s being staged in the right way so that the solutions are available in the market to meet those requirements.
Charged: What about the copper and aluminum and the plastics? Is that stuff easily mechanically separated out in the grinding phase?
Ajay Kochhar: Exactly. It’s all automated, we use physical properties to separate that out, no thermal processing, we don’t burn anything off. Then we put them into the standard copper, aluminum, plastic recycling supply chain.
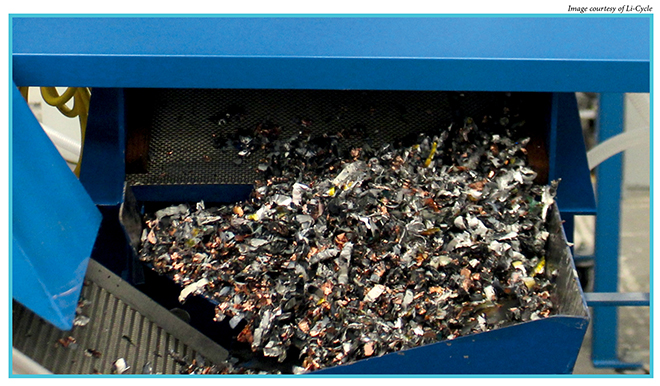
Charged: What are the next steps for you? Are you guys looking for customers? Are you looking for partners? If someone in China or Europe wanted to license your technology, would you do that?
Ajay Kochhar: Generally speaking, yes, that’s what we’re doing. The intent is not maybe so much via licensing. I think there’s a lot of, say, younger companies in this space where that’s what their business model is. And now the reality is that, to put it very plainly, you have to do it. You have to show that what you’re doing is working at commercial scale before somebody else is going to take the risk and license it.
Just to sum up, let me say this. From a consumer perspective about EVs, I think there’s been a lot of questions about, “What are the end-of-life recycling solutions out there? Are they economically viable?” I just want to say it loud and clear: There are solutions today, and they’re here. And this “end-of-lifecycle problem” with lithium-ion batteries and EVs, it’s not a problem. It’s taken innovation to figure it out, but the reality is, it can be done. All that needs to happen is that we continue to scale up to meet the market need over time.
There are solutions there, and that’s important for not only consumers to know, but government stakeholders and OEMs themselves. The whole supply chain, the whole ecosystem, really needs to have that awareness. Because in the absence of that, there is this clear, countercurrent narrative which homes in on [the lack of sustainable and economic recycling solutions for lithium-ion batteries], and it’s actually wrong.
Charged: You hear a similar thing with the long tailpipe argument. People say, “You know, these things are fueled by coal.” And, “What are we going to do with all the batteries?” is the next thing they say, and my response is, those are both solved.
Ajay Kochhar: Exactly. And they’re not solutions that will be here in the future. They’re here today.
This article appeared in Charged Issue 50 – July/August 2020