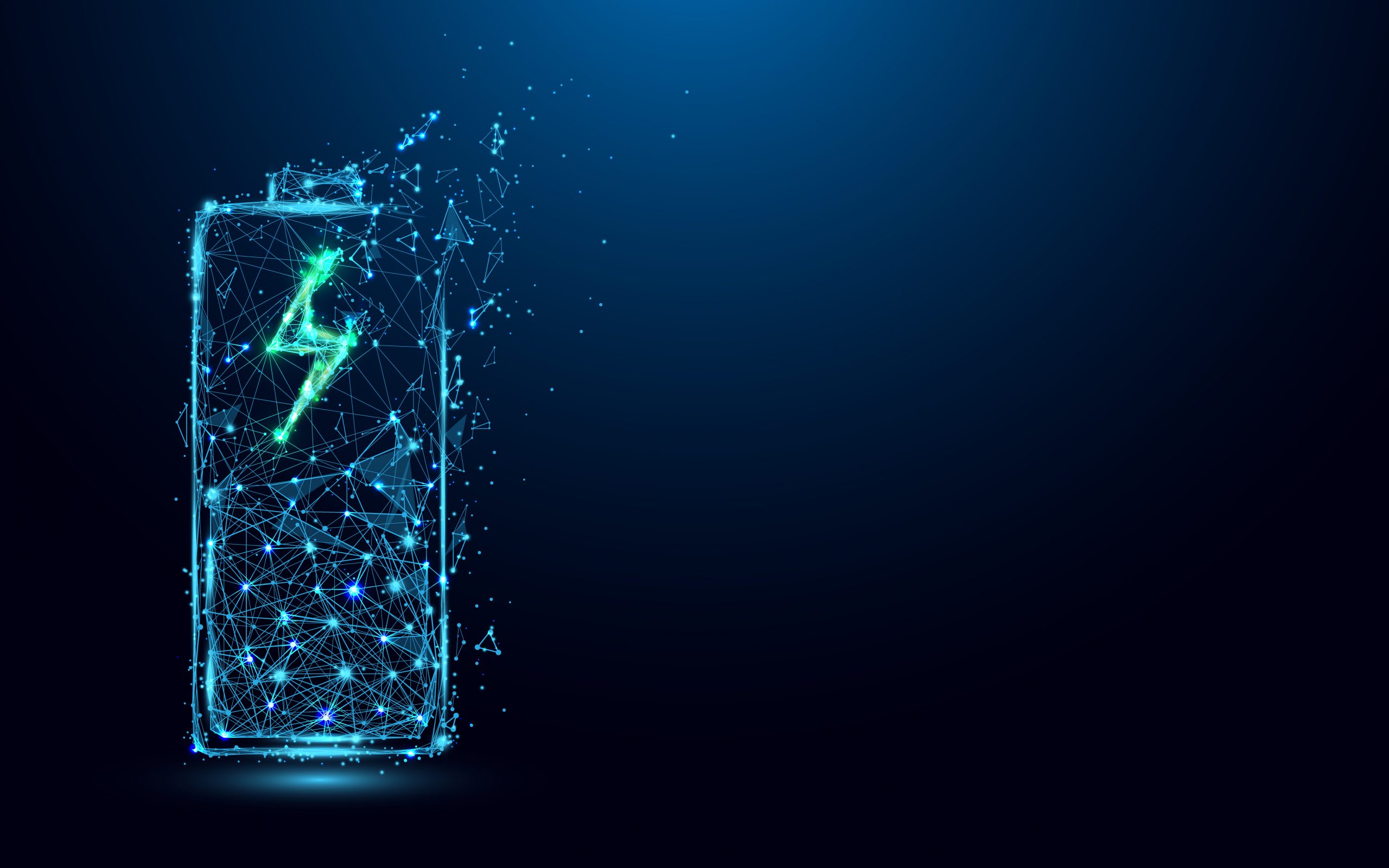
March 23, 2020
Li-Cycle delivers first commercial shipment of recycled battery material
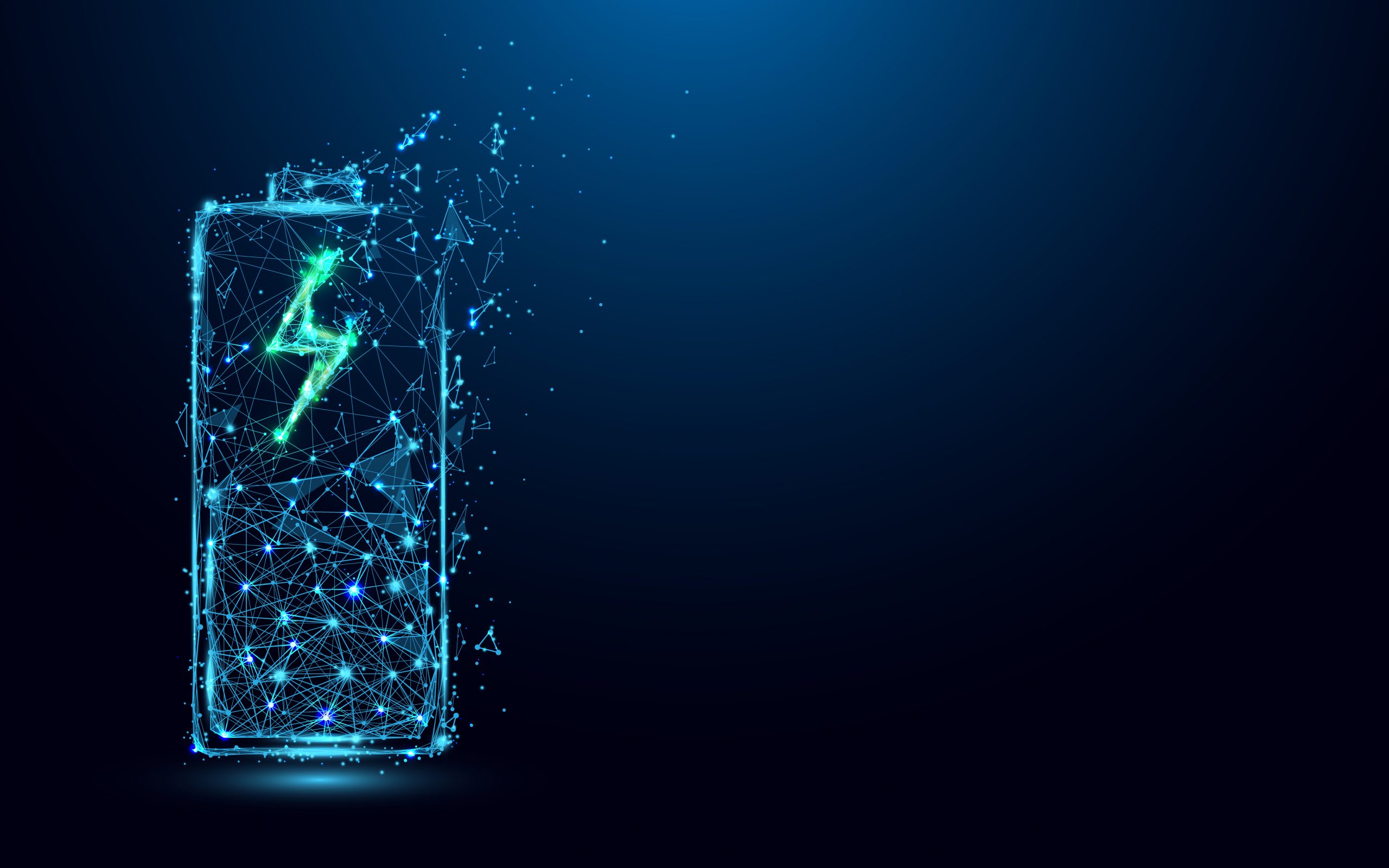
March 21. Li-Cycle Corp., a North-America-based lithium-ion battery resource recovery company, recently completed its first shipment of commercially recycled battery material, containing energy metals concentrate. (Earlier post.) The shipped product was processed at Li-Cycle’s facility in Ontario, Canada and contained key energy metals—such as cobalt, nickel and lithium—used in lithium-ion batteries.
Li-Cycle is one of the few companies globally capable of recovering critical battery materials from lithium-ion batteries in a sustainable and safe manner.
The company also announced that it will establish its first US-based facility in New York State. Li-Cycle will set up operations at Eastman Business Park (EBP) in Monroe County in an effort to tap into the robust lithium-ion battery supply chain in the United States and the lithium-ion battery ecosystem in Rochester.
Li-Cycle selected EBP for this facility after determining it as the best location for the company to provide services to its growing client base to the South and Midwest. The company has also committed to creating a minimum of 23 jobs in its first year of operation. Li-Cycle expects to be fully operational at the facility later this year.
Since Li-Cycle’s founding in 2016, the company has developed a technology that enables 80-100% recovery of all materials found in lithium-ion batteries using a two-step mechanical and hydrometallurgical/wet-chemistry process.
Li-Cycle’s process technology is capable of recycling all variants of cathode and anode chemistries within the lithium-ion spectrum, without the need for sorting into specific chemistries. Additionally, Li-Cycle’s technology ensures that lithium-ion batteries are processed safely without risk of thermal runaway (i.e. there is no risk of fire during processing).
The process technology is inherently sustainable—it produces no solid waste streams, minimal/no water discharge, nor any harmful air emissions.
By 2040, an estimated 559 million electric vehicles will be on the road worldwide. Furthermore, the capacity of global lithium-ion battery energy storage installations is projected to grow over 50 times during that same period. While lithium-ion batteries continue to play an increasingly critical role in the global transition towards electrification, the world currently lacks a viable option for dealing with the rapidly growing volumes of spent lithium-ion batteries. Li-Cycle is targeting that need.
Li-Cycle is focused on meeting the global challenge in North America through its existing processing facility in Canada and its upcoming expansion in the US during 2020. Li-Cycle is also actively pursuing international opportunities, with a vision to create a significant secondary source of critical materials for the lithium-ion battery supply chain.
Materials produced by Li-Cycle provide a significant net benefit to the environment compared to traditional production methods. Specifically, returning commercial quantities of recycled battery materials to the supply chain offsets the use of battery materials that are mined and refined from primary sources. As a result, Li-Cycle’s activities indirectly reduce the environmental (e.g. air emissions, soil and water impacts) and social impacts of mining and refining from primary sources at scale.
See the full article posted on Green Car Congress here.
About Li-Cycle
Li-Cycle Corp. (Li-Cycle) is on a mission to leverage its innovative solution to address an emerging and urgent global challenge. Lithium-ion rechargeable batteries are increasingly powering our world in automotive, industrial/utility/residential energy storage, and consumer electronic applications. The world needs improved technology and supply chain innovations to better recycle these batteries, and to meet the rapidly growing demand for critical and scarce battery-grade materials.
Li-Cycle Technology™ is a low cost, safe, environmentally friendly process that can recycle all types of lithium-ion batteries. It can do so with an unparalleled recovery rate of up to 80-100% of all materials. The Company’s industry-leading processing technologies uniquely position it to support a key element of the growing international movement towards zero carbon technologies as part of the circular economy.