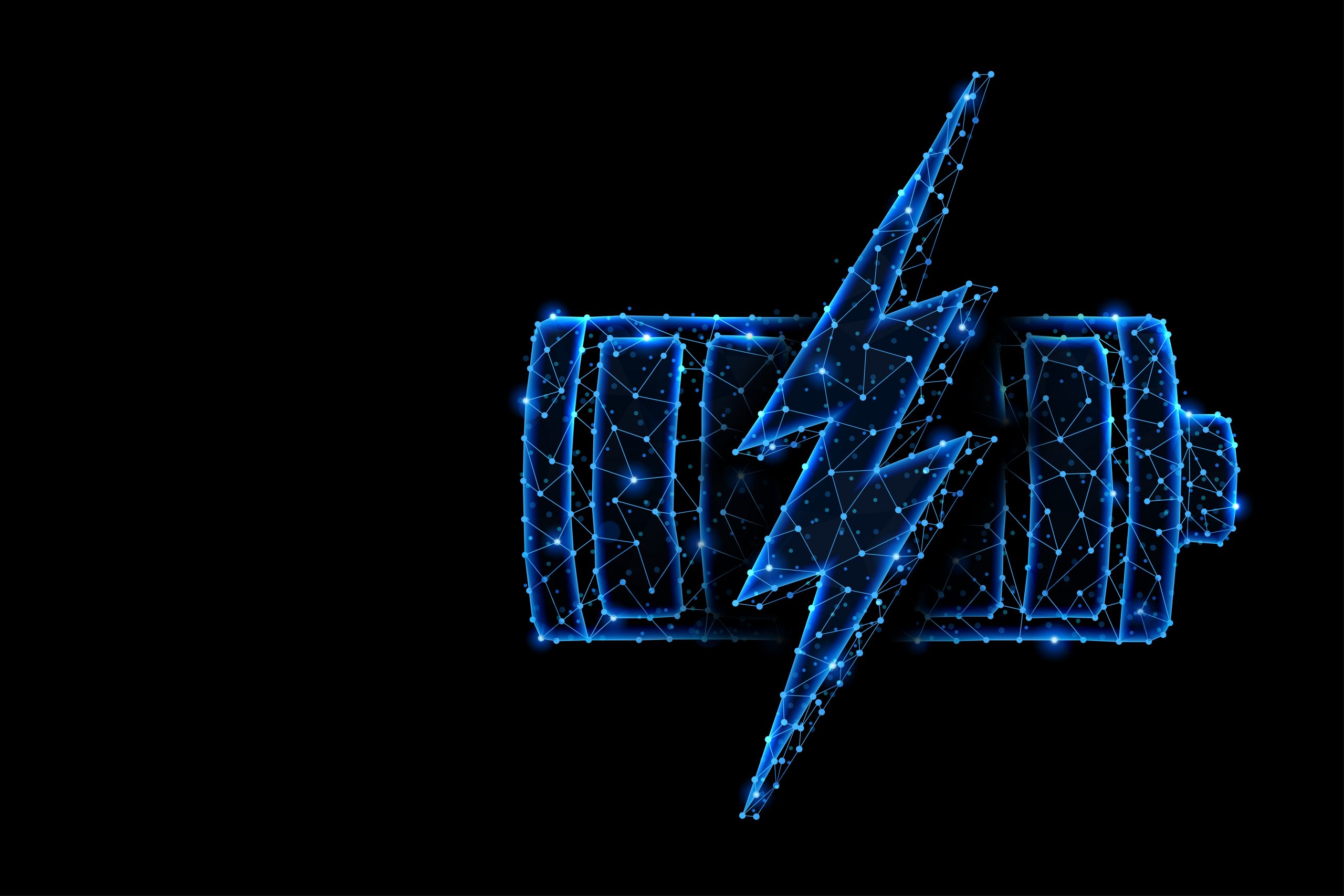
July 10, 2020
Why Resource Recovery is Critical to the Future of Clean Transportation
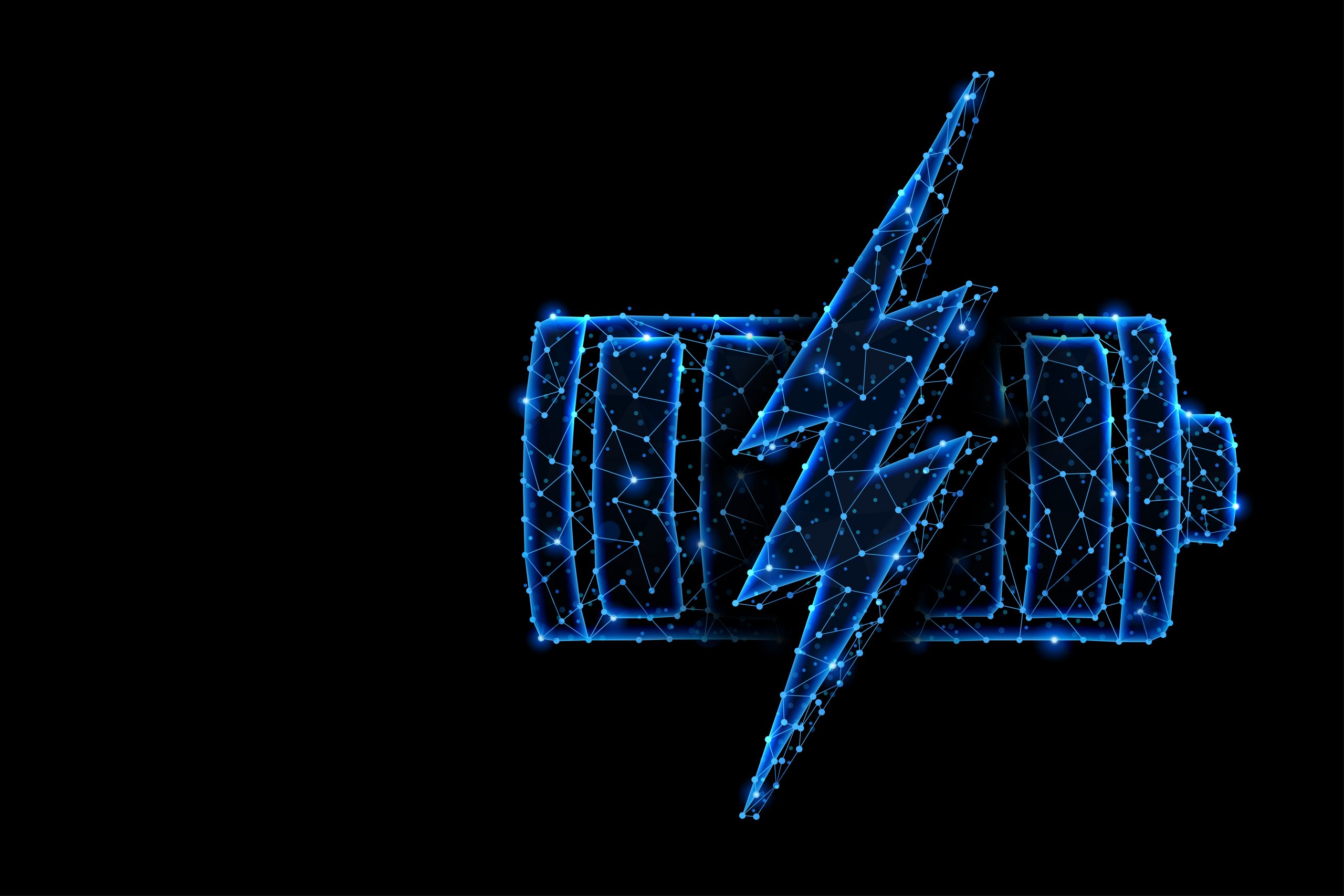
Original article published in Alt Energy Mag
Recently, a report from industry analysts stated that by the end of this year – 2020 – China alone will generate approximately 500,000 metric tons of used lithium-ion batteries and that by 2030.
June 30th, 2020 – Kunal Phalpher
The world is rapidly moving forward in the replacement of fossil fuel-powered cars, busses and other modes of transportation with clean energy sources. Fossil fuel byproducts have a detrimental impact on not only human health, but the global climate and overall environment. A significant force behind this shift has been the evolution and optimization of energy storage, in the form of lithium-ion batteries, which are efficient, stable and enable a reduction in impact on the environment thanks to the elimination of tailpipe emissions. The challenge, however, lies in how to deal with the growing number of lithium-ion batteries at the end of their lifecycle.
The urgency and size of this problem is backed up by the numbers. Recently, a report from industry analysts stated that by the end of this year – 2020 – China alone will generate approximately 500,000 metric tons of used lithium-ion batteries and that by 2030, considering the expanding popularity of electric vehicles, will reach 2 million metric tons of lithium-ion waste per year.
The environmental impacts of this growing battery demand are two-fold; the first being the physical amount of lithium-ion battery waste that could end up in landfills, potentially releasing metals into the environment like nickel, cobalt and manganese which, while not as problematic as lead, are still considered toxic heavy metals. The second focuses on the increasing demand for mining the resources necessary for the manufacture of new lithium-ion batteries has on the environment, including the release of byproducts through mining that contribute to general pollution; the pollution and depletion of groundwater; and of course, the finite nature of critical battery resources like lithium.
The social impacts of new battery production should also be considered. Cobalt is an important component of lithium-ion batteries and 50 percent of the world’s production of cobalt comes from the Democratic Republic of the Congo, which is tied to human rights abuses, illegal mining, harmful environmental practices and armed conflict.
Unfortunately, industry experts have stated that we’re unlikely to find a more environmentally conscious or economic energy storage solution for another two decades, largely due to the fact that energy storage technology advancements typically require long development lead times from concept to full-scale manufacture. With all of these aspects in mind, it’s clear to see that resource recovery is a critical element in the future of clean transportation, while lithium-ion technology remains the dominant powertrain, in order to meet the high demand for critical materials and offset some of the need for mining of new materials and redirecting batteries away from landfills.
As it stands, recycling and resource recovery of the components within lithium-ion batteries has historically been largely ineffective. Traditional methods are energy intensive, requiring the batteries to undergo a high temperature melting and extraction, or smelting, process similar to methods used in the mining industry. The plants required for this are costly to build and operate, which, despite the high costs, only recover 30-40 percent of the constituent materials, with the remainder becoming volatilized, cleaned, emitted to the atmosphere or discarded as solid waste. The challenge in resource recovery is also made more cogent with the majority of innovations in the development of batteries being dedicated to reducing the overall cost, while improving charge capacity and battery longevity. This means the need for innovation around a more recyclable battery unit has largely been ignored.
Luckily, things are starting to change. Driven by the enormous quantity of spent batteries and the influx of soon-to-be spent batteries from electric vehicles on the horizon, a number of companies are emerging to commercialize new battery-recycling technology. In fact, some of these companies have completely shifted the recycling process to ensure that 80-100 percent of resources are recovered in a closed-loop process. While these companies are still in the process of scaling up to become the widespread method of battery recycling and resource recovery, their potential positive impacts on the environment and resources shouldn’t be ignored.
While lithium-ion batteries are a key part in the transition away from carbon-based methods of transport, the mission to secure a clean transport future doesn’t end with the constant production of brand-new batteries. To ensure a positive impact on the environment, climate and society, it’s critical that effective and ethical closed-loop recycling and resource recovery options are prioritized, implemented and widely adopted to reduce battery waste, and ease the strain on available resources.
About Kunal Phalpher
Kunal Phalpher is the Chief Commercial Officer of Li-Cycle Corp. https://li-cycle.com/ He has extensive international experience in the lithium-ion battery and renewable energy sectors, with a focus primarily on strategy and business development.